Introduction
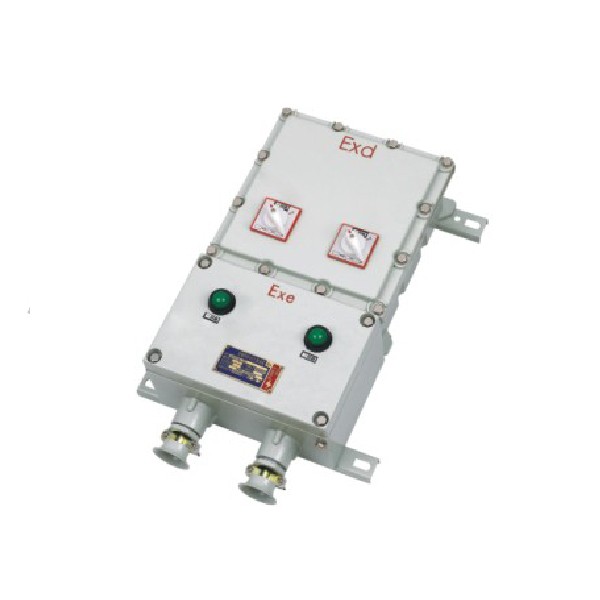
In a world where safety is paramount, understanding intrinsically safe equipment becomes essential, especially in hazardous environments. This type of equipment is designed to prevent ignition of flammable gases or dust by limiting the energy available for ignition. But what exactly qualifies as intrinsically safe?
Understanding Intrinsically Safe Equipment
Intrinsically safe equipment refers to devices that are engineered to operate safely in potentially explosive atmospheres by ensuring that any sparks or heat generated are insufficient to ignite hazardous materials. Examples of intrinsically safe electrical equipment include specialized sensors, communication devices, and tools used in industries like oil and gas, mining, and pharmaceuticals. By contrast, non-intrinsically safe equipment examples can lead to catastrophic failures if not managed properly.
Importance of Safety Standards
Safety standards play a crucial role in defining the requirements for intrinsically safe equipment, ensuring that such devices meet rigorous testing and certification processes before they can be deployed in risk-prone environments. Adhering to these standards not only protects personnel but also safeguards valuable assets from potential disasters caused by explosions or fires. As industries evolve and technology advances, maintaining compliance with safety regulations remains a top priority.
Key Concepts To Know
To navigate the world of intrinsically safe equipment effectively, it’s vital to grasp key concepts such as how to identify intrinsically safe equipment through visual indicators and manufacturer certifications, as well as understanding the difference between Ex IB and Ex IA classifications. Moreover, knowing what are the requirements for intrinsically safe equipment helps organizations select appropriate tools tailored for their specific needs—especially when considering applications like intrinsically safe equipment on ships where maritime safety is critical. As we dive deeper into this topic throughout this outline, you'll gain insights into real-world applications and effective scenarios for using these life-saving technologies.
What is Intrinsically Safe Equipment?
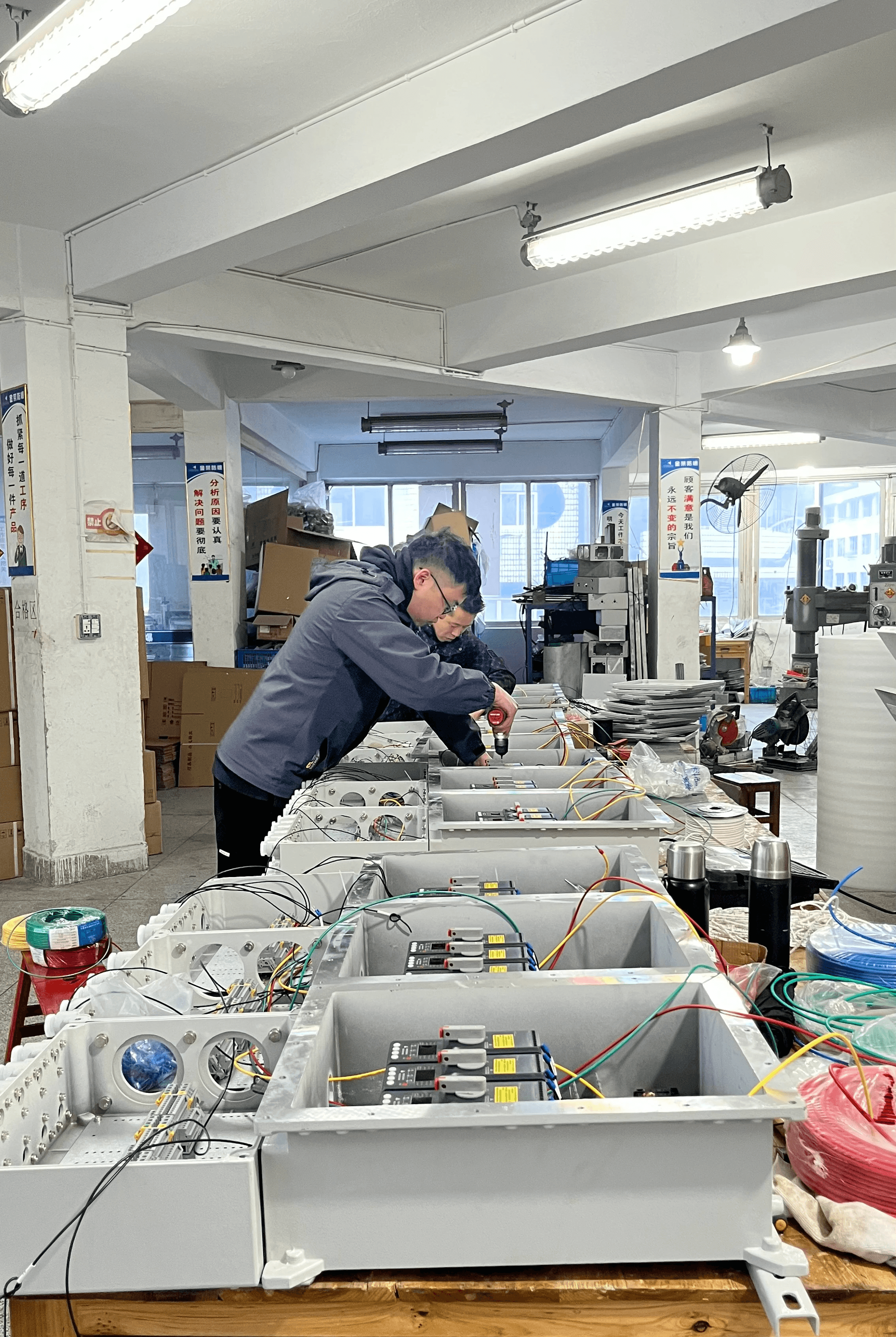
Defining Intrinsic Safety
Intrinsic safety is a protection technique that ensures electrical devices can function safely in potentially explosive atmospheres. It limits the energy available for ignition, meaning that even if a fault occurs, the device won't produce enough heat or spark to ignite a combustible substance. This makes intrinsic safety an essential consideration in industries like oil and gas, chemicals, and mining.
Examples of Intrinsically Safe Equipment
There are numerous examples of intrinsically safe equipment used across various industries. Common devices include handheld communication tools, sensors, and measurement instruments designed specifically for hazardous environments. Other examples also extend to certain types of cameras and lighting systems that ensure safety without compromising performance.
Intrinsically Safe Electrical Equipment Explained
Intrinsically safe electrical equipment operates under strict guidelines to prevent ignition sources from interacting with flammable gases or dusts. These devices are rigorously tested and certified according to international standards before they can be deemed suitable for use in hazardous locations. Understanding how these devices work helps users recognize the importance of selecting appropriate equipment — especially when contrasting them with non-intrinsically safe equipment examples that could pose serious risks.
What is an Example of Intrinsically Safe?
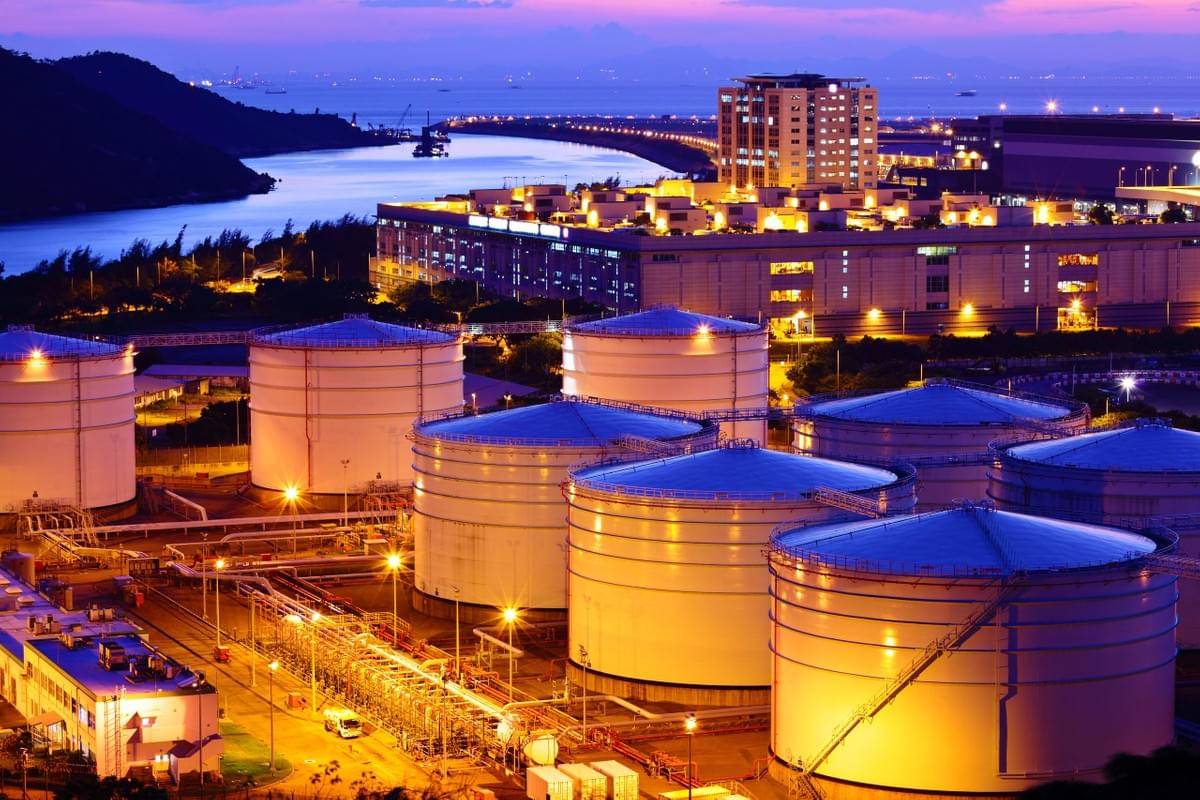
When discussing intrinsically safe equipment, it's crucial to highlight real-world applications that showcase its effectiveness. This type of equipment is designed to operate safely in hazardous environments, where the risk of explosion or fire is present due to flammable gases, vapors, or dust. Understanding what constitutes an example of intrinsically safe equipment helps clarify its importance across various industries.
Real-World Applications
Intrinsically safe equipment finds its place in numerous sectors, including oil and gas, chemical manufacturing, and pharmaceuticals. For instance, handheld devices like smartphones used for data collection in explosive atmospheres are often designed with intrinsic safety in mind. These applications demonstrate how intrinsically safe electrical equipment can mitigate risks while ensuring operational efficiency.
In the maritime industry, intrinsically safe equipment on ships plays a vital role in maintaining safety standards during operations at sea. Equipment such as communication devices and sensors must adhere to strict regulations to prevent ignition sources from causing catastrophic events. The versatility of intrinsically safe designs allows them to be employed effectively across diverse settings where non-intrinsically safe equipment examples would pose significant hazards.
Case Studies of Use
One notable case study involves a major oil refinery that implemented intrinsically safe equipment for monitoring gas levels in their processing units. By replacing traditional sensors with intrinsically safe alternatives, they significantly reduced the risk of explosions caused by flammable gases escaping into the atmosphere. This successful transition not only enhanced safety but also improved efficiency by providing real-time data without compromising worker safety.
Another compelling example comes from a pharmaceutical company that adopted intrinsically safe electrical equipment for use in their production lines involving volatile chemicals. By integrating these systems into their processes, they ensured compliance with stringent industry regulations while safeguarding employees’ health and well-being. Such case studies illustrate how intrinsic safety can be effectively leveraged across different industries.
Effective Scenarios for Use
Effective scenarios for using intrinsically safe equipment include environments where flammable materials are handled or stored—such as fuel depots or chemical plants—where even a spark could lead to disaster. In these situations, employing devices certified as intrinsically safe ensures that any potential energy released will not ignite surrounding materials. Moreover, understanding what are the requirements for intrinsically safe equipment helps organizations make informed decisions when selecting tools and technologies suitable for hazardous locations.
Another scenario involves fieldwork conducted by technicians who need reliable communication tools while working near explosive areas; here, smartphones with intrinsic safety features come into play again as indispensable assets on-site. Similarly, maintenance personnel aboard ships frequently rely on such technology when inspecting storage tanks containing volatile substances—a prime example of why knowing how to identify intrinsically safe equipment is critical in maritime operations.
How to Identify Intrinsically Safe Equipment?
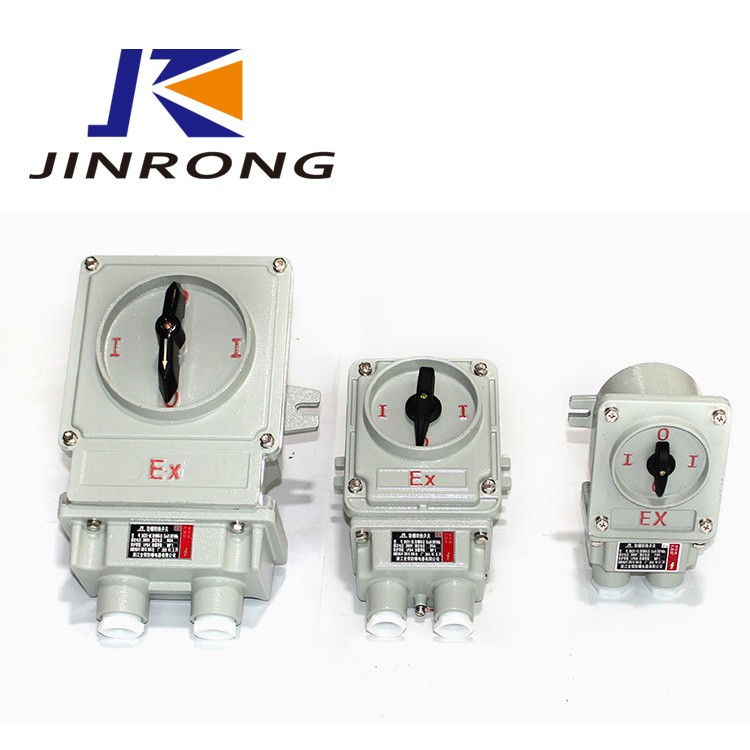
Identifying intrinsically safe equipment is crucial for ensuring safety in hazardous environments. With the right knowledge, one can easily distinguish between intrinsically safe and non-intrinsically safe equipment examples. This section will guide you through visual indicators, manufacturer certifications, and the importance of specifications to help you make informed decisions.
Visual Indicators and Markings
One of the first steps in identifying intrinsically safe equipment is to look for specific visual indicators and markings. These markings often include a symbol or label that indicates compliance with intrinsic safety standards, such as the Ex designation followed by specific classification codes. Familiarizing yourself with these symbols can save you from using non-intrinsically safe equipment examples that could lead to dangerous situations.
Additionally, many manufacturers use color coding or unique designs on their intrinsically safe electrical equipment to make identification easier. For instance, devices may feature labels indicating their suitability for use in explosive atmospheres or hazardous locations. Always take a close look at these visual cues; they are your first line of defense in spotting whether an item meets the requirements for intrinsically safe equipment.
Manufacturer Certifications
Manufacturer certifications play a vital role in verifying that a piece of equipment is indeed intrinsically safe. Reputable manufacturers will typically provide documentation proving that their products have undergone rigorous testing and comply with established safety standards. This certification process ensures that the product has been evaluated against criteria such as temperature limits, energy levels, and potential ignition sources—essential factors when determining what is an example of intrinsically safe.
When assessing manufacturer certifications, it's essential to check for recognized bodies such as ATEX or IECEx approvals, which signify adherence to international safety regulations. These certifications not only offer peace of mind but also serve as a guide when selecting the right equipment for your specific application—whether it’s on land or aboard ships where safety is paramount due to environmental conditions.
Importance of Specifications
Understanding specifications is crucial when identifying intrinsically safe equipment because they detail how a device operates safely under various conditions. Specifications outline critical parameters like voltage ratings, current limits, and temperature classifications—all key components that determine whether an item qualifies as intrinsically safe or falls into the category of non-intrinsically safe equipment examples.
Moreover, adhering strictly to these specifications ensures compliance with industry guidelines and regulations governing both land-based operations and maritime applications where intrinsic safety is vital—especially considering what is the difference between Ex IB and Ex IA classifications? By thoroughly reviewing specifications before making an investment in any piece of electrical gear—or even during routine inspections—you can significantly reduce risks associated with hazardous environments.
What are the Requirements for Intrinsically Safe Equipment?
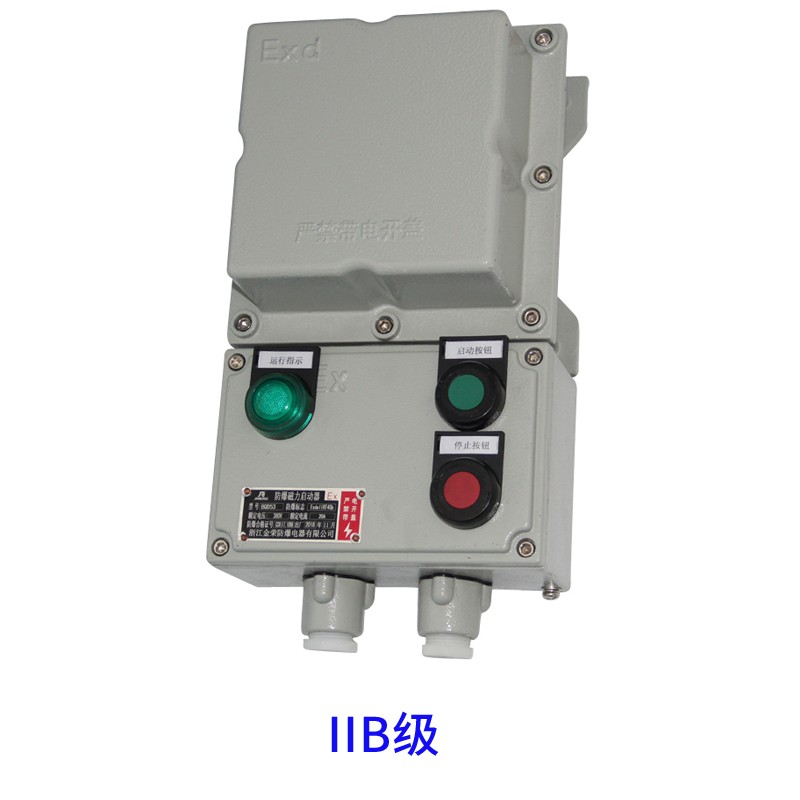
Technical Standards and Regulations
The backbone of intrinsically safe equipment lies in its technical standards and regulations. Various international standards such as IEC 60079-11 outline the criteria that must be met for equipment to be classified as intrinsically safe. Compliance with these standards ensures that the equipment can operate safely in potentially explosive environments without causing ignition, distinguishing it from non-intrinsically safe equipment examples.
Testing and Certification Processes
Testing and certification processes play a pivotal role in validating whether an item qualifies as intrinsically safe electrical equipment. Manufacturers must subject their products to rigorous testing by accredited laboratories, which assess factors like energy levels and temperature rise under fault conditions. Upon successful testing, products receive certification marking them as compliant with safety regulations—an essential step for anyone looking to identify intrinsically safe equipment.
Compliance with Industry Guidelines
Compliance with industry guidelines is not just a formality; it's a necessity when dealing with intrinsically safe equipment. Various sectors have established specific guidelines that dictate how such equipment should be used, maintained, and inspected regularly to ensure ongoing safety performance. Understanding these guidelines helps organizations avoid pitfalls associated with improper usage while also reinforcing the importance of choosing between options like Ex IB and Ex IA classifications when selecting appropriate gear.
What is the Difference Between Ex IB and Ex IA?
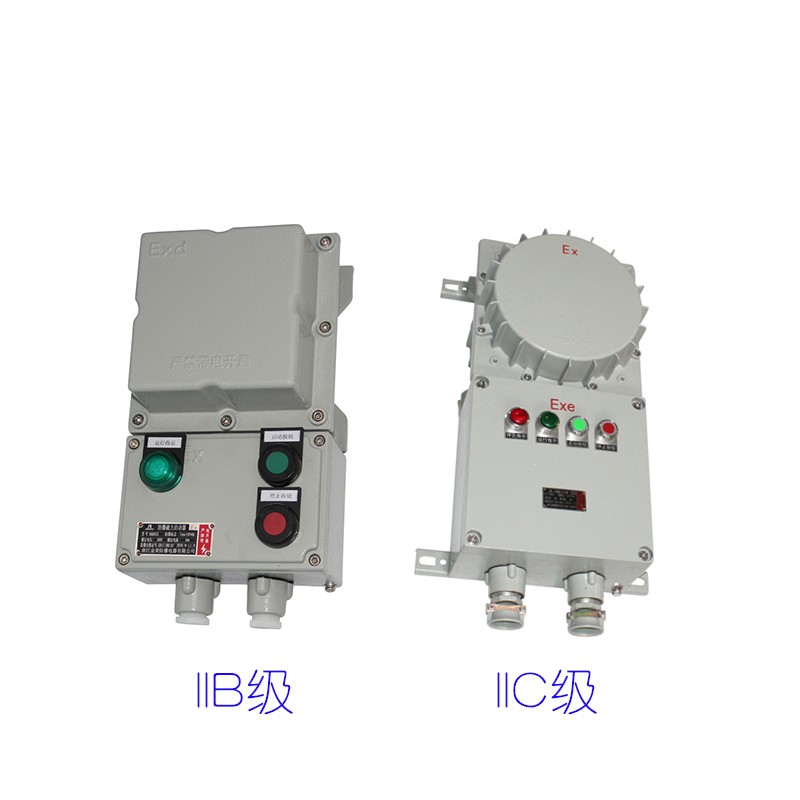
When it comes to intrinsically safe equipment, understanding the classifications of Ex IB and Ex IA is crucial for safety in hazardous environments. These classifications indicate different levels of safety measures designed to prevent ignition in explosive atmospheres. Knowing the differences can help you make informed decisions about what equipment to use in specific situations.
Definitions of Ex IB and Ex IA
Ex IA refers to equipment that is designed for use in areas where there is a high risk of explosive atmospheres occurring continuously or for long periods. This classification ensures that the intrinsically safe electrical equipment can operate safely under those conditions without causing any ignition risks. On the other hand, Ex IB equipment is intended for areas where explosive atmospheres are likely but not constant, providing a slightly less stringent level of safety compared to Ex IA.
Safety Implications of Each Classification
The safety implications of choosing between Ex IB and Ex IA are significant, especially in industries like oil and gas or maritime operations where hazards are prevalent. Using Ex IA equipment means you can have peace of mind knowing it’s designed for continuous exposure to dangerous conditions, while opting for non-intrinsically safe equipment examples could lead to catastrophic failures if exposed to such environments. In contrast, while Ex IB offers protection against occasional hazards, relying solely on this classification may not be adequate in high-risk zones.
Choosing the Right Equipment
Choosing the right intrinsically safe equipment depends on understanding your environment's specific risks and requirements. If you frequently work in areas prone to continuous explosive atmospheres, investing in Ex IA classified gear will be essential for ensuring maximum safety compliance. However, if your operations involve sporadic exposure to hazardous conditions, selecting reliable but less stringent options like those classified as Ex IB may suffice—just remember that thorough identification methods are crucial when determining what type suits your needs best.
Intrinsically Safe Equipment on Ship
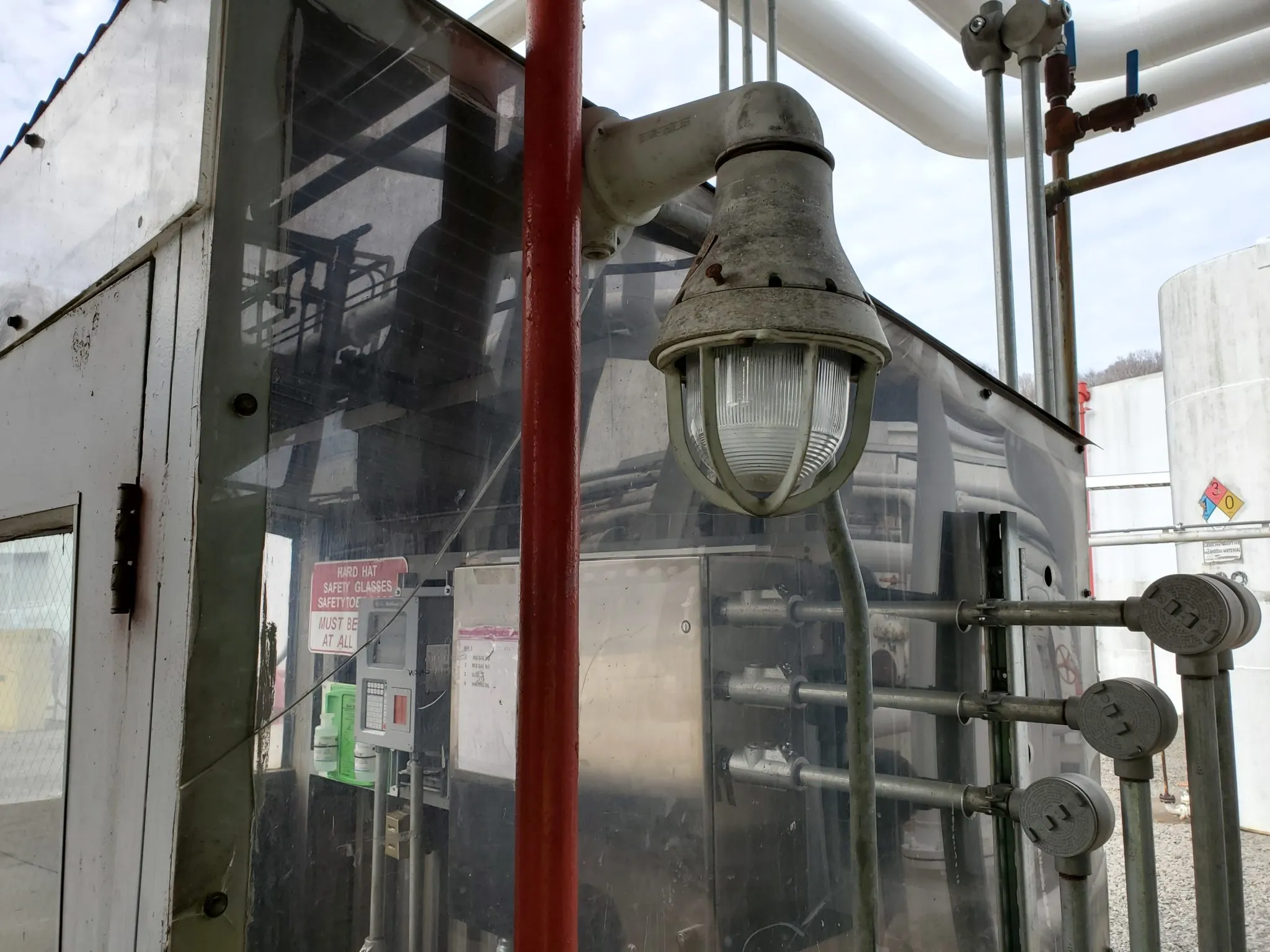
Navigating the unpredictable waters of maritime operations requires a keen focus on safety, especially when it comes to using intrinsically safe equipment. In environments where flammable gases or vapors are present, the use of non intrinsically safe equipment examples can lead to catastrophic consequences. Therefore, understanding how to identify intrinsically safe equipment becomes paramount for crew and operational integrity.
Importance in Maritime Safety
The importance of intrinsically safe equipment in maritime safety cannot be overstated. Ships often operate in hazardous environments where explosive atmospheres may arise from fuel vapors or other volatile substances. By utilizing intrinsically safe electrical equipment, ship operators can ensure that their devices do not ignite these potentially explosive atmospheres, thus preserving both life and property.
In addition to protecting human lives, the use of intrinsically safe equipment also safeguards valuable assets onboard ships. A single ignition event could lead to significant financial losses and endanger entire crews and vessels. This makes compliance with safety standards not just a legal obligation but a moral imperative for all maritime operators.
Common Types Used at Sea
Several types of intrinsically safe equipment are commonly used at sea to enhance safety measures aboard ships. For instance, handheld communication devices designed with intrinsic safety features allow crew members to stay connected without risking ignition from sparks or heat generation. Additionally, sensors and monitoring systems that detect gas leaks utilize intrinsic safety principles to provide real-time data without compromising safety.
Another example includes lighting systems specifically designed for hazardous areas on ships; these lights are engineered not only for visibility but also for maintaining an explosion-proof environment. Furthermore, personal protective equipment (PPE) integrated with intrinsic safety ensures that crew members remain protected while performing their duties in potentially dangerous situations.
Regulations Governing Marine Applications
Regulations governing the use of intrinsically safe equipment on ships are stringent and essential for ensuring maritime safety. Various international standards dictate the design and testing requirements for such equipment, emphasizing compliance with technical standards relevant to marine applications. Organizations like the International Maritime Organization (IMO) set guidelines that help define what is considered an example of intrinsically safe technology in maritime settings.
Moreover, manufacturers must adhere to specific certification processes that validate their products as compliant with industry guidelines regarding intrinsic safety features—this is where understanding what the requirements for intrinsically safe equipment become crucial for ship operators looking to maintain compliance and ensure crew welfare. Regular inspections and audits further reinforce adherence to these regulations, ensuring that all onboard systems function safely under various conditions.
Conclusion
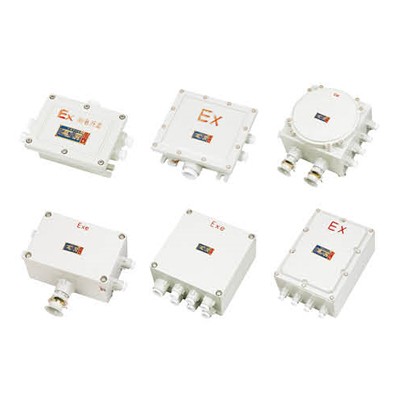
In the ever-evolving landscape of hazardous environments, ensuring safety is paramount. Intrinsically safe equipment plays a crucial role in mitigating risks associated with explosive atmospheres. By adhering to rigorous standards and understanding how to identify intrinsically safe equipment, industries can protect their workers and assets effectively.
Ensuring Safety in Hazardous Environments
The use of intrinsically safe electrical equipment is vital in environments where flammable gases or dust may be present. Understanding what are the requirements for intrinsically safe equipment helps organizations comply with safety regulations while minimizing potential hazards. As we’ve seen, proper identification of this specialized gear can mean the difference between safety and disaster.
The Role of Jinrong in Safety Innovation
Jinrong has established itself as a leader in developing cutting-edge intrinsically safe equipment tailored for various industries, including maritime applications where risks are heightened. Their commitment to innovation ensures that users have access to state-of-the-art solutions that meet stringent safety standards, including distinctions like what is the difference between Ex IB and Ex IA? By continually pushing the envelope, Jinrong contributes significantly to enhancing workplace safety across sectors.
Future of Intrinsically Safe Equipment
Looking ahead, the future of intrinsically safe equipment appears promising as technology advances and new materials emerge. We can expect increased integration of smart technologies that will further refine how we identify intrinsically safe equipment and monitor its performance in real-time. As industries adapt to these changes, understanding non-intrinsically safe equipment examples will remain essential for ensuring compliance and safety across all operations.