Introduction
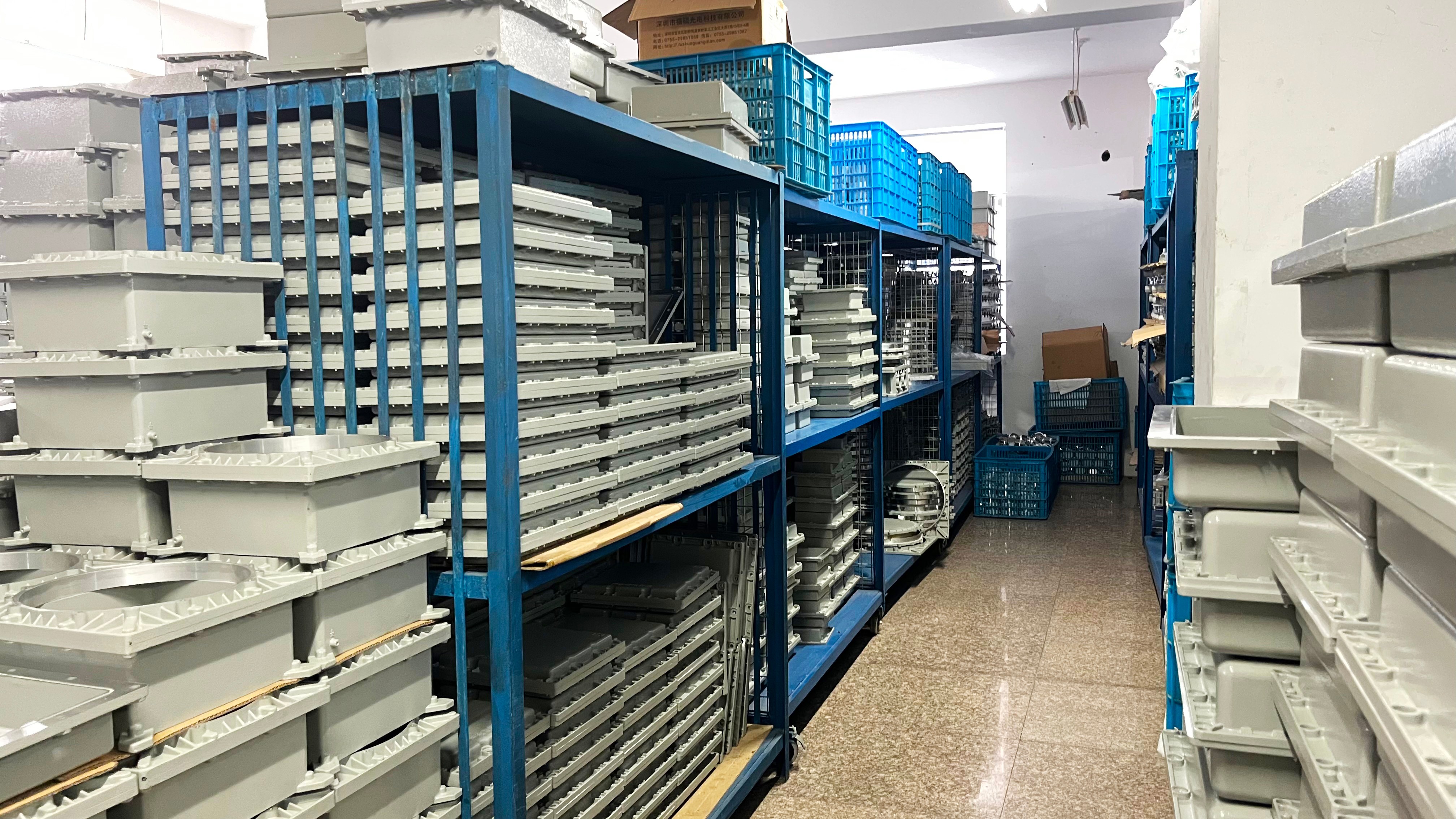
In an increasingly industrialized world, the need for safety in hazardous environments cannot be overstated. Understanding explosion proof standards is crucial for industries that handle flammable materials or operate in potentially explosive atmospheres. These standards offer guidelines to ensure that equipment, including explosion proof boxes, can withstand and contain explosions, preventing catastrophic incidents.
Understanding Explosion Proof Standards
Explosion proof standards are designed to protect both people and property from the dangers of explosions in hazardous areas. These standards encompass a variety of regulations and certifications, including ATEX (the European Union directive) and its US equivalent, which ensures that equipment meets specific safety requirements. When discussing what are the requirements for explosion-proof enclosures?, it’s essential to consider these regulations as they dictate how equipment should be designed and tested.
Importance of Safety in Hazardous Areas
Safety is paramount in environments where flammable gases or dust may be present; a single spark can lead to devastating consequences. Implementing proper explosion proof measures—such as using explosion proof junction boxes—helps mitigate these risks significantly. By prioritizing safety protocols in hazardous areas, industries not only protect their workforce but also safeguard their assets against potential losses.
Overview of ATEX and Explosion-Proof Boxes
ATEX stands for Atmosphères Explosibles and refers to regulations governing equipment used in explosive atmospheres within the EU. It sets forth compliance requirements that manufacturers must meet when producing products like explosion proof boxes to ensure their safe operation under hazardous conditions. While IEC (International Electrotechnical Commission) standards share similarities with ATEX, they are not identical; understanding these distinctions is vital for selecting the right solutions for your needs.
The Basics of ATEX Regulations
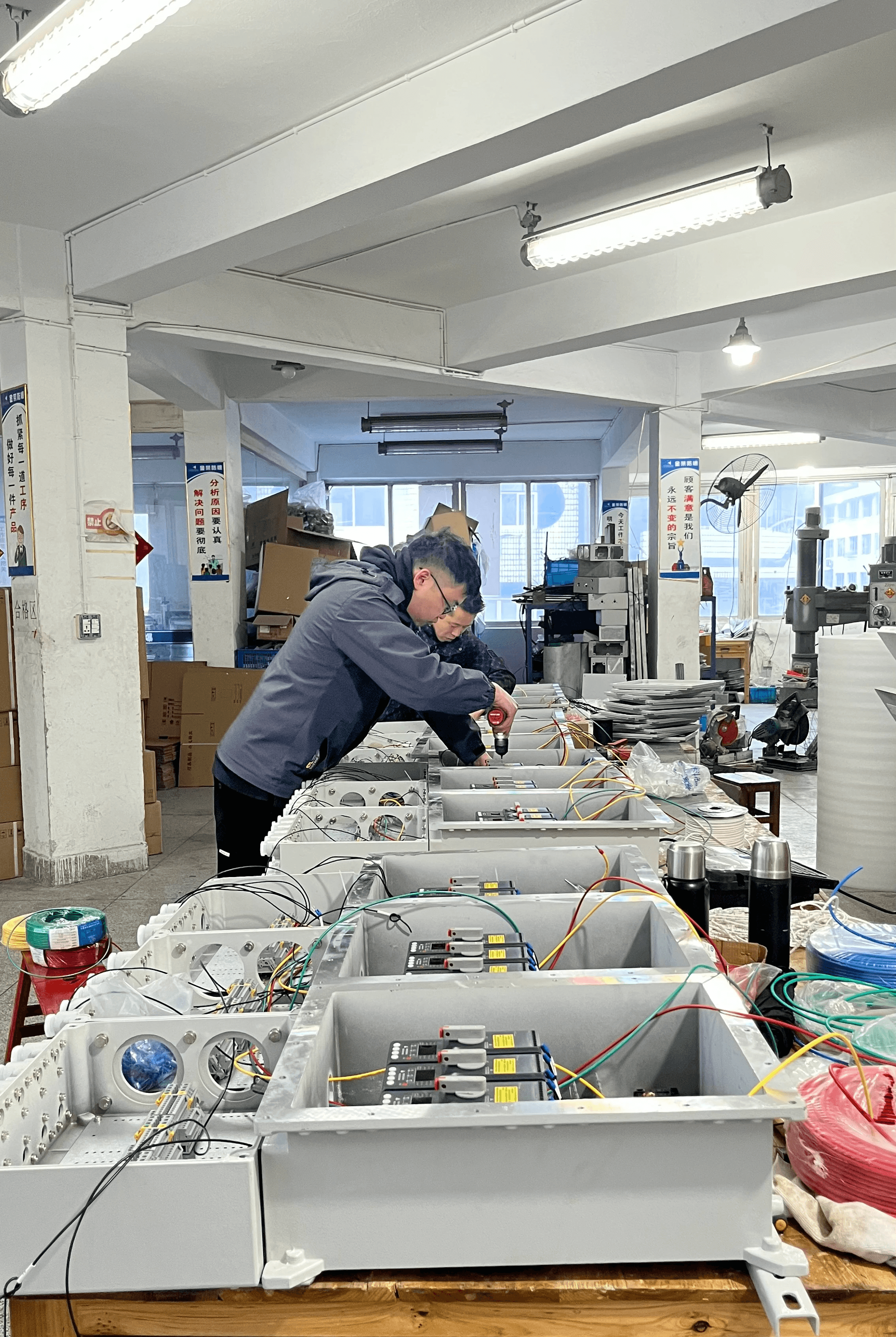
Understanding ATEX regulations is crucial for anyone dealing with hazardous environments, particularly when it comes to explosion proof boxes. The ATEX directive is a European Union directive that ensures equipment and protective systems intended for use in potentially explosive atmospheres are designed and manufactured to meet strict safety standards. This section will delve into what ATEX stands for, its compliance requirements, and its applications across various industries.
What ATEX Stands For
ATEX is an acronym derived from the French term ATmosphères EXplosibles, which translates to explosive atmospheres. This regulation focuses on the safety of equipment used in environments where flammable gases, vapors, or dust may be present. Understanding what ATEX represents helps industries implement the necessary explosion proof solutions, such as explosion proof boxes and junction boxes.
Key ATEX Compliance Requirements
The key compliance requirements under the ATEX directive include rigorous testing and certification processes to ensure that equipment can operate safely in hazardous conditions. Manufacturers must demonstrate that their products meet specific design standards tailored for explosive environments—this includes explosion proof enclosures that can withstand pressure from internal explosions without allowing flames or hot gases to escape. Additionally, understanding what are the requirements for explosion-proof enclosures is essential for ensuring compliance with these regulations.
Applications of ATEX in Industry
ATEX regulations find applications across various sectors such as oil and gas, chemical manufacturing, mining, and food processing—essentially anywhere flammable substances abound. In these industries, equipment like explosion proof junction boxes plays a vital role in maintaining safety by preventing ignition sources from causing catastrophic incidents. By ensuring adherence to ATEX standards, companies not only protect their workforce but also enhance operational efficiency while minimizing risks associated with hazardous materials.
Exploring Explosion-Proof Boxes
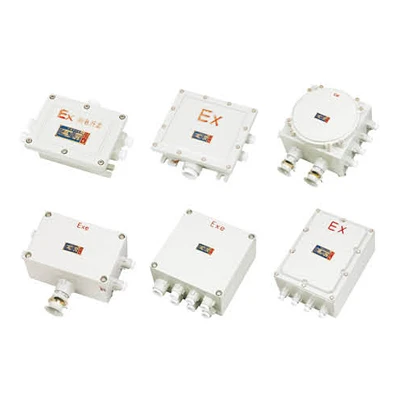
These enclosures are designed to contain any explosions that may occur inside, preventing them from spreading to the surrounding area. By using explosion proof boxes, industries can comply with safety standards while maintaining operational efficiency.
Definition and Purpose of Explosion Proof Boxes
Explosion proof boxes are specially designed enclosures that house electrical components and prevent the ignition of flammable gases or dust in hazardous locations. Their primary purpose is to ensure that any internal explosion is contained within the box itself, thereby protecting both personnel and equipment outside. These boxes are crucial for industries such as oil and gas, chemical manufacturing, and mining where volatile substances may be present.
Key Features of Explosion Proof Boxes
One of the defining features of explosion proof boxes is their robust construction, often made from materials like aluminum or stainless steel which can withstand high pressure and temperature fluctuations. They also come equipped with sealed joints and gaskets to prevent any ingress of dust or moisture which could compromise their integrity. Additionally, many explosion proof junction box options include features like corrosion resistance and impact protection, making them suitable for a variety of challenging environments.
Common Uses in Hazardous Environments
Explosion proof boxes find their place in numerous applications across various industries where hazardous conditions exist. Common uses include housing electrical connections in refineries, protecting instrumentation in chemical plants, and securing junctions in mining operations where methane gas might be present. Given their importance for compliance with regulations such as ATEX (and its US equivalent), these enclosures help mitigate risks associated with explosive atmospheres effectively.
Key Differences Between ATEX and Explosion-Proof
When it comes to safety in hazardous areas, understanding the differences between ATEX and general explosion-proof standards is crucial. While both aim to protect against explosions, they do so through different frameworks and regulations. This section will break down the certification processes, design standards, and environmental considerations that set them apart.
Certification Processes Explained
The certification processes for ATEX and general explosion-proof enclosures vary significantly. ATEX, which stands for ATmosphères EXplosibles, is a European directive that requires products used in potentially explosive atmospheres to undergo rigorous testing by notified bodies. In contrast, explosion-proof boxes in the U.S., such as the explosion proof junction box 1/2 inch, must comply with National Electrical Code (NEC) standards and are often certified by organizations like Underwriters Laboratories (UL).
Understanding these certification processes helps businesses determine what are the requirements for explosion-proof enclosures in their specific regions. For instance, while an ATEX-certified product may be acceptable in Europe, it might not meet U.S. standards without additional certifications. Therefore, companies operating internationally must navigate these differing requirements carefully.
Design Standards Unique to Each
Design standards also differ between ATEX-compliant products and those labeled as explosion-proof under U.S. regulations. ATEX guidelines focus on minimizing ignition sources while ensuring equipment can withstand certain pressures from explosions without breaching containment—essentially a fail-safe approach tailored to European markets. On the other hand, U.S.-based explosion proof boxes emphasize robust construction materials capable of containing internal explosions without allowing flames or hot gases to escape.
For instance, when selecting an explosion proof junction box for your facility, it's essential to consider whether it meets your local design standards—what materials are explosion-proof? The choice of materials plays a significant role here; while both systems prioritize safety, they might utilize different methodologies or material compositions based on regulatory needs.
Environmental Considerations
Environmental considerations further differentiate ATEX from general explosion-proof solutions. The ATEX directive takes into account various environmental factors when certifying equipment for use in explosive atmospheres—such as temperature ranges and humidity levels that could affect performance over time. Conversely, U.S.-based regulations may not always address these environmental factors as comprehensively but still ensure that materials used can withstand harsh conditions typical of industrial settings.
In practice, this means that businesses need to evaluate their operational environments closely when choosing between an ATEX-certified solution or a standard explosion proof box; after all, not every environment is created equal! Understanding what is the US equivalent of ATEX can also help organizations select appropriate solutions tailored to their specific hazardous conditions.
What Are the Requirements for Explosion-Proof Enclosures?
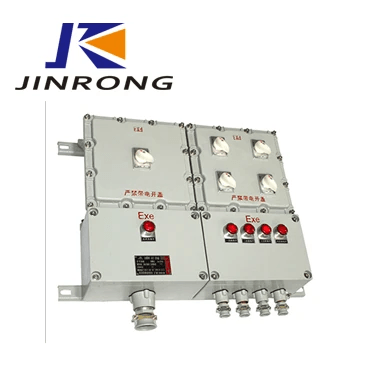
Essential Safety Standards
The foundation of any explosion-proof enclosure lies in its adherence to essential safety standards. In Europe, ATEX regulations govern the design and use of these enclosures, while in the United States, the National Electrical Code (NEC) provides guidelines on what is considered safe. Understanding what materials are explosion-proof and how they comply with these standards is vital for manufacturers and users alike.
Moreover, many industries rely on certifications like UL (Underwriters Laboratories) or IECEx (International Electrotechnical Commission Explosive) to validate that their explosion proof boxes meet necessary criteria. These certifications ensure that each product has undergone rigorous testing and evaluation before being deemed safe for use in hazardous locations. This compliance helps mitigate risks associated with flammable gases or dust present in various industrial settings.
Material Specifications and Durability
Material specifications play a significant role when discussing what are the requirements for explosion-proof enclosures. Typically constructed from robust materials like aluminum or stainless steel, these enclosures must resist corrosion and withstand harsh environmental conditions while maintaining their integrity during an explosive event. The durability of an explosion proof junction box is paramount; it should function effectively even under extreme temperatures or pressure changes.
Additionally, manufacturers must consider factors such as impact resistance and ingress protection ratings when selecting materials for their products. For example, an explosion proof junction box 1/2 inch may need specific thicknesses or coatings to ensure it meets industry standards while remaining lightweight enough for practical installation purposes. Ultimately, choosing high-quality materials directly influences both safety performance and longevity of these critical components.
Testing Methods for Compliance
To guarantee that explosion-proof enclosures meet necessary safety standards, rigorous testing methods are employed throughout the certification process. These tests assess various aspects such as pressure resistance, temperature fluctuations, and impact strength—ensuring that each enclosure can withstand potential explosive forces without failing catastrophically. Understanding how these tests work can help users appreciate why investing in quality products is essential.
Furthermore, manufacturers often conduct third-party evaluations to provide additional assurance regarding compliance with international regulations like ATEX or IECEx—giving buyers peace of mind when purchasing their explosion proof boxes. Regular re-testing also ensures ongoing compliance as technologies evolve over time; this vigilance helps maintain high safety levels across industries reliant on such equipment.
In conclusion, knowing what are the requirements for explosion-proof enclosures involves a comprehensive understanding of essential safety standards, material specifications, durability concerns, and rigorous testing methods used during certification processes—ultimately contributing to safer working environments across various sectors.
What Materials Are Explosion-Proof?
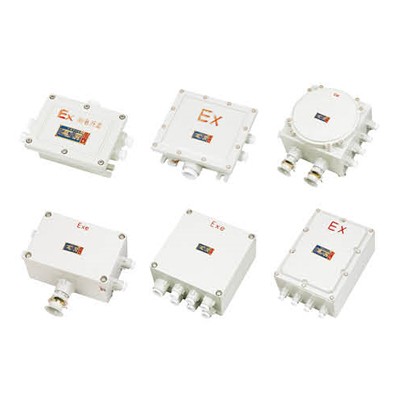
Common Materials Used in Construction
Explosion-proof boxes are typically constructed from a variety of materials, each chosen for its ability to withstand explosive atmospheres. Common materials include aluminum, stainless steel, and fiberglass-reinforced plastic (FRP). Aluminum offers a lightweight yet strong option, while stainless steel provides superior corrosion resistance; FRP is often favored for its non-conductive properties and high strength-to-weight ratio.
Pros and Cons of Various Materials
Each material used in explosion-proof junction box construction has its own set of advantages and disadvantages. For instance, aluminum is cost-effective and easy to machine but may not be suitable for highly corrosive environments. On the other hand, stainless steel is robust and durable but tends to be heavier and more expensive; FRP can resist harsh chemicals but might not offer the same level of mechanical strength as metals.
Selecting the Right Material for Your Needs
Choosing the right material for your explosion-proof solutions involves considering several factors such as environmental conditions, intended use, and budget constraints. If you’re operating in a highly corrosive environment or one with extreme temperatures, investing in high-quality stainless steel or specialized plastics may be necessary despite higher costs. Ultimately, balancing safety requirements with budget considerations will guide you toward selecting an appropriate material that meets what are the requirements for explosion-proof enclosures.
The Economic Aspect of Explosion Proof Solutions
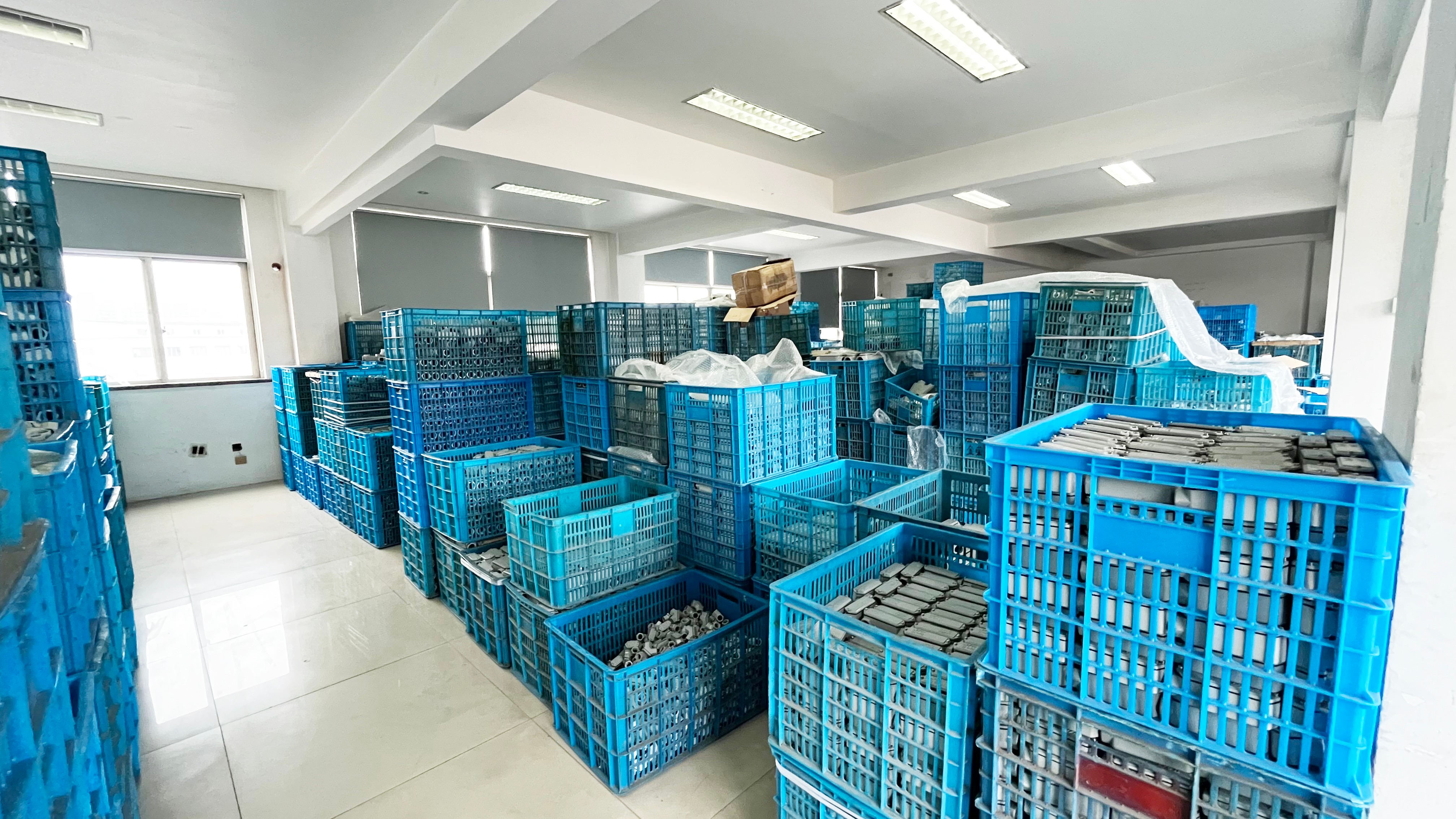
Explosion Proof Boxes Price Breakdown
The price of explosion proof boxes can vary widely based on several factors such as size, material, and specific features like ingress protection ratings. Generally, you might find basic models starting around a few hundred dollars, while more complex configurations can reach thousands. Additionally, specialized items like an explosion proof junction box 1/2 inch may have different pricing tiers depending on their specifications and compliance with standards.
It's important to note that while upfront costs are vital, long-term value should also be considered when assessing the price of explosion proof boxes. Investing in high-quality enclosures ensures durability and reliability over time, potentially saving money on replacements or repairs down the line. Thus, understanding what materials are explosion-proof plays a pivotal role in making economically sound choices.
Cost vs. Safety Considerations
Balancing cost against safety considerations is a tightrope walk many companies face when selecting explosion proof solutions. While it may be tempting to opt for cheaper alternatives to save money upfront, these options could compromise safety in hazardous areas where regulations demand strict adherence to standards like ATEX or IEC certifications. After all, what are the requirements for explosion-proof enclosures? They exist for a reason: to protect lives and property from catastrophic events.
Investing in reliable explosion proof boxes is not just about compliance; it's about safeguarding your workforce and assets against potential explosions caused by flammable gases or dusts. In this context, spending more initially could prevent devastating financial losses from accidents or regulatory fines later on. Therefore, weighing cost against potential risks is essential for any responsible business owner.
Investment in Quality vs. Cheap Alternatives
When considering whether to invest in quality versus settling for cheap alternatives in the realm of explosion proof solutions, one must remember that “you get what you pay for” often rings true—especially in hazardous environments that require stringent safety measures like those outlined by ATEX regulations or their US equivalents like NEC (National Electrical Code). High-quality explosion proof boxes are designed using robust materials specifically engineered to withstand extreme conditions while ensuring optimal performance.
Cheap alternatives may seem appealing at first glance but often lack necessary certifications and durability features required for safe operation under hazardous conditions—leading to potentially catastrophic outcomes down the line. For example, choosing an inferior quality explosion proof junction box might save money today but could lead to costly accidents tomorrow due to inadequate protection levels against explosive atmospheres.
In conclusion, investing wisely in well-manufactured products will not only enhance workplace safety but ultimately prove more economical over time by reducing risks associated with explosions and ensuring compliance with relevant standards like ATEX or IEC guidelines.
Conclusion
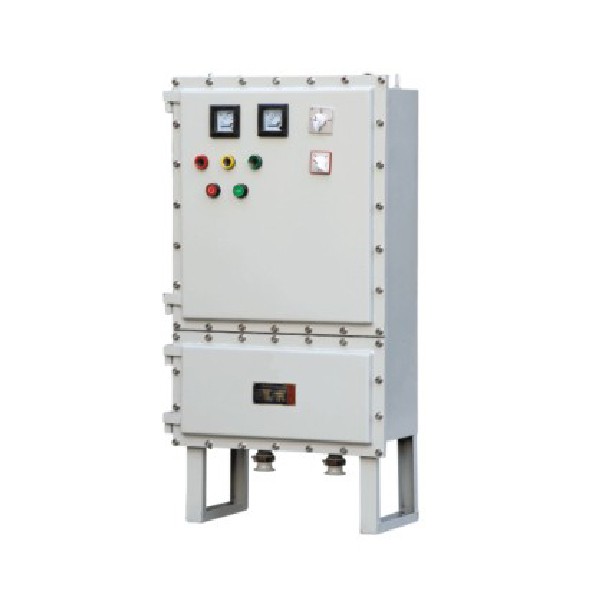
In summary, selecting the right explosion proof boxes is crucial for ensuring safety in hazardous environments. With a plethora of options available, understanding what are the requirements for explosion-proof enclosures and the materials that are explosion-proof will help you make an informed decision. The balance between safety, compliance, and cost should guide your selection process.
Choosing the Right Solution for Your Needs
Are you working in an area where flammable gases or dust are present? Understanding what materials are explosion-proof and their respective durability will ensure that your investment pays off in the long run.
Moreover, it’s essential to evaluate not just the price but also the reliability of these enclosures. Explosion proof junction box options vary significantly in price; however, cutting corners can lead to catastrophic consequences. Always prioritize quality over cheap alternatives when selecting your equipment.
The Role of Manufacturers Like Jinrong
Manufacturers like Jinrong play a pivotal role in delivering high-quality explosion proof solutions tailored to industry needs. They adhere strictly to ATEX regulations and other international standards—such as IEC—ensuring that their products meet safety requirements effectively. By choosing reputable manufacturers, you can rest assured that your explosion proof boxes will perform as intended under hazardous conditions.
Additionally, Jinrong's commitment to innovation means they often lead trends in materials technology and design standards unique to each market segment. This is particularly important when considering what is the US equivalent of ATEX; manufacturers must navigate various regulations while maintaining compliance with both local and international standards. Investing in products from established brands can save you time and reduce risks associated with subpar equipment.
Future Trends in Explosion-Proof Technology
As industries evolve, so too does technology around explosion-proof solutions. We can expect advancements in materials science leading to even more durable options that meet stringent safety criteria while being lightweight and cost-effective—a win-win situation! Furthermore, innovations such as smart monitoring systems integrated into explosion proof junction box designs may soon become standard practice.
Looking ahead, there’s also potential for increased collaboration between different regulatory bodies worldwide regarding standards like IEC and ATEX being harmonized for better global compliance measures. This could simplify procurement processes across borders while maintaining high safety standards across all types of environments where explosive hazards exist.
Ultimately, staying informed about future trends ensures that businesses remain compliant while maximizing operational efficiency through reliable equipment choices like well-designed explosion proof boxes.