Introduction
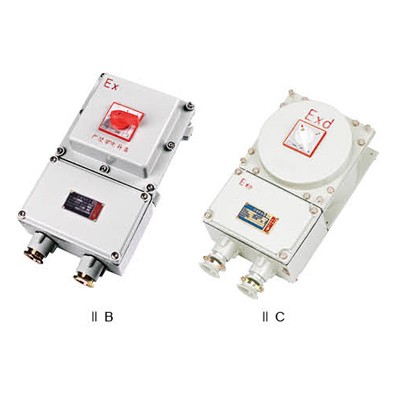
In an age where safety is paramount, understanding the principles of intrinsic safety becomes crucial, especially in environments where hazards lurk around every corner. Intrinsically safe circuits are designed to prevent ignition of flammable materials by limiting the energy available in electrical circuits, thus ensuring that safety remains a top priority. By employing specific electrical wiring techniques and utilizing metal clad cable, these circuits provide a reliable solution for various industries.
Understanding Intrinsic Safety Principles
At its core, intrinsic safety is a design philosophy aimed at safeguarding personnel and equipment from potential explosions or fires in hazardous environments. This approach focuses on controlling the energy levels within electrical wiring systems to ensure they remain below thresholds that could ignite flammable substances. By integrating safety equipment specifically designed for these applications, engineers can create robust systems that prioritize both functionality and protection.
Importance of Intrinsically Safe Circuits
The significance of intrinsically safe circuits cannot be overstated; they serve as the backbone of operational safety in industries such as oil and gas, chemical processing, and mining. These circuits not only protect workers from potential hazards but also minimize the risk of costly accidents and environmental damage. As organizations strive to enhance their safety protocols, investing in intrinsically safe solutions has become an essential component of modern industrial practices.
Overview of Key Safety Features
Intrinsically safe circuits incorporate several key features that contribute to their reliability and effectiveness in hazardous settings. First and foremost, they utilize specialized components designed to limit energy flow—this includes everything from resistors to fuses that ensure no excessive current can cause ignition. Additionally, proper field wiring practices play a vital role alongside cable tray systems for organizing metal clad cable efficiently; together they form a comprehensive approach to maintaining intrinsic safety throughout operations.
What Are Intrinsically Safe Circuits?
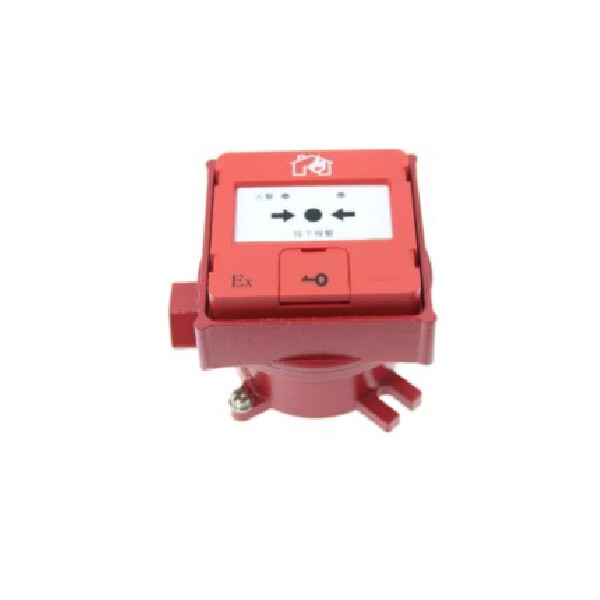
Intrinsically safe circuits are designed to prevent the release of sufficient energy to ignite flammable materials in hazardous environments. This is achieved by limiting the electrical and thermal energy available in the circuit, ensuring that any sparks or heat generated cannot cause an explosion. Understanding these principles is crucial for anyone working in industries where safety is paramount.
Definition and Basic Concepts
At their core, intrinsically safe circuits utilize a combination of safety equipment and design techniques to minimize risks associated with electrical wiring in explosive atmospheres. The basic concept revolves around maintaining low voltage and current levels, which prevents ignition sources from forming. This makes them indispensable for applications where volatile substances are present.
Moreover, intrinsic safety often involves specialized components such as metal clad cables that provide additional protection against environmental factors while ensuring the integrity of electrical connections. These cables are designed to withstand harsh conditions without compromising safety, making them a preferred choice for many industries relying on intrinsically safe circuits. By adhering to strict guidelines and employing well-defined electrical wiring practices, companies can effectively mitigate risks associated with hazardous environments.
Applications in Hazardous Environments
Intrinsically safe circuits find extensive applications in various hazardous environments where flammable gases or dust are present. For instance, they are commonly used in oil refineries where volatile compounds can easily ignite if proper precautions aren't taken. Similarly, chemical processing facilities rely on these circuits to maintain operational safety while handling reactive substances.
In mining operations, intrinsically safe circuits ensure that equipment remains functional without posing a danger to workers or causing accidental explosions due to methane gas accumulation. The versatility of these circuits allows them to be integrated into different systems across various sectors while maintaining a high level of safety standards throughout their operation. This adaptability further emphasizes the importance of understanding intrinsic safety principles when designing systems for hazardous locations.
Common Industries Utilizing Intrinsic Safety
Several industries have adopted intrinsically safe circuit designs as part of their operational protocols due to the inherent risks involved with their processes. The oil and gas sector stands out as one of the primary users; here, ensuring worker safety through reliable electrical wiring solutions is non-negotiable given the explosive nature of hydrocarbons involved.
Chemical manufacturing is another industry heavily reliant on intrinsic safety measures; it involves handling various chemicals that could lead to dangerous situations if not properly managed through effective circuit design and installation practices like using cable trays for organization and protection purposes. Additionally, sectors like pharmaceuticals and food processing also benefit from these advanced safety solutions by reducing potential hazards related to combustible dust or fumes during production processes.
Key Components of Intrinsically Safe Circuits
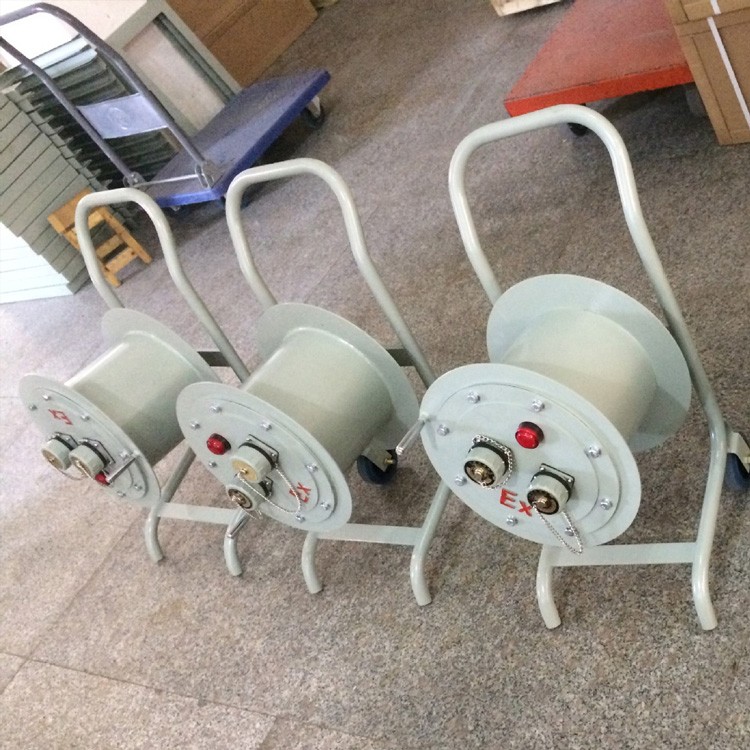
When it comes to intrinsically safe circuits, understanding the key components is crucial for ensuring safety in hazardous environments. These circuits are designed to prevent ignition of flammable materials by limiting the energy available for ignition. The right combination of safety equipment, electrical wiring techniques, and materials like metal clad cable can make all the difference in maintaining a secure and compliant system.
Role of Safety Equipment in Design
Safety equipment plays a pivotal role in the design of intrinsically safe circuits. Devices such as barriers and isolators are essential for containing energy within safe limits, thus protecting against potential hazards. By integrating these safety features into circuit design, engineers can effectively mitigate risks associated with electrical faults or environmental factors that could lead to explosive atmospheres.
Moreover, selecting appropriate safety equipment requires a thorough understanding of both intrinsic safety principles and the specific application environment. Depending on the industry—whether oil and gas or chemical processing—the choice of safety devices can vary significantly to meet compliance standards. Ultimately, investing in high-quality safety equipment not only enhances protection but also ensures adherence to regulations governing intrinsically safe circuits.
Specifics of Electrical Wiring Techniques
Electrical wiring techniques are fundamental when designing intrinsically safe circuits because improper wiring can compromise overall system integrity and safety. Adhering to best practices for field wiring is vital; this includes using appropriate connectors, ensuring proper grounding, and maintaining clear labeling for easy identification during maintenance or troubleshooting. Additionally, employing strategies like minimizing cable lengths can help reduce resistance and enhance reliability.
Another important aspect is ensuring that all wiring is done using suitable materials that meet industry standards for hazardous locations. For instance, using cables specifically designed for intrinsic safety applications helps prevent any accidental discharge that could ignite flammable substances nearby. By focusing on meticulous electrical wiring techniques, engineers can create robust systems that uphold high levels of safety.
Importance of Metal Clad Cable
Metal clad cable is an integral component in the construction of intrinsically safe circuits due to its protective properties against mechanical damage and environmental hazards. This type of cable offers enhanced durability compared to traditional insulation methods, making it ideal for use in harsh industrial settings where exposure to chemicals or physical impact may occur frequently. The rugged nature of metal clad cable allows it to maintain integrity even under extreme conditions.
Furthermore, metal clad cables provide an added layer of electromagnetic interference (EMI) protection which is crucial when working with sensitive electronic components within intrinsically safe circuits. By shielding conductors from external noise sources, these cables help ensure reliable performance without compromising the circuit's inherent safety features. Therefore, incorporating metal clad cables into circuit designs not only boosts resilience but also reinforces overall operational security in hazardous environments.
Certification and Compliance Standards
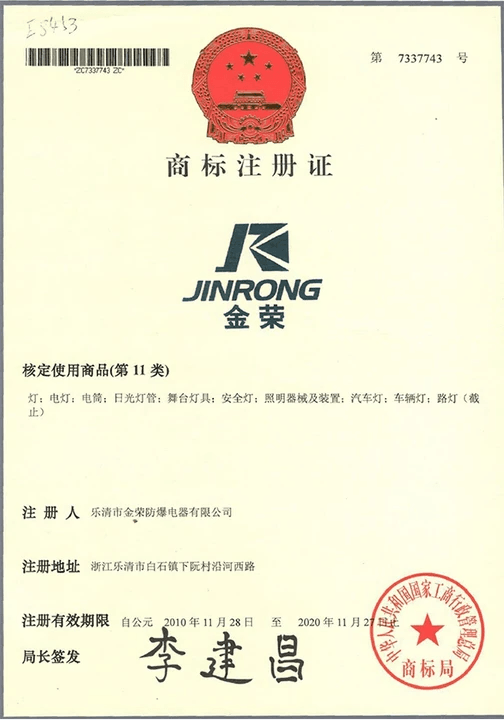
In the realm of intrinsically safe circuits, understanding certification and compliance standards is paramount for ensuring safety in hazardous environments. Regulations such as ATEX and IECEx provide frameworks that govern the design, installation, and maintenance of safety equipment, particularly in industries where explosive atmospheres may be present. Adhering to these standards not only protects personnel but also safeguards valuable assets.
Understanding ATEX and IECEx Regulations
ATEX (Atmosphères Explosibles) is a European directive that outlines essential health and safety requirements for equipment used in explosive atmospheres. Similarly, IECEx (International Electrotechnical Commission System for Certification to Standards Relating to Equipment for Use in Explosive Atmospheres) provides a global certification system to ensure equipment meets stringent safety criteria. Both regulations emphasize the importance of using appropriate electrical wiring techniques and components, including metal clad cable, to minimize risks associated with intrinsically safe circuits.
Compliance with ATEX and IECEx regulations involves rigorous testing and certification processes that evaluate the performance of safety equipment under various conditions. Manufacturers must demonstrate that their products can operate safely without igniting flammable gases or dust. This adherence not only enhances workplace safety but also builds trust among clients who rely on these systems for protection against potential hazards.
Role of Jinrong in Ex-proof Manufacturing
Jinrong has positioned itself as a leader in ex-proof manufacturing by focusing on the development of high-quality intrinsically safe circuits tailored for hazardous environments. The company’s commitment to adhering to ATEX and IECEx standards ensures that its products meet or exceed industry requirements for safety equipment used in explosive atmospheres. By investing in advanced technology and rigorous testing protocols, Jinrong guarantees that its electrical wiring solutions are both reliable and compliant.
The use of metal clad cable within Jinrong's product offerings further enhances the robustness of their intrinsically safe circuits. This type of cable provides superior protection against mechanical damage while maintaining excellent electrical performance under challenging conditions. As industries increasingly prioritize safety, Jinrong’s dedication to innovation positions it as a trusted partner in ex-proof manufacturing.
Moreover, Jinrong actively engages with clients during the design phase to ensure compliance with relevant regulations when upgrading existing systems or implementing new installations. Their expertise helps navigate complex compliance landscapes while delivering effective solutions tailored to specific operational needs.
Navigating Compliance for Safety Upgrades
When it comes time for organizations to upgrade their systems, navigating compliance can feel like traversing a minefield—one wrong step could lead to costly delays or even accidents! However, understanding intrinsic safety principles can ease this process significantly when planning enhancements involving intrinsically safe circuits or field wiring configurations. Engaging knowledgeable professionals who specialize in electrical wiring techniques ensures upgrades align with both ATEX and IECEx standards without compromising operational efficiency.
Utilizing cable tray systems effectively during upgrades plays an essential role in maintaining organized field wiring configurations while adhering strictly to compliance guidelines. Properly designed cable trays not only facilitate easier access but also help protect cables from environmental factors that could pose risks if left unshielded—making them indispensable when working with intrinsically safe circuits!
Lastly, companies should regularly review their existing systems against current regulatory frameworks since updates may arise over time—staying proactive about compliance helps avoid potential pitfalls down the line! Embracing innovative solutions from trusted manufacturers like Jinrong will further enhance your organization’s commitment toward creating safer work environments while remaining compliant with all necessary regulations.
Designing Intrinsically Safe Circuits
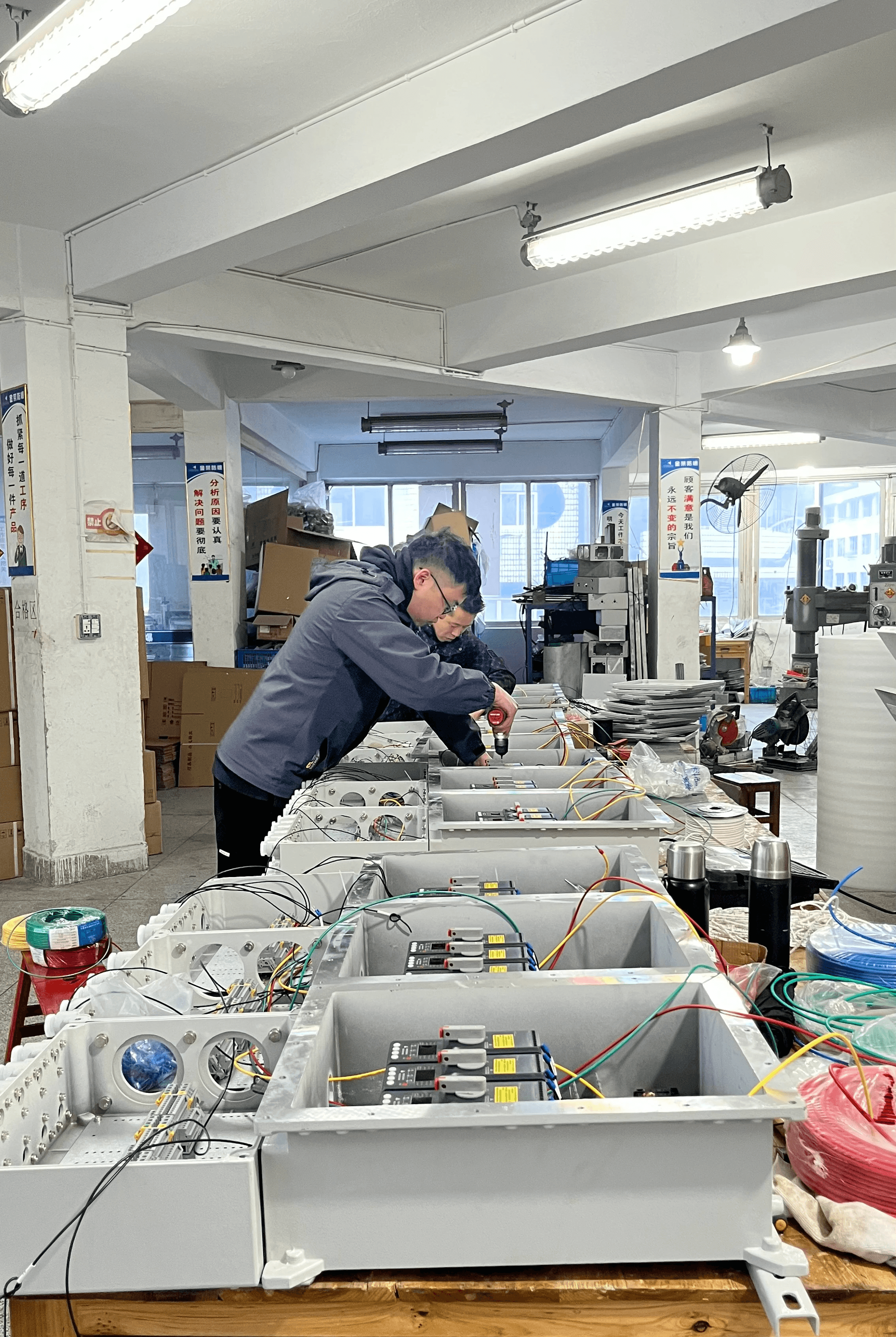
Designing intrinsically safe circuits is a crucial step in ensuring the safety and reliability of electrical systems in hazardous environments. By adhering to best practices, utilizing appropriate safety equipment, and making informed choices about materials and configurations, engineers can create systems that minimize risk while maximizing functionality. This section will delve into effective strategies for field wiring configurations, the use of cable tray systems, and tips for selecting components safely.
Best Practices for Field Wiring Configurations
When configuring field wiring for intrinsically safe circuits, it’s vital to follow best practices to enhance safety and performance. First, ensure that all electrical wiring is meticulously planned to prevent unintentional short circuits or overloads that could compromise intrinsic safety features. Additionally, employing metal clad cable can provide an extra layer of protection against physical damage and environmental hazards while maintaining compliance with safety standards.
Another essential practice involves segregating intrinsically safe circuits from non-intrinsically safe circuits to avoid potential interference. This segregation not only minimizes risks but also simplifies troubleshooting and maintenance activities in the future. Regular inspections should be conducted on the field wiring to identify any wear or damage early on, ensuring ongoing compliance with intrinsic safety regulations.
Using Cable Tray Systems Effectively
Cable tray systems play a pivotal role in organizing electrical wiring for intrinsically safe circuits while promoting both safety and efficiency. These systems facilitate proper airflow around cables, reducing the risk of overheating—an essential consideration when working with sensitive equipment in hazardous environments. Moreover, using cable trays allows for easy access during installation or maintenance without compromising the integrity of the circuit.
Selecting the right type of cable tray is equally important; options like ladder trays or solid-bottom trays can accommodate various types of metal clad cables based on specific project needs. Properly securing cables within these trays not only enhances aesthetics but also ensures that electrical wiring remains intact during routine operations or extreme conditions. Ultimately, an effectively designed cable tray system contributes significantly to maintaining intrinsic safety standards across installations.
Tips for Selecting Components Safely
Choosing components wisely is paramount when designing intrinsically safe circuits; each element must be compatible with intrinsic safety principles to ensure overall system performance and reliability. Start by selecting certified safety equipment that meets relevant industry standards such as ATEX or IECEx—this guarantees that components have been rigorously tested under various conditions specific to hazardous environments.
Additionally, prioritize using high-quality materials such as metal clad cables which provide durability against environmental challenges while safeguarding against accidental sparks or shorts within the circuit itself. Always consult manufacturer specifications regarding component ratings to ensure they align with your design requirements; this attention to detail fosters a culture of proactive safety throughout your project lifecycle.
Real-World Applications and Case Studies
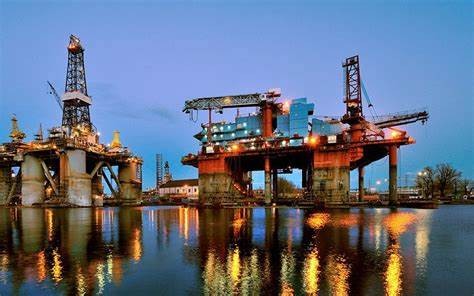
Intrinsically safe circuits play a crucial role in various industries where safety is paramount. By analyzing real-world applications, we can see how these circuits effectively mitigate risks associated with hazardous environments. From oil rigs to chemical plants and mining operations, the importance of intrinsic safety cannot be overstated.
Examples from the Oil and Gas Industry
In the oil and gas industry, intrinsically safe circuits are indispensable for maintaining safety standards while maximizing operational efficiency. These circuits are designed to prevent ignition sources in environments where flammable gases or vapors may be present. Utilizing robust electrical wiring techniques along with metal clad cable ensures that equipment remains protected from external hazards, thereby enhancing overall safety.
One notable example is the implementation of intrinsically safe sensors on offshore drilling platforms. These sensors monitor pressure and temperature, sending data back to control rooms without posing a risk of explosion or fire. By employing field wiring strategies that prioritize safety equipment integration, companies can ensure compliance with stringent regulations while safeguarding their personnel and assets.
Use Cases in Chemical Processing Facilities
Chemical processing facilities are another domain where intrinsically safe circuits shine bright—quite literally! In these settings, hazardous materials often coexist with complex machinery, making it essential to design systems that minimize risk. Intrinsically safe circuits enable operators to use electrical devices safely in zones classified as hazardous due to the presence of flammable chemicals.
For instance, many facilities utilize intrinsically safe handheld devices for monitoring chemical reactions remotely. These devices rely on specialized cable tray systems for organized field wiring that keeps cables secure and minimizes potential damage from spills or leaks. This approach not only enhances operational efficiency but also underscores the commitment to maintaining a safe working environment through innovative intrinsic safety solutions.
Intrinsically Safe Circuits in Mining Operations
Here, intrinsically safe circuits serve as a vital component in protecting both personnel and equipment from catastrophic incidents. By integrating advanced safety equipment into their designs, mining companies can navigate these treacherous conditions more effectively.
A prime example involves using intrinsically safe communication devices among miners working underground—these gadgets facilitate real-time communication without introducing ignition risks associated with traditional electrical systems. Additionally, employing metal clad cable helps shield sensitive components from mechanical damage often encountered during mining activities. As a result, organizations can rely on effective field wiring configurations that prioritize both functionality and safety.
Conclusion
In wrapping up our exploration of intrinsically safe circuits, it is clear that these systems are not just a regulatory requirement but a fundamental aspect of enhancing safety in hazardous environments. As industries continue to evolve, the importance of robust safety measures will only grow, making intrinsic safety technology more relevant than ever. With innovations on the horizon, we can expect advancements that will further improve the reliability and functionality of these critical systems.
The Future of Intrinsic Safety Technology
Looking ahead, the future of intrinsic safety technology is bright and filled with potential. Emerging technologies such as smart sensors and IoT integration are set to revolutionize how intrinsically safe circuits operate, allowing for real-time monitoring and maintenance alerts that enhance overall safety. Additionally, advancements in materials used for electrical wiring and metal clad cable promise to make these systems even more resilient against environmental challenges.
Enhancing Safety with Innovative Solutions
To truly enhance safety in hazardous environments, innovative solutions must be embraced across all sectors utilizing intrinsically safe circuits. This includes adopting advanced safety equipment designed specifically for these applications, which can significantly reduce risks associated with electrical hazards. Moreover, optimizing field wiring techniques and utilizing effective cable tray systems can streamline installations while ensuring compliance with stringent safety standards.
Why Choose Jinrong for Your Safety Needs
Our commitment to quality ensures that every component—be it metal clad cable or specialized electrical wiring—is designed with utmost care for maximum reliability and performance in hazardous settings. By choosing Jinrong, you’re not just investing in products; you’re investing in peace of mind knowing that your operations prioritize both efficiency and uncompromising safety.