Introduction
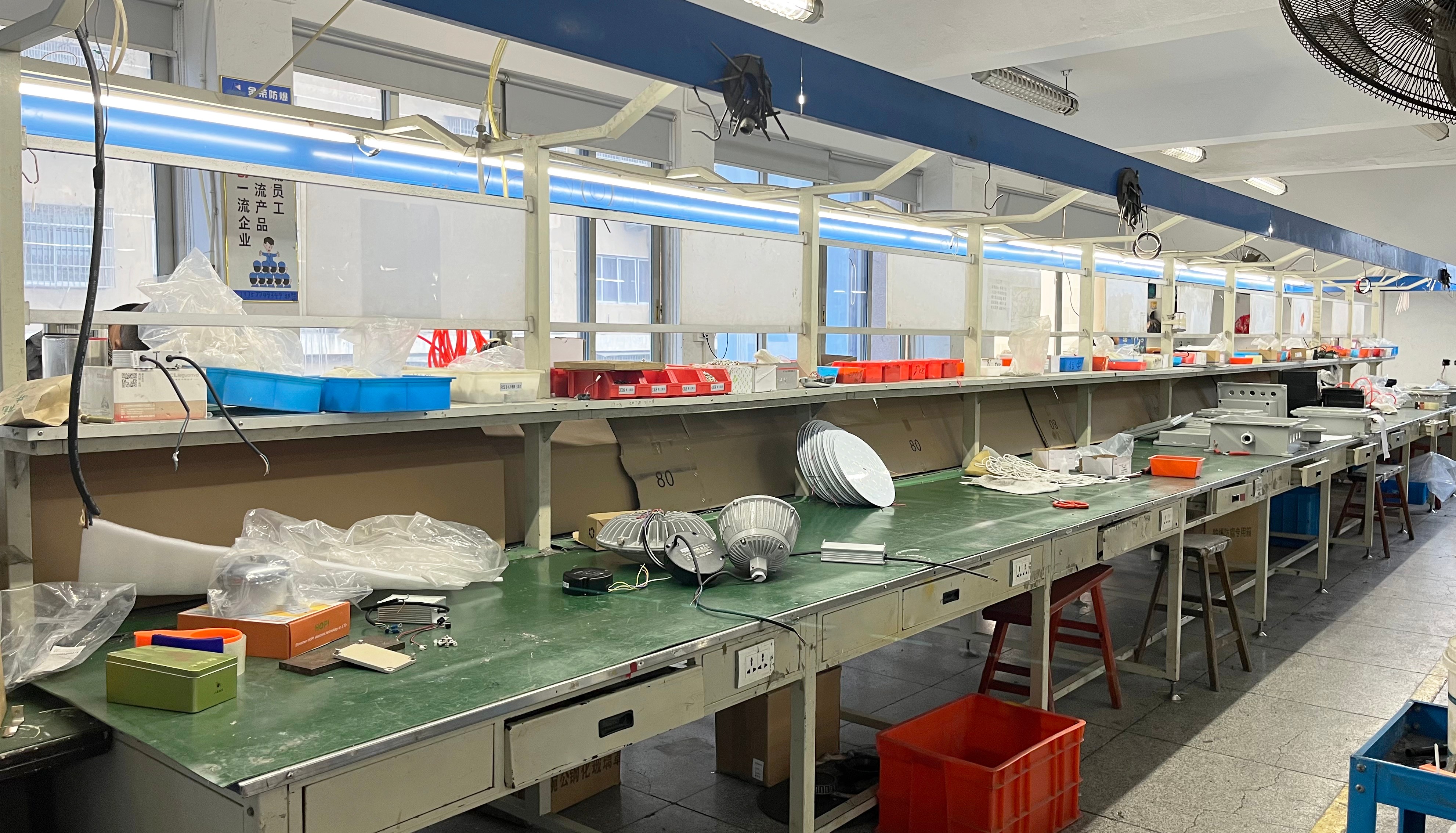
In today’s industrial landscape, safety standards are paramount to ensuring the well-being of workers and the integrity of operations. Understanding these safety standards is essential, especially when it comes to distinguishing between non-intrinsically safe equipment and other types of safety equipment. The complexities surrounding electrical circuits and their potential hazards necessitate a thorough comprehension of intrinsic safety concepts and the protective mechanisms in place.
Understanding Safety Standards in Industry
Safety standards serve as guidelines that dictate how equipment should be designed, tested, and operated to minimize risks in hazardous environments. These regulations are crucial for industries dealing with flammable materials or explosive atmospheres, where even a small spark can lead to catastrophic events. Familiarity with these standards helps organizations implement effective measures, ensuring compliance while safeguarding employees from dangers associated with non-intrinsically safe equipment.
The Role of Non-Intrinsically Safe Equipment
Non-intrinsically safe equipment plays a vital role in various industrial applications where the environment may not be classified as hazardous but still requires careful consideration. This type of equipment is designed without built-in protection against ignition sources but can still function effectively under controlled conditions. However, organizations must recognize the limitations and risks associated with using non-intrinsically safe tools alongside intrinsically safe devices.
Overview of IS Barriers
IS barriers are integral components that enhance safety by preventing potential ignition sources from reaching hazardous areas through electrical circuits. By isolating non-intrinsically safe equipment from potentially explosive environments, IS barriers provide an additional layer of protection that complements intrinsic safety measures. With products designed specifically for this purpose, industries can confidently operate within regulatory frameworks while ensuring robust safety certification compliance.
What is Non-Intrinsically Safe Equipment
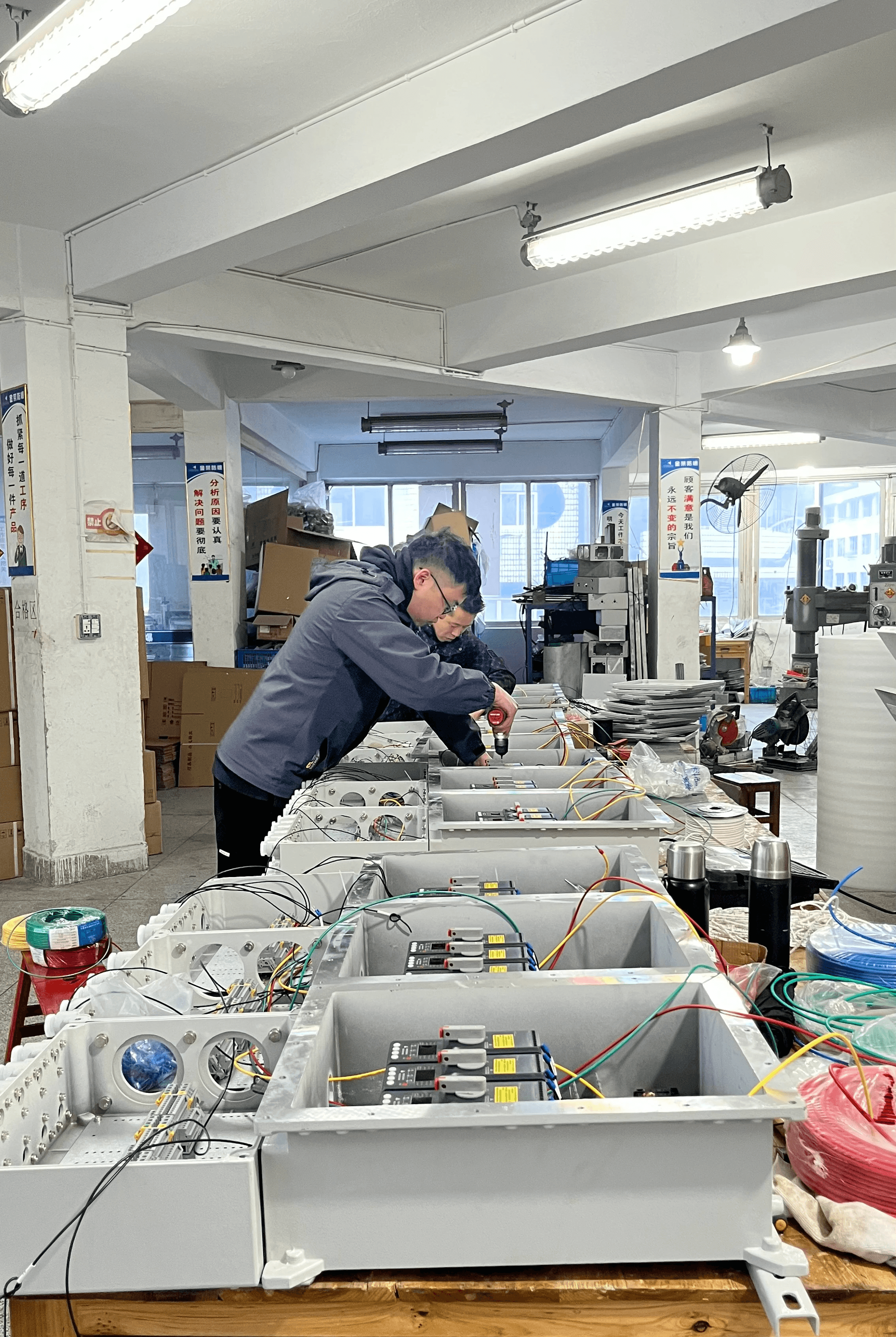
Non-intrinsically safe equipment refers to devices and systems that are not designed to prevent ignition in hazardous environments. Unlike their intrinsically safe counterparts, these tools can potentially spark or generate heat, which poses risks in explosive atmospheres. Understanding this distinction is crucial for industries where safety equipment must meet rigorous standards.
Definition and Examples
At its core, non-intrinsically safe equipment includes any electrical circuit or device that does not incorporate safety measures to eliminate the risk of explosion when used in flammable environments. Common examples include standard electrical tools, non-certified mobile devices like an intrinsically safe cell phone, and industrial machinery lacking explosion-proof modifications. These devices can operate efficiently under normal conditions but may become hazardous if exposed to volatile substances.
Common Applications in Industry
Non-intrinsically safe equipment finds its place in various industries where the environment is less volatile or controlled, such as manufacturing plants or assembly lines. For instance, construction sites often utilize standard power tools that don’t require stringent safety certification because they are situated away from explosive risks. However, there are situations where this equipment might inadvertently enter hazardous zones, necessitating careful monitoring and adherence to safety protocols.
Limitations and Risks
The primary limitation of non-intrinsically safe equipment lies in its susceptibility to causing ignition sources within explosive atmospheres. While it may be suitable for certain applications, using such devices without proper precautions can lead to catastrophic incidents including fires or explosions. Additionally, the absence of safety certification means that operators must remain vigilant about compliance with industry regulations and best practices when deploying these tools in sensitive environments.
The Intrinsic Safety Concept Explained
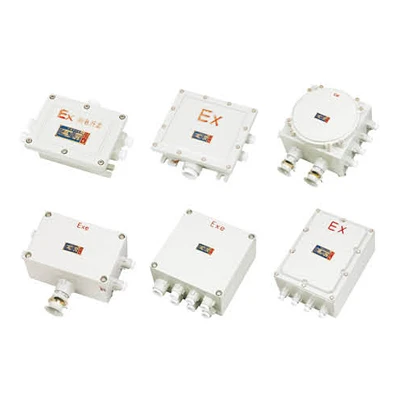
Intrinsic safety is a design principle aimed at preventing the ignition of hazardous atmospheres by limiting the energy available for potential ignition sources. This approach is particularly crucial in environments where flammable gases, vapors, or dust are present. By ensuring that electrical circuits operate within safe energy limits, intrinsic safety provides a reliable means of protecting both personnel and equipment.
Intrinsically Safe Meaning
The term intrinsically safe refers to equipment and wiring systems designed to operate safely in explosive atmospheres without the need for additional protective measures. Essentially, it means that even if there’s a fault or failure in the system, the energy released will not be enough to ignite any surrounding hazardous materials. This concept is vital for industries utilizing non intrinsically safe equipment, as it sets a benchmark for safety standards.
In practical terms, intrinsically safe devices are equipped with features that limit their electrical current and voltage output. For instance, an intrinsically safe cell phone can be used in oil refineries without fear of igniting flammable gases due to its carefully controlled energy levels. Understanding this meaning helps organizations make informed choices about their safety equipment.
How It Compares to Explosion Proof Equipment
While both intrinsic safety and explosion proof equipment aim to protect against ignitions in hazardous areas, they employ different methodologies. Explosion proof systems are designed to contain any explosion within their enclosure; however, this does not prevent an explosion from occurring in the first place. In contrast, intrinsic safety prevents any dangerous conditions from arising altogether by limiting energy levels within electrical circuits.
Another key difference lies in installation and maintenance: explosion proof equipment often requires heavy enclosures and can be cumbersome to install or maintain compared to intrinsically safe devices which often do not require such robust housing. Moreover, when using non intrinsically safe equipment alongside explosion proof gear, there’s always a risk of creating unsafe conditions if not managed correctly—something intrinsic safety aims to eliminate entirely.
Ultimately, while both approaches have their merits depending on specific applications and environments, intrinsic safety offers a more proactive approach towards hazard prevention rather than just containment.
Key Advantages of Intrinsic Safety
One major advantage of intrinsic safety is its inherent simplicity; by reducing complexity in design and installation processes compared to explosion proof solutions, it allows for easier integration into existing systems without extensive modifications. Additionally, because intrinsically safe devices don’t rely on heavy casings or barriers like traditional explosion-proof methods do, they tend to be lighter and more portable—making them ideal for dynamic work environments.
Furthermore, compliance with safety certification standards becomes more streamlined when using intrinsically safe technology since these devices are often already pre-certified for use in hazardous locations around the globe. This helps companies save time during audits while ensuring they meet regulatory demands across different regions effectively.
Lastly—and perhaps most importantly—intrinsic safety fosters a culture of awareness regarding potential hazards among employees who utilize these technologies daily; understanding how their tools work promotes safer practices overall while minimizing risks associated with non intrinsically safe equipment usage.
The Function of IS Barriers
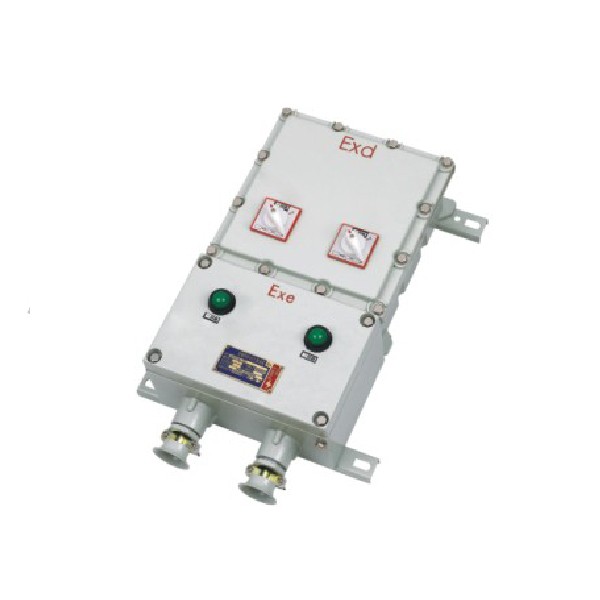
IS barriers are essential components in the realm of electrical safety, particularly when dealing with non-intrinsically safe equipment. Their primary purpose is to ensure that any potential energy released due to faults or surges does not ignite hazardous atmospheres. By creating a protective interface, these barriers allow for the safe operation of various electrical circuits in environments where risks are heightened.
Definition and Purpose
Intrinsic safety is a concept that revolves around preventing ignition sources in explosive atmospheres through careful design and engineering practices. IS barriers specifically serve as a safeguard by limiting the energy available to electrical circuits, thereby reducing the risk of sparks or heat generation that could lead to an explosion. In essence, their purpose is to maintain safety compliance while allowing non-intrinsically safe equipment to function effectively within hazardous areas.
How IS Barriers Protect Electrical Circuits
IS barriers protect electrical circuits by isolating non-intrinsically safe equipment from potentially dangerous environments. They achieve this by restricting both voltage and current levels, ensuring that any fault conditions remain below thresholds that could cause ignition. This proactive approach not only enhances safety but also aligns with various safety certification standards required across different industries.
In practical terms, when an electric circuit experiences a fault, such as a short circuit or overload, the IS barrier acts like a shield—preventing excessive energy from reaching sensitive components or igniting flammable materials nearby. By doing so, these barriers create a safer operational environment for devices like intrinsically safe cell phones and other electronic gadgets commonly used in industrial settings.
Examples of IS Barrier Products
There are numerous products available on the market designed specifically as IS barriers for various applications across industries. For instance, companies like Jinrong offer devices that integrate seamlessly with existing systems while providing robust protection against hazardous conditions. These products often include isolators and signal conditioners tailored for specific needs, ensuring compliance with intrinsic safety standards without compromising functionality.
Another notable example includes barrier modules used in conjunction with sensors and actuators; they play a pivotal role in maintaining operational integrity while safeguarding personnel from potential dangers associated with non-intrinsically safe equipment. Additionally, some advanced models feature built-in diagnostics that enhance reliability and facilitate maintenance checks—an essential aspect of any effective safety equipment strategy.
Safety Certification and Compliance
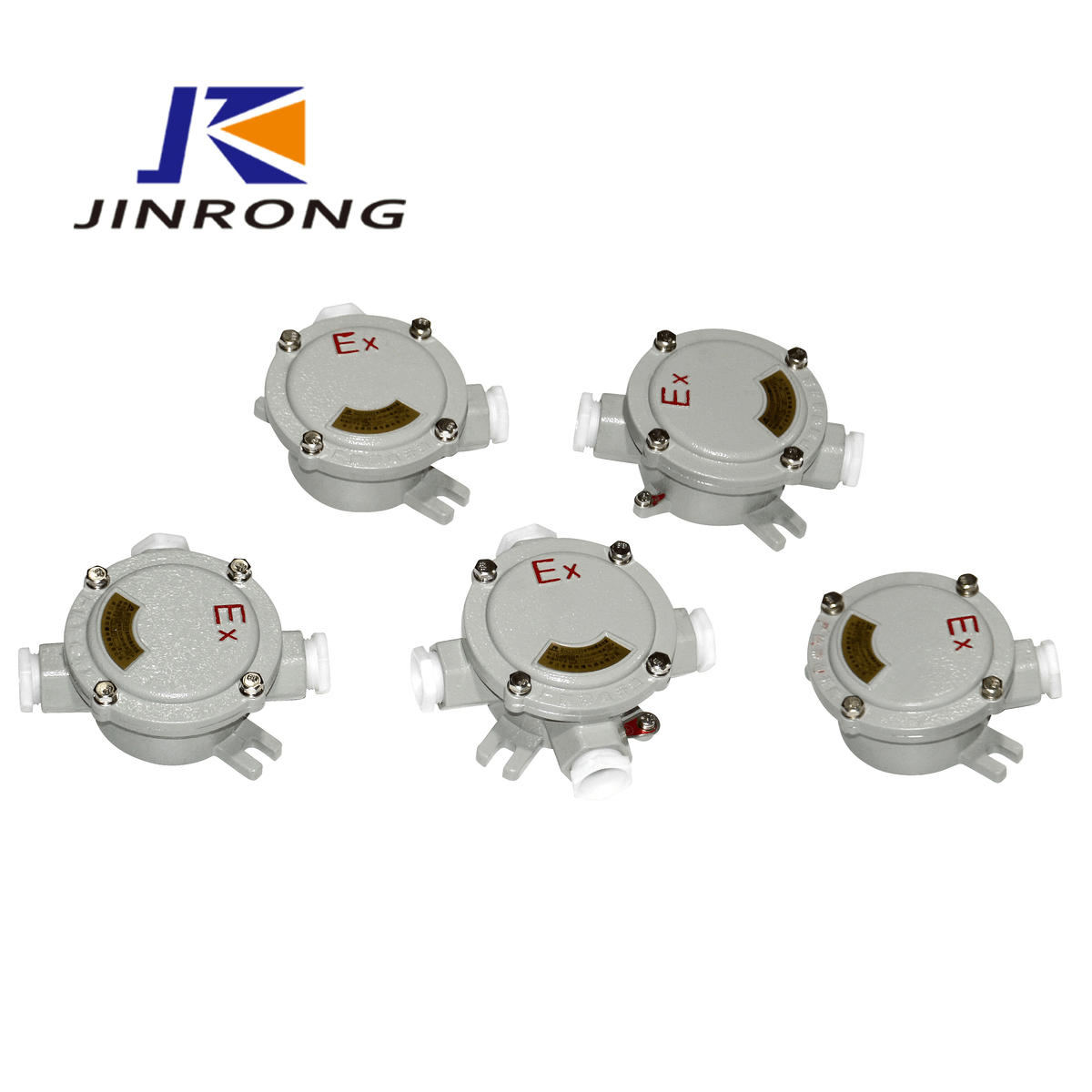
In the world of industrial safety, certification is not just a box to tick; it’s a fundamental pillar that ensures non-intrinsically safe equipment operates within established safety parameters. Without robust safety certification, the risk of accidents rises significantly, particularly in hazardous environments where electrical circuits are involved. This is why understanding safety certification and compliance is essential for both manufacturers and end-users of safety equipment.
Importance of Safety Certification
Safety certification acts as a guarantee that equipment meets specific standards designed to protect users from potential hazards. For non-intrinsically safe equipment, this assurance is critical as it helps mitigate risks associated with electrical circuits that could lead to explosions or fires in volatile environments. Moreover, possessing proper certifications enhances consumer trust and can often be a legal requirement for operating in certain regions.
Regulatory Standards in Different Regions
Different regions have varying regulatory standards governing the use of safety equipment, particularly concerning intrinsic safety and explosion-proof equipment. In Europe, for instance, ATEX directives dictate stringent requirements for devices used in potentially explosive atmospheres, while North America follows National Electrical Code (NEC) guidelines for hazardous locations. Understanding these regional differences is crucial for companies looking to ensure compliance with local laws while utilizing non-intrinsically safe equipment safely.
How Jinrong Ensures Compliance
At Jinrong, compliance isn’t just an afterthought; it’s embedded into our operational DNA. We rigorously test our products against international standards to ensure they meet or exceed safety certification requirements relevant to various markets. Our commitment ensures that even when dealing with non-intrinsically safe equipment, we provide solutions that prioritize intrinsic safety principles without compromising on quality or performance.
Real-World Applications and Case Studies
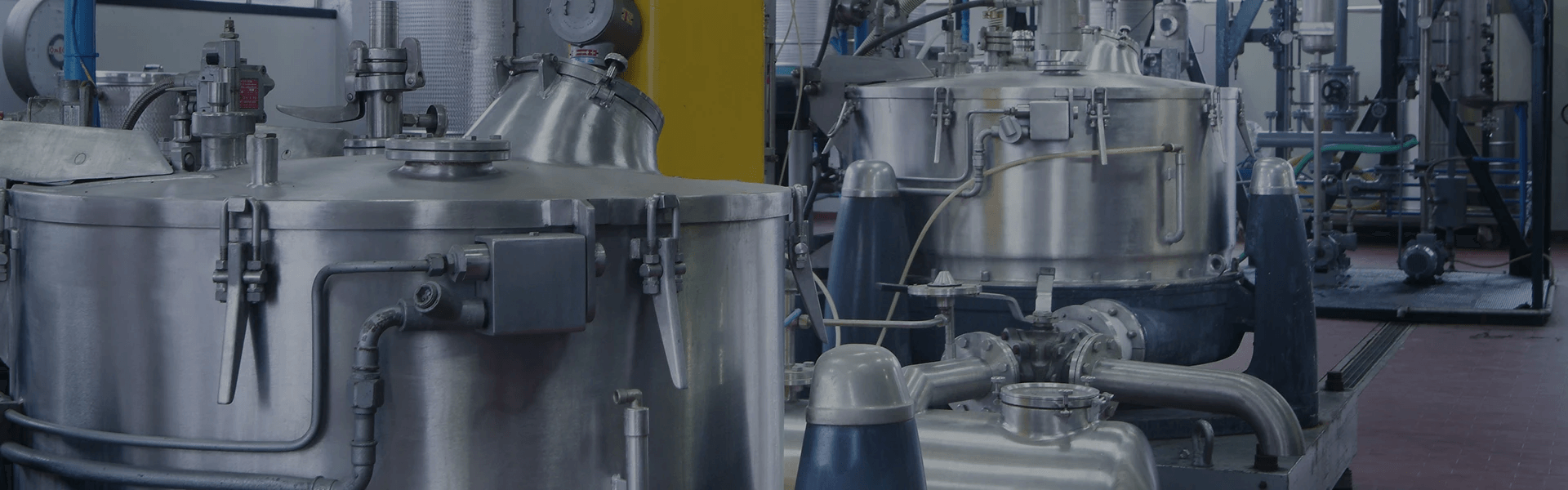
In the realm of industrial safety, understanding the real-world applications of non-intrinsically safe equipment is crucial. Various industries employ this type of equipment to enhance productivity while managing risks associated with hazardous environments. From oil and gas to chemical manufacturing, these sectors utilize non-intrinsically safe equipment in conjunction with IS barriers to ensure operational efficiency and safety compliance.
Industries Utilizing Non-Intrinsically Safe Equipment
Non-intrinsically safe equipment finds its place across several industries where explosive atmospheres are a concern. The oil and gas industry, for instance, often relies on this type of equipment for drilling operations, where traditional safety measures must be complemented by robust IS barriers. Similarly, the chemical manufacturing sector uses non-intrinsically safe devices for monitoring processes, necessitating stringent safety certification to mitigate risks associated with electrical circuits.
The pharmaceutical industry also utilizes non-intrinsically safe equipment in its production lines, ensuring that processes remain efficient without sacrificing safety standards. In environments where volatile substances are handled, such as paint shops or grain silos, the right combination of intrinsic safety measures and explosion-proof equipment becomes essential in preventing accidents. Understanding how these industries implement non-intrinsic solutions gives insight into balancing productivity and safety.
Success Stories from Jinrong Clients
Jinrong has a rich portfolio of clients who have successfully integrated IS barriers with their existing non-intrinsically safe equipment setups. One notable success story comes from a major petrochemical plant that faced frequent electrical circuit failures due to hazardous conditions. By implementing Jinrong's IS barriers alongside their existing systems, they significantly reduced downtime while enhancing overall operational safety.
Another client in the pharmaceutical sector reported remarkable improvements after adopting Jinrong's solutions; they were able to maintain compliance with stringent regulatory standards while utilizing their existing non-intrinsically safe equipment more efficiently than ever before. The introduction of intrinsically safe cell phones into their workflow allowed for seamless communication without compromising safety protocols during critical operations. These success stories highlight how strategic implementation can lead to improved outcomes.
Lessons Learned from Implementing IS Barriers
Implementing IS barriers alongside non-intrinsically safe equipment offers valuable lessons for organizations aiming for enhanced safety compliance. One key takeaway is the importance of thorough training; employees must understand both intrinsic safety concepts and how to effectively use the new systems introduced into their work environment. This knowledge fosters a culture of awareness around potential hazards related to electrical circuits and other risks associated with explosion-proof equipment.
Another lesson learned is that regular maintenance is vital; even when using certified safety equipment, neglecting upkeep can lead to failures that compromise worker safety or result in costly downtime. Organizations have discovered that maintaining an ongoing dialogue about best practices between teams ensures everyone remains vigilant regarding potential hazards associated with their specific applications of non-intrinsic technology. Ultimately, these lessons underscore that effective implementation requires more than just installing new gear—it involves cultivating an informed workforce committed to maintaining high standards of operational integrity.
Conclusion
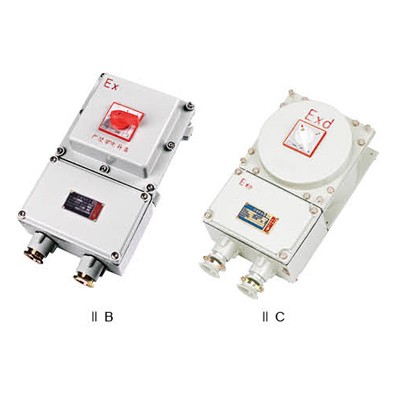
In summary, understanding the distinctions between non-intrinsically safe equipment and IS barriers is crucial for safety in hazardous environments. Non-intrinsically safe equipment can pose risks if not properly managed, while IS barriers provide an essential layer of protection by ensuring electrical circuits remain safe under potentially explosive conditions. As industries evolve, recognizing these differences will help organizations make informed decisions regarding their safety equipment.
Key Differences Between Non-Intrinsically Safe Equipment and IS Barriers
The fundamental difference lies in how each type of equipment handles risk; non-intrinsically safe equipment operates without built-in safeguards against ignition sources, whereas IS barriers are designed to limit energy levels to prevent explosions. In practical terms, this means that while non-intrinsically safe devices can be used in certain environments, they require careful monitoring and management to mitigate risks associated with electrical circuits. On the other hand, IS barriers enhance safety by ensuring that even if a fault occurs, the energy released is insufficient to ignite a hazardous atmosphere.
The Future of Safety Equipment in Hazardous Areas
Looking ahead, the future of safety equipment in hazardous areas is likely to see increased integration of advanced technologies such as smart sensors and IoT capabilities within intrinsically safe devices. This evolution will not only improve operational efficiency but also enhance real-time monitoring and compliance with safety certification standards across various regions. As industries continue to prioritize worker safety and environmental responsibility, we can expect a growing reliance on both non-intrinsically safe equipment paired with robust IS barriers for comprehensive protection.
Making Informed Choices for Safety Compliance
Making informed choices about safety compliance involves understanding both the benefits and limitations of different types of safety equipment available on the market today. Organizations should evaluate their specific needs against regulatory standards while considering options like explosion proof equipment or intrinsically safe cell phones for field workers operating in dangerous environments. By prioritizing proper training and awareness around intrinsic safety concepts, businesses can ensure their teams are well-equipped to navigate potential hazards effectively.