Introduction
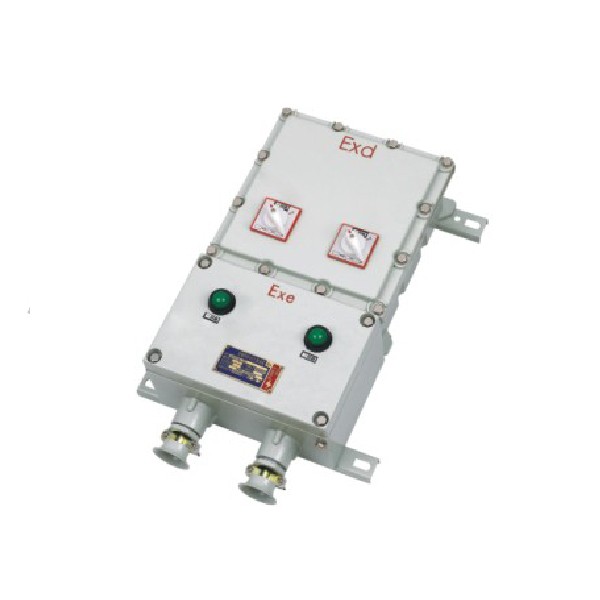
In a world where safety and efficiency are paramount, explosion-proof equipment plays a critical role in protecting lives and property from the hazards of explosive environments. This specialized sector of explosion proof manufacturing is designed to mitigate risks associated with flammable gases, vapors, and dusts, ensuring that industries can operate without fear of catastrophic incidents. As we delve into the nuances of this industry, we'll explore key players, industry standards, and what sets these products apart.
The Importance of Explosion-proof Equipment
Explosion-proof equipment is more than just a regulatory requirement; it is essential for safeguarding workers and facilities in hazardous locations. With industries such as oil and gas, chemical processing, and mining relying heavily on these solutions, understanding what are explosion proof products becomes vital for operational safety. By employing robust designs that adhere to stringent requirements for explosion proof standards, companies can significantly reduce the risk of explosions while maintaining productivity.
Key Players in Explosion-proof Manufacturing
The landscape of explosion proof manufacturing is populated by several key players who have established themselves as leaders in the field. Companies like Jinrong have become synonymous with high-quality explosion proof electrical equipment that meets international standards. These manufacturers not only innovate but also ensure compliance with regulations such as IEC standards for explosion proof applications—an essential aspect for any organization looking to implement Ex equipment meaningfully.
Insights into the Industry Standards
Navigating the complex web of industry standards can be daunting; however, understanding what is the IEC standard for explosion proof is crucial for manufacturers and end-users alike. These guidelines provide a framework that ensures safety through rigorous testing and certification processes tailored specifically for hazardous environments. Moreover, grasping what is the difference between ATEX and explosion proof helps clarify how different regions approach safety regulations—an important factor when selecting equipment suitable for various applications.
Understanding Explosion-proof Manufacturing
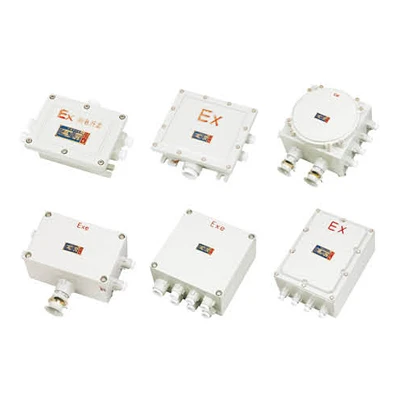
In the realm of explosion-proof manufacturing, safety and reliability are paramount. This sector focuses on creating products designed to operate in hazardous environments where flammable gases, vapors, or dust may be present. By understanding what explosion-proof products are and how they adhere to stringent standards, we can appreciate the critical role they play in various industries.
What are Explosion-proof Products?
Explosion-proof products are specially designed equipment that can contain an explosion within their enclosures, preventing it from igniting the surrounding atmosphere. These products include a variety of electrical devices such as lights, switches, and motors that meet specific safety standards to mitigate risks in volatile environments. The primary goal is to ensure that when using explosion proof electrical equipment, there is minimal risk of ignition under normal operating conditions.
Understanding what are explosion proof products also involves recognizing their applications across industries like oil and gas, chemical manufacturing, and mining. Each product must undergo rigorous testing to meet the requirements for explosion proof certification. This ensures they can withstand internal explosions without compromising safety or functionality.
The Role of IEC Standards in Safety
The International Electrotechnical Commission (IEC) plays a crucial role in establishing safety standards for explosion-proof manufacturing globally. The IEC standard for explosion proof equipment outlines essential guidelines that manufacturers must follow to ensure their products can effectively prevent ignition sources in hazardous locations. Compliance with these standards not only guarantees product integrity but also fosters trust among users who rely on this equipment daily.
Moreover, adherence to IEC standards helps streamline international trade by providing a universally recognized benchmark for quality and safety in explosive atmospheres. Manufacturers who align with these regulations demonstrate their commitment to producing reliable Ex equipment meaning safe for use across various sectors worldwide. Thus, understanding the role of IEC standards is vital for both manufacturers and consumers alike.
What is the Difference Between ATEX and Explosion Proof?
When discussing what is the difference between ATEX and explosion proof terminology arises frequently among professionals in the field of explosion proof manufacturing. ATEX refers specifically to European Union directives regarding equipment used in explosive atmospheres; it stands for Atmosphères Explosibles. In contrast, explosion proof is a broader term that encompasses various global certifications beyond just ATEX.
While both terms indicate compliance with safety measures intended to prevent explosions from occurring due to electrical devices or machinery, they cater to different regulatory frameworks based on geographic regions. For instance, while ATEX focuses on Europe’s stringent regulations, other countries may have their own sets of requirements—like NEC (National Electrical Code) in North America—defining what qualifies as safe for use within hazardous areas.
In summary, understanding these distinctions helps stakeholders navigate compliance processes more effectively while ensuring they select appropriate solutions tailored specifically for their operational environment—whether under ATEX guidelines or general explosion proof criteria.
The Evolution of Explosion-proof Technologies
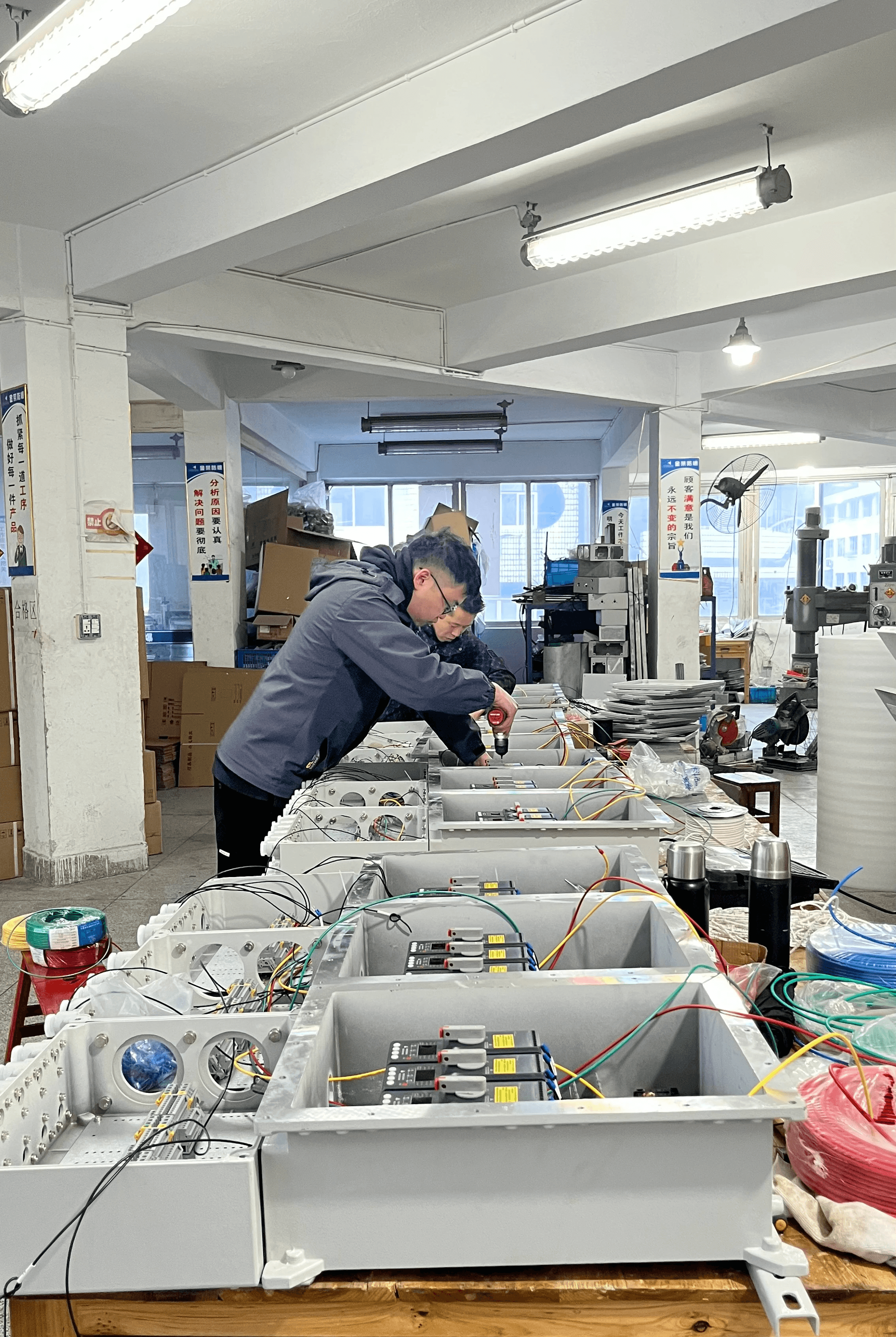
The evolution of explosion-proof technologies has been a fascinating journey, marked by innovation and adaptation to changing safety needs. From rudimentary designs intended to protect against the most basic hazards to sophisticated systems that leverage cutting-edge technology, explosion proof manufacturing has come a long way. This section explores the historical background of explosion-proof equipment, modern innovations that have reshaped the industry, and what the future holds for these critical safety solutions.
Historical Background of Explosion-proof Equipment
The roots of explosion-proof equipment can be traced back to the industrial revolution when machinery began operating in environments fraught with flammable gases and dust. Early attempts at creating safe electrical apparatuses led to the development of basic standards; however, it wasn't until the introduction of comprehensive regulations that true progress was made in explosion proof manufacturing. Notably, organizations like IEC (International Electrotechnical Commission) laid down essential guidelines, defining what are explosion proof products and establishing benchmarks for safety.
Over time, key milestones emerged in this field: from the first ATEX directives in Europe to rigorous IEC standards that dictated how manufacturers should design their products for hazardous environments. Understanding what is the IEC standard for explosion proof not only helped manufacturers comply with regulations but also ensured that their products were genuinely safe for use in explosive atmospheres. As industries grew and diversified, so did the need for more advanced solutions tailored to specific applications.
Modern Innovations and Their Impacts
Today’s explosion proof electrical equipment is a testament to human ingenuity and technological advancement. With innovations such as smart sensors and IoT integration, modern systems can provide real-time monitoring and diagnostics, significantly enhancing safety measures in hazardous environments. These advancements allow industries not only to meet compliance requirements but also improve operational efficiency—demonstrating how crucial it is to stay ahead in explosion proof manufacturing.
Moreover, understanding what are the requirements for explosion proof equipment has become more complex yet essential as technology evolves. Manufacturers now focus on creating Ex equipment meaning devices that not only comply with existing regulations but also anticipate future needs through design flexibility and adaptability. The impact of these innovations extends beyond mere compliance; they foster a culture of safety that permeates organizations reliant on such technologies.
The Future of Explosion-proof Manufacturing
Looking ahead, the future of explosion-proof manufacturing appears bright yet challenging as new materials and technologies emerge at an unprecedented pace. As companies strive for greater efficiency while maintaining stringent safety standards, we can expect further refinements in both product design and regulatory frameworks around what is the difference between ATEX and explosion proof classifications—an important distinction every manufacturer must navigate carefully.
In addition to technological advancements, sustainability will likely play a pivotal role in shaping future practices within this sector. Manufacturers will increasingly seek eco-friendly materials without compromising on safety or performance when producing their equipment designed for volatile environments. Ultimately, embracing innovation while adhering to established standards will define success in this evolving landscape—ensuring that businesses continue reaping benefits from certified Ex equipment while prioritizing worker safety above all else.
Key Manufacturers in the Explosion-proof Sector
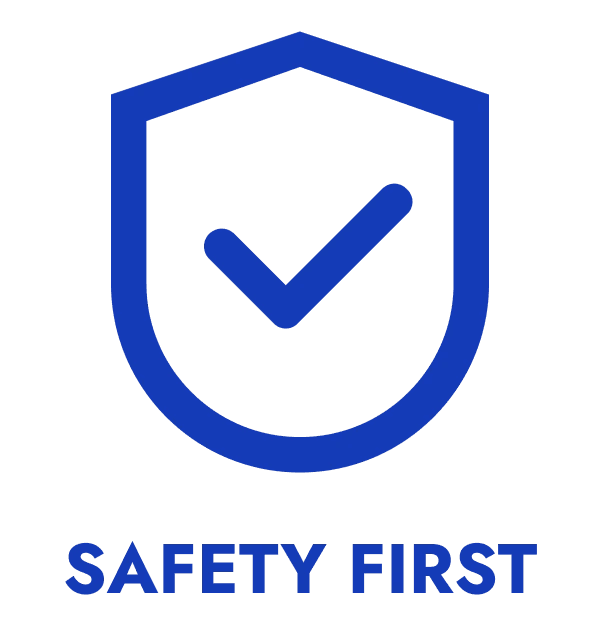
When it comes to explosion-proof manufacturing, a few key players stand out in the industry. These manufacturers not only produce high-quality explosion proof electrical equipment but also ensure compliance with stringent safety standards. Among them, Jinrong has carved a niche as a leader in Ex-proof solutions, setting benchmarks for innovation and reliability.
Jinrong: A Leader in Ex-proof Solutions
Jinrong is synonymous with excellence in explosion proof manufacturing, offering a wide range of products designed to withstand hazardous environments. Their commitment to adhering to international standards, such as IEC and ATEX regulations, ensures that their equipment meets the highest safety requirements for various industries. So, what is the difference between ATEX and explosion proof? While both terms refer to safety standards for equipment used in explosive atmospheres, ATEX specifically applies to European Union regulations, whereas explosion proof is often used more broadly.
The company’s portfolio includes various types of explosion proof products that cater to diverse applications—from oil and gas extraction to chemical processing facilities. What are the requirements for explosion proof equipment? Jinrong’s designs focus on maintaining structural integrity under extreme conditions while also being user-friendly and easy to install. Their innovative approach allows them to stay ahead of the curve by integrating modern technology into their traditional manufacturing processes.
In addition to producing top-notch Ex equipment meaning safe operation within explosive environments, Jinrong emphasizes quality assurance throughout its production cycle. They implement rigorous testing protocols aligned with what is the IEC standard for explosion proof devices—ensuring that each product not only meets but exceeds industry expectations. With a keen eye on future advancements, Jinrong continues to invest in research and development aimed at enhancing the efficiency and functionality of their products.
Regulations and Requirements for Explosion-proof Equipment
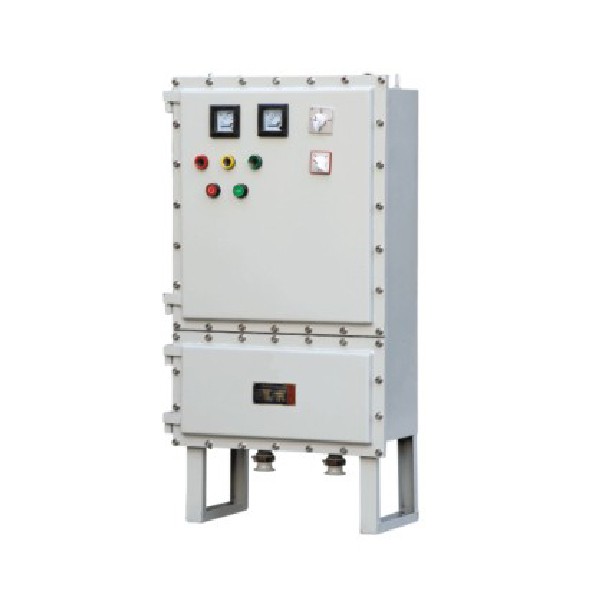
In the realm of explosion proof manufacturing, adhering to regulations is crucial for ensuring safety and compliance. The requirements for explosion proof products are designed to mitigate risks associated with hazardous environments where flammable gases or dust may be present. Understanding these regulations not only helps manufacturers create safer products but also protects end-users from potential disasters.
What are the Requirements for Explosion Proof?
The requirements for explosion proof equipment are stringent, reflecting the critical need for safety in hazardous areas. These standards dictate that explosion proof electrical equipment must be designed to contain any internal explosions without allowing flames or hot gases to escape into the surrounding atmosphere. Additionally, manufacturers must ensure that their products meet specific performance criteria set by international guidelines, such as what is the IEC standard for explosion proof applications.
To comply with these requirements, manufacturers must thoroughly test their products under various conditions to ensure they can withstand potential explosive atmospheres. This includes rigorous assessments of materials, construction methods, and operational capabilities of the equipment. Ultimately, understanding what are explosion proof products and their regulatory requirements is essential in creating reliable solutions that protect lives and property.
Navigating Compliance and Certification Processes
Navigating compliance and certification processes can be a daunting task in the world of explosion proof manufacturing. Manufacturers must familiarize themselves with both local regulations and international standards like ATEX (Atmosphères Explosibles) and IECEx (International Electrotechnical Commission System for Certification to Standards Relating to Equipment for Use in Explosive Atmospheres). Understanding what is the difference between ATEX and explosion proof certifications can help clarify which path best suits a manufacturer’s target market.
The certification process typically involves submitting detailed documentation about product design, testing results, and quality assurance measures to relevant authorities or notified bodies. Once approved, manufacturers receive certification marks indicating that their equipment meets all necessary safety standards—an essential step before reaching customers in industries reliant on Ex equipment meaning safe operations in explosive environments.
Moreover, staying updated on changing regulations is vital; non-compliance can lead to severe penalties or product recalls that could tarnish a company’s reputation.
The Importance of Quality Assurance
Quality assurance plays an indispensable role in ensuring the reliability of explosion proof electrical equipment throughout its lifecycle. Implementing robust quality control processes not only aids compliance with industry standards but also fosters customer trust by guaranteeing that products perform as intended under hazardous conditions. This commitment to quality ensures that every piece of equipment adheres strictly to what are the requirements for explosion proof certifications.
Moreover, continuous improvement practices within quality assurance frameworks help manufacturers adapt quickly to new technologies or changes in regulatory landscapes—keeping them competitive within an evolving market landscape characterized by rapid advancements in safety technology related to explosion-proof solutions. Investing time and resources into maintaining high-quality standards ultimately leads to safer working environments across various industries relying on certified Ex equipment.
In conclusion, navigating regulations while maintaining high-quality production practices forms the backbone of successful operations within this specialized sector of manufacturing.
Applications of Explosion-proof Electrical Equipment
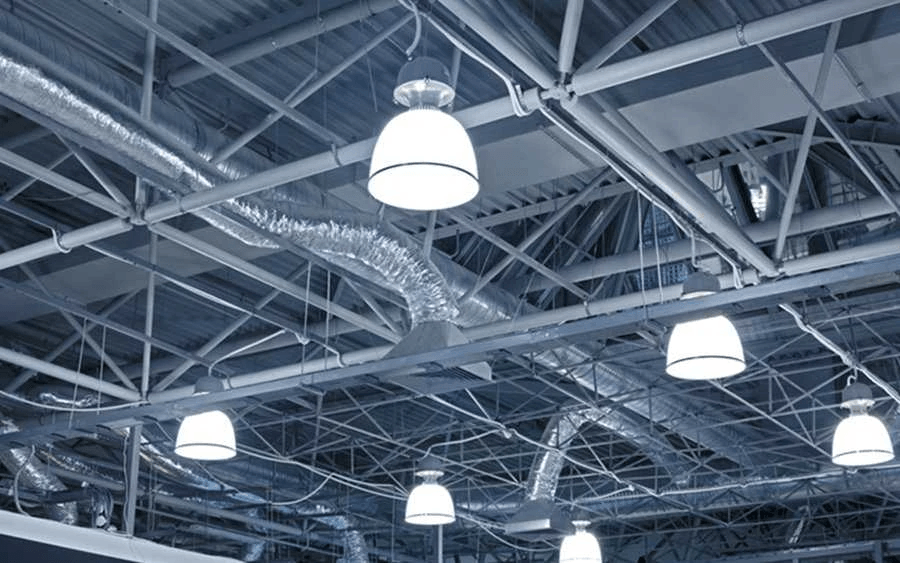
Explosion-proof electrical equipment is not just a niche market; it’s a necessity in various industries where the risk of explosion is prevalent. From oil rigs to chemical plants, these specialized products ensure safety and compliance with stringent regulations. Understanding what explosion-proof products are and their applications can greatly enhance workplace safety and operational efficiency.
Industries That Rely on Explosion-proof Solutions
Several industries depend heavily on explosion-proof manufacturing due to the hazardous environments they operate in. The oil and gas sector, for instance, frequently encounters flammable gases that necessitate the use of certified Ex equipment to prevent catastrophic incidents. Similarly, chemical manufacturing facilities require robust solutions that meet IEC standards for explosion proof to mitigate risks associated with volatile substances.
In addition to oil and gas and chemicals, industries like mining, pharmaceuticals, and food processing also utilize explosion-proof electrical equipment. Each sector has its unique challenges that demand tailored solutions; thus, understanding what the requirements for explosion proof entail is crucial for compliance and safety. As companies strive for operational excellence while ensuring worker safety, the demand for effective explosion-proof solutions continues to rise.
Case Studies of Successful Implementation
Real-world examples illustrate the importance of adhering to industry standards in explosion proof manufacturing. For instance, a major oil company implemented IEC-compliant Ex equipment across its offshore platforms after experiencing several near-misses with explosive atmospheres. By investing in high-quality explosion-proof products, they not only improved safety but also enhanced productivity by minimizing downtime caused by accidents.
Another notable case involves a pharmaceutical manufacturer that transitioned to using certified Ex equipment in their production lines handling volatile compounds. The result was a significant reduction in incidents related to chemical spills or explosions while maintaining compliance with ATEX regulations—showing what is the difference between ATEX and explosion proof truly means in practice: one focuses on European markets while another encompasses broader global standards.
These case studies highlight how crucial it is for businesses operating in hazardous environments to prioritize quality assurance when selecting their suppliers of explosion proof electrical equipment.
The Benefits of Using Certified Ex Equipment
Utilizing certified Ex equipment offers numerous advantages beyond mere compliance; it enhances overall workplace safety significantly while fostering trust among employees and stakeholders alike. Companies can rest assured knowing they’re meeting stringent requirements for explosion proof manufacturing by investing in tested products designed specifically for hazardous locations.
Moreover, employing such specialized solutions can lead to long-term cost savings through reduced insurance premiums and fewer workplace accidents—both vital factors contributing positively to a company's bottom line. Businesses gain peace of mind knowing that they are protected against potential liabilities associated with explosions or fires caused by inadequate safety measures.
Ultimately, choosing certified Ex equipment not only safeguards personnel but also strengthens an organization’s reputation as a responsible player within its industry—a win-win situation all around!
Conclusion
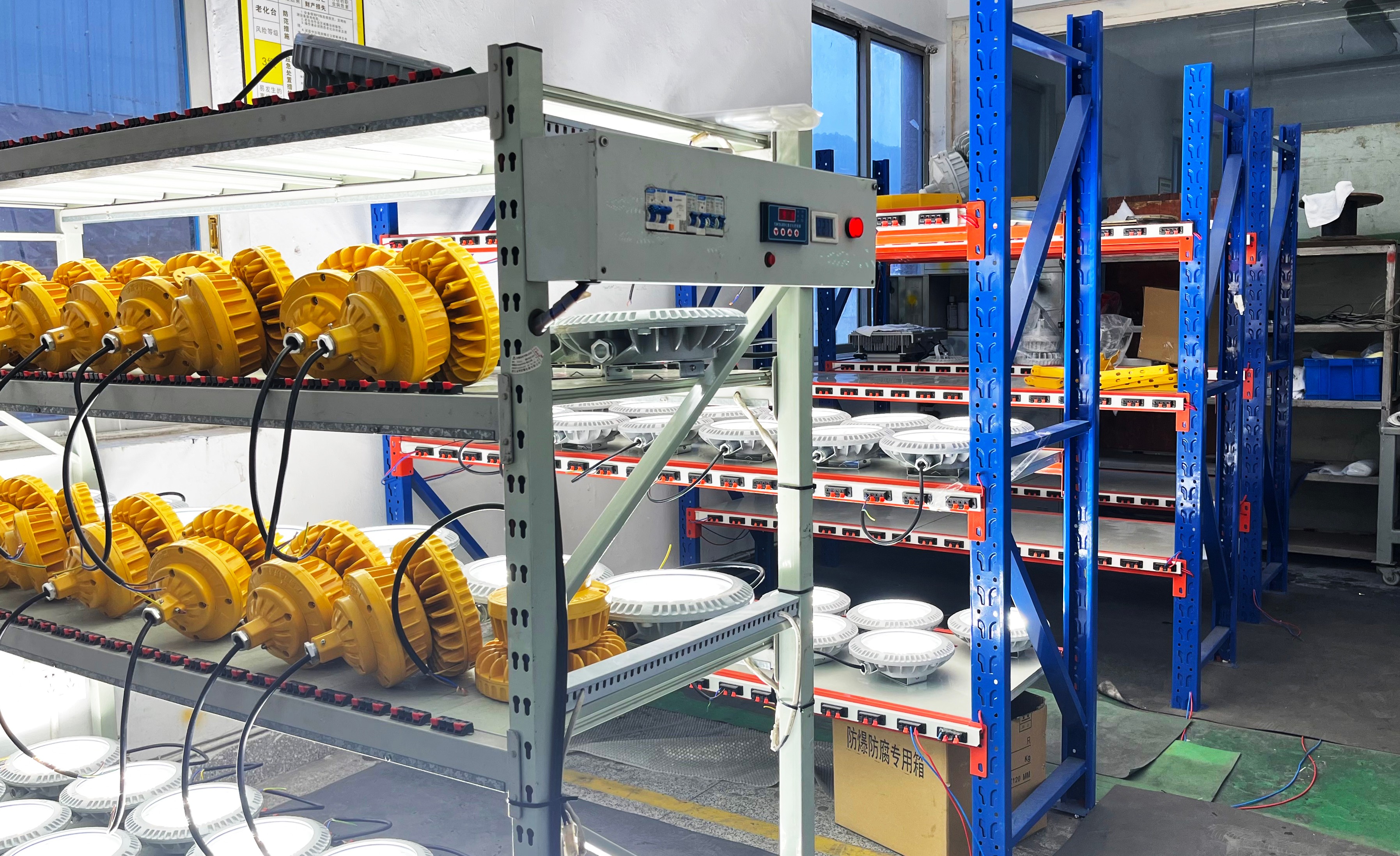
In the realm of safety and industrial innovation, explosion-proof manufacturing stands as a critical pillar. As industries evolve and expand, the demand for robust explosion-proof products continues to grow, driven by stringent regulations and the ever-present need for safety in hazardous environments. The future of this field is not just about compliance; it’s also about embracing new technologies that enhance efficiency while ensuring the highest standards of protection.
Exploring the Future of Explosion-proof Solutions
The future of explosion-proof solutions is bright and full of potential as advancements in technology pave the way for safer, more efficient equipment. Innovations such as smart sensors integrated into explosion proof electrical equipment are emerging, allowing for real-time monitoring and proactive safety measures. Additionally, understanding what is the IEC standard for explosion proof will become increasingly vital as we navigate through evolving industry requirements that demand higher levels of safety and performance.
As manufacturers continue to push boundaries, questions like What is the difference between ATEX and explosion proof? will gain prominence in discussions about global standards and certifications. The convergence of digital technology with traditional manufacturing processes will likely lead to new solutions that not only meet but exceed current expectations in explosion proof manufacturing.
How to Choose the Right Manufacturer
Choosing the right manufacturer in explosion-proof manufacturing isn't just about price; it's about quality assurance, reliability, and expertise in compliance with industry standards. Start by asking critical questions: What are the requirements for explosion proof certification? Does the manufacturer have a proven track record with certified Ex equipment meaning? Researching their history and customer reviews can provide insight into their reliability.
Look for manufacturers who are transparent about their processes and adhere strictly to IEC standards related to safety measures. Prioritize those who offer comprehensive support services throughout your project lifecycle—from initial consultation through installation—ensuring you have a partner invested in your success rather than just a supplier pushing products.
Building a Career in Explosion-proof Manufacturing
Building a career in explosion-proof manufacturing can be both rewarding and challenging due to its niche nature within broader industrial sectors. As industries increasingly prioritize safety compliance, experts knowledgeable about what are explosion proof products are becoming invaluable assets across multiple fields—from oil & gas to pharmaceuticals.
Pursuing relevant certifications or training programs focused on IEC standards can significantly enhance your employability within this sector. Networking with professionals already established in this field can also open doors; mentorship opportunities often yield insights into best practices while helping you navigate potential career paths that align with your interests.