Introduction
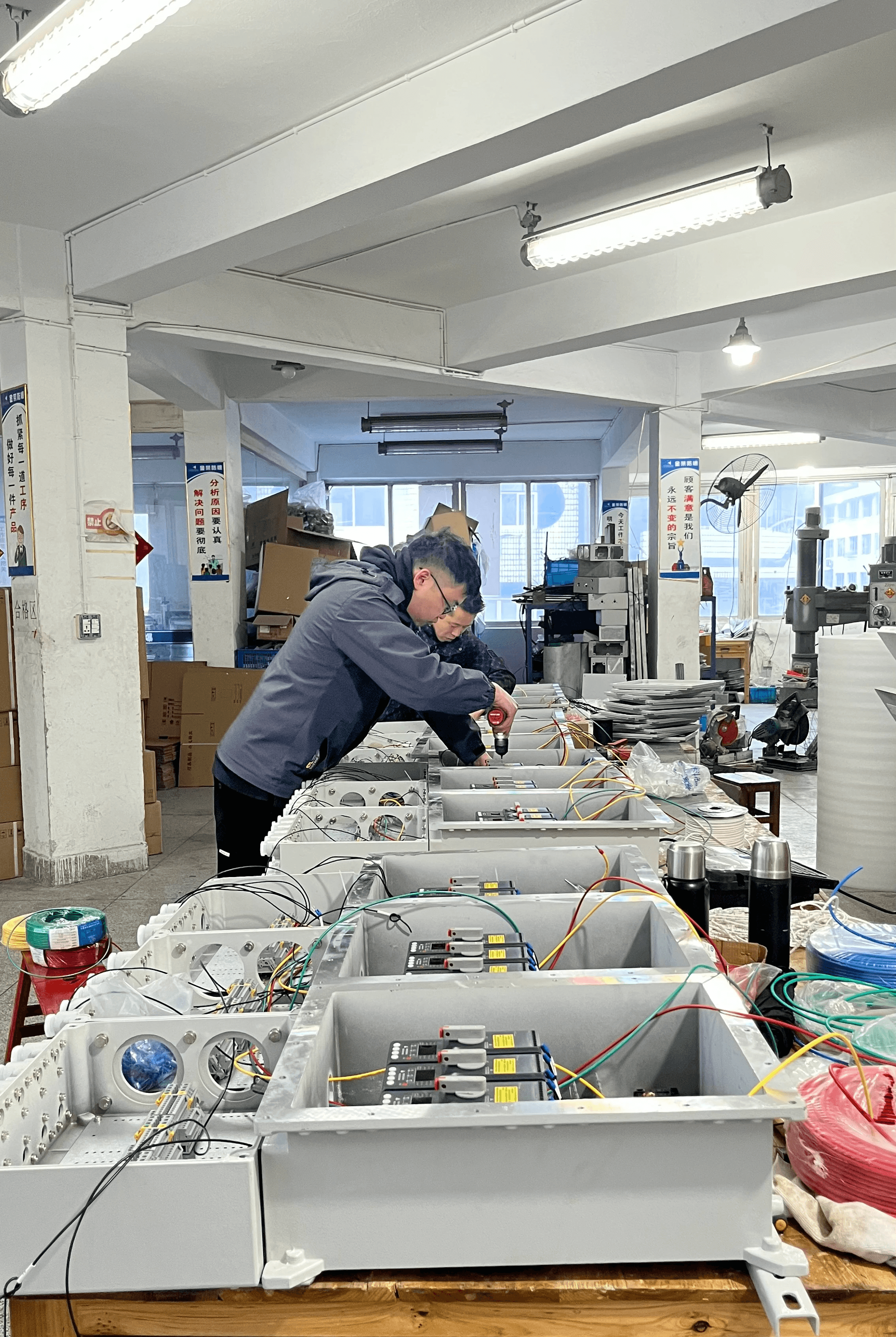
In industries where flammable gases, vapors, or dust are present, safety is not just a priority; it's a necessity. Understanding intrinsically safe equipment is crucial for ensuring that operations run smoothly without posing risks to personnel or the environment. But what is the difference between intrinsically safe and non-intrinsically safe equipment? This distinction can mean the difference between safe operations and catastrophic incidents.
Understanding Intrinsically Safe Equipment
Intrinsic safety refers to a protection technique for electrical equipment used in hazardous areas. It ensures that any potential energy released from the device is below levels that could ignite a combustible atmosphere. So, what is meant by intrinsically safe? Essentially, it's about designing devices that prevent ignition sources while maintaining functionality in challenging environments.
Importance of Safety in Hazardous Areas
Safety in hazardous areas cannot be overstated; one spark can lead to disaster. This makes understanding non intrinsically safe (NIS) equipment critical for anyone working in these settings. The risks associated with using NIS devices are significant, which leads us to ask: What is the difference between NIS and IS? By recognizing these differences, companies can make informed choices about their equipment.
Overview of Non Intrinsically Safe Equipment
Non intrinsically safe equipment includes devices that do not have protective features designed to prevent ignition in hazardous environments. Examples of non intrinsically safe equipment often include standard electrical tools and machinery that may pose risks when used improperly or without adequate safeguards. Additionally, non intrinsically safe cable can exacerbate dangers by failing to provide necessary protections against ignition sources in volatile atmospheres.
What Is Intrinsically Safe?
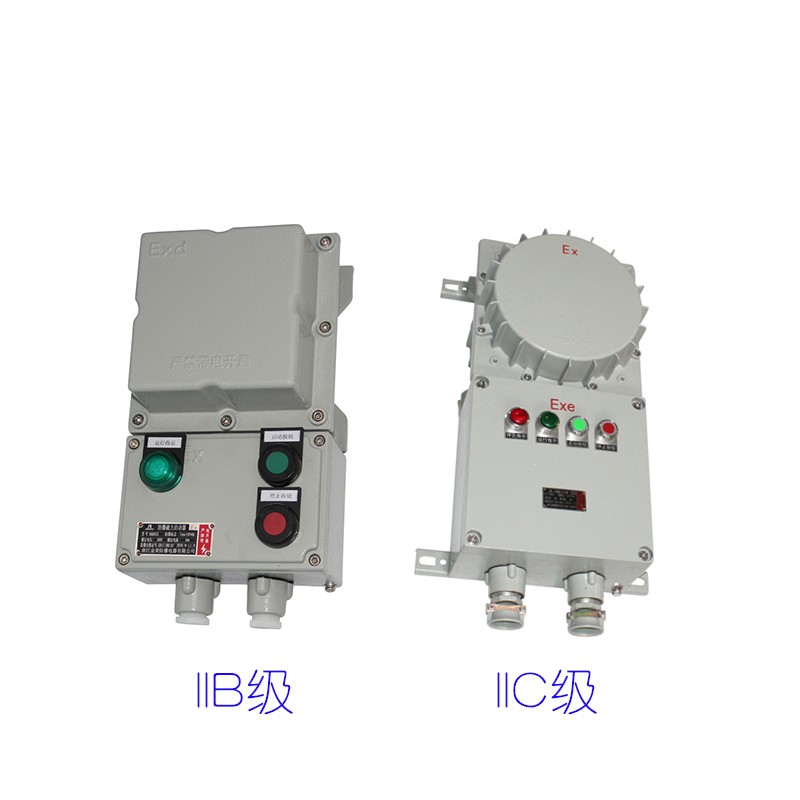
When it comes to equipment used in potentially hazardous environments, the term intrinsically safe is crucial. But what is meant by intrinsically safe? This concept refers to a design philosophy aimed at preventing ignition of flammable materials by limiting energy, ensuring that even in the event of a fault, devices will not produce sparks or excessive heat. Intrinsically safe equipment is essential for industries such as oil and gas, chemical manufacturing, and mining where the risk of explosion is ever-present.
Definition and Key Features
Intrinsically safe (IS) devices are engineered to operate safely in explosive atmospheres by design. The key features include low power consumption, limited voltage, and current levels that reduce the risk of ignition. In contrast to non intrinsically safe (NIS) equipment, these devices are rigorously tested to ensure they meet strict safety standards before being deployed in hazardous areas.
Understanding what is the difference between intrinsically safe and non-intrinsically safe can be illuminating. While IS devices are designed with safety as their primary concern, NIS equipment lacks these stringent safeguards and can pose significant risks if used incorrectly in dangerous environments. An example of intrinsically safe equipment might include specialized handheld communication devices or sensors used on oil rigs that are certified for use in explosive atmospheres.
The Science Behind Intrinsic Safety
The science behind intrinsic safety involves a combination of electrical engineering principles and rigorous testing protocols. Essentially, IS designs ensure that any potential energy release—whether it be electrical sparks or thermal energy—is kept below levels that could ignite flammable gases or dusts present in the environment. This approach often utilizes barriers or isolators that limit energy flow into hazardous areas.
When comparing NIS versus IS technology, one must recognize how critical this scientific foundation is for preventing accidents at work sites where volatile substances are present. Non intrinsically safe cable systems may carry higher voltages and currents without adequate protective measures, making them unsuitable for such applications. Thus understanding this science can help industries make informed choices about which type of equipment best suits their operational needs.
Why Intrinsic Safety Matters
Intrinsic safety matters because it directly correlates with worker safety and environmental protection in hazardous settings. By utilizing intrinsically safe devices, companies significantly reduce the likelihood of accidents caused by explosions or fires—issues that can have devastating consequences both humanely and financially.
Moreover, understanding non intrinsically safe meaning helps organizations recognize the potential dangers associated with using NIS equipment examples; from simple tools to complex machinery that could inadvertently cause catastrophic failures if not properly managed within designated zones. As industries evolve towards more stringent safety regulations worldwide, intrinsic safety will remain a cornerstone principle guiding future innovations in ex-proof manufacturing.
Examples of Intrinsically Safe Equipment
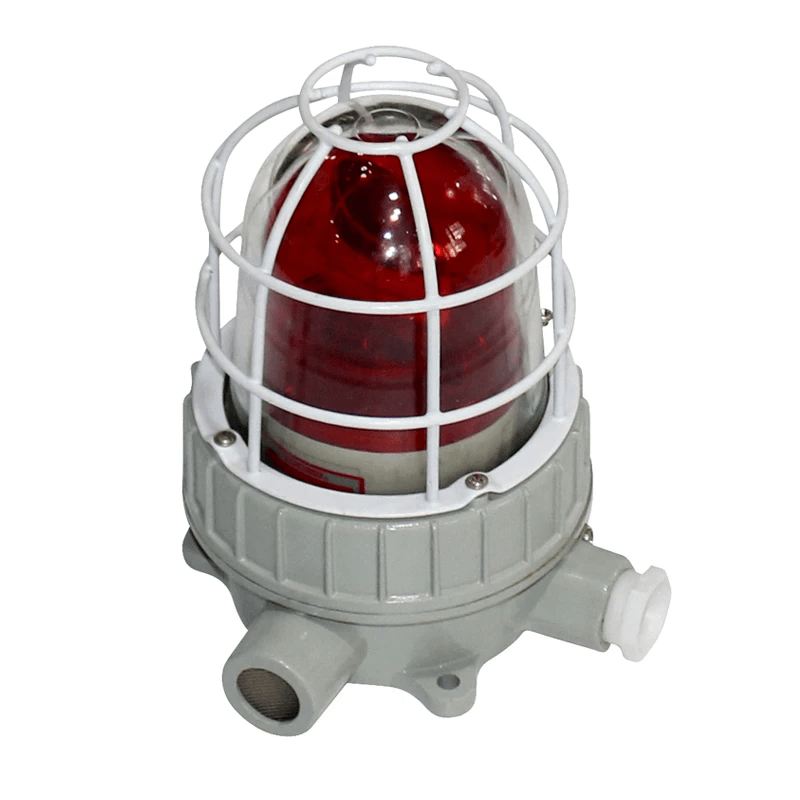
When it comes to ensuring safety in hazardous environments, intrinsically safe equipment plays a pivotal role. This type of equipment is designed to operate safely in explosive atmospheres by limiting the energy available for ignition. Understanding what is meant by intrinsically safe can help distinguish it from non intrinsically safe (NIS) alternatives, which can pose significant risks in similar settings.
Common Applications in Industry
Intrinsically safe devices find their way into various industries where flammable gases, vapors, or dust are present. Common applications include oil and gas exploration, chemical manufacturing, mining operations, and pharmaceuticals. In these sectors, the question often arises: what is the difference between intrinsically safe and non-intrinsically safe? The key lies in the design and functionality that prevent potential ignition sources from causing catastrophic incidents.
Leading Brands and Their Offerings
Several leading brands have made their mark by providing high-quality intrinsically safe equipment tailored for hazardous environments. Companies like Honeywell, Siemens, and Pepperl+Fuchs offer a range of products that meet stringent safety standards. These brands understand the critical nature of their offerings; thus, they ensure that their devices are not only compliant but also reliable when compared to non intrinsically safe alternatives.
Jinrong's Role in Ex-Proof Manufacturing
Jinrong has established itself as a key player in ex-proof manufacturing by focusing on producing state-of-the-art intrinsically safe solutions. Their commitment to quality ensures that each product minimizes risks associated with non intrinsically safe equipment examples found on the market today. By leveraging advanced technology and rigorous testing methods, Jinrong exemplifies how innovation can lead to safer operational practices across various industries.
What Is the Difference Between Intrinsically Safe and Non-Intrinsically Safe?
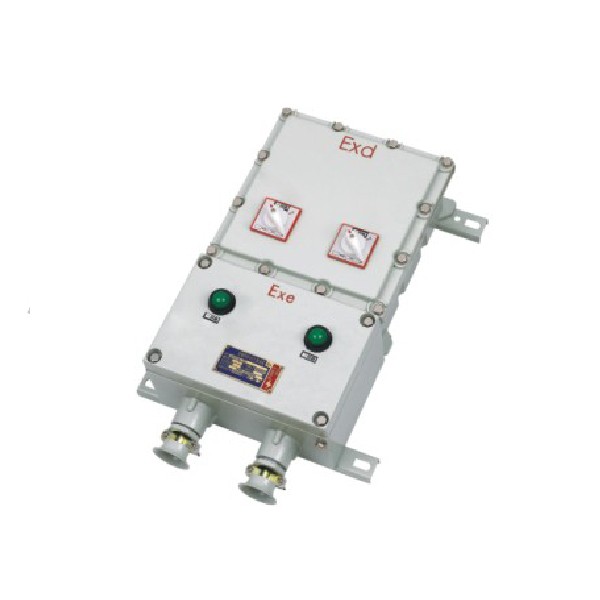
Understanding the difference between intrinsically safe and non-intrinsically safe equipment is crucial for anyone working in hazardous environments. The fundamental distinction lies in how each type of equipment manages potential ignition sources. This section will explore what is meant by intrinsically safe, delve into the meaning of non-intrinsically safe, and highlight key safety features that set these two categories apart.
Understanding Non Intrinsically Safe Meaning
Non-intrinsically safe (NIS) refers to equipment or devices that do not incorporate safety measures to prevent ignition in explosive atmospheres. Unlike their intrinsically safe counterparts, NIS devices can generate enough energy to ignite flammable gases or dust under certain conditions. This lack of protection makes it essential for industries operating in hazardous areas to understand the implications of using non-intrinsically safe equipment examples, which can lead to catastrophic incidents if not properly managed.
When asking What is the difference between intrinsically safe and non-intrinsically safe?, it's important to recognize that NIS equipment often requires additional protective measures such as barriers or enclosures to mitigate risks. These extra layers may not always be sufficient, especially if maintenance practices are lax or if operators are unaware of the potential dangers associated with their use. Thus, a clear understanding of non-intrinsically safe meaning helps professionals make informed choices about their operational safety.
Key Safety Features of Intrinsically Safe Devices
Intrinsically safe devices are designed with specific safety features that minimize the risk of ignition in hazardous environments. One key characteristic is their ability to limit electrical energy output, ensuring that any spark produced during operation is too weak to ignite flammable materials. Additionally, these devices often include robust design elements such as reinforced casings and specialized circuitry tailored for use in explosive atmospheres.
When considering What is an example of intrinsically safe? one might think of handheld gas detectors or communication devices specifically engineered for use in oil rigs or chemical plants where explosive gases are present. These devices not only meet stringent industry standards but also undergo rigorous testing to ensure they perform safely under various conditions. The emphasis on safety features sets intrinsically safe devices apart from non-intrinsically safe options, making them essential tools for maintaining workplace safety.
Risks Associated with Non-Intrinsically Safe Equipment
Using non-intrinsically safe equipment poses significant risks that can lead to severe consequences in hazardous environments. One major concern is the potential for explosions caused by sparks or heat generated by NIS devices when they come into contact with flammable substances like gas or dust. This risk becomes even more pronounced when considering real-world applications where human error can occur due to a lack of awareness regarding what is meant by intrinsically safe versus non-intrinsically safe.
In addition to explosion hazards, relying on non-intrinsic technology may result in costly downtime and damage control efforts following an incident. Industries utilizing NIS cable must be particularly vigilant since improper installation or maintenance can exacerbate these risks substantially—leading some companies toward adopting alternatives designed specifically for safer operations instead. Understanding these risks emphasizes why choosing intrinsic safety over its counterpart should be a priority for any organization operating within potentially dangerous settings.
Non Intrinsically Safe Equipment Examples
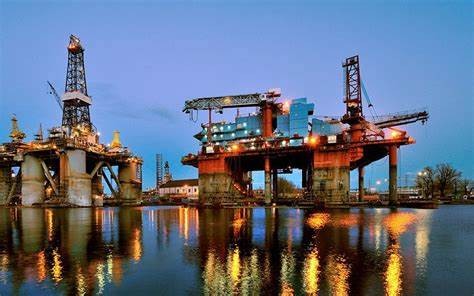
When discussing safety in hazardous environments, it’s crucial to understand the implications of using non intrinsically safe (NIS) equipment. Various industries rely on NIS equipment for specific functions, but this reliance can pose significant risks when not managed properly. From oil and gas to pharmaceuticals, these sectors often grapple with the question: what is the difference between intrinsically safe and non-intrinsically safe?
Common Industries Using NIS Equipment
Several industries frequently utilize non intrinsically safe equipment, often due to its cost-effectiveness or availability. The oil and gas sector is a prime example, where NIS devices are common for drilling operations and monitoring systems. Additionally, manufacturing facilities may use non intrinsically safe cable in their processes, despite the inherent risks associated with such choices.
In the chemical industry, NIS equipment might be employed for tasks that don't directly involve hazardous materials but still operate in environments where flammable substances are present. The construction industry also sees a reliance on NIS tools and machinery that may not meet intrinsic safety standards but are deemed necessary for specific tasks. It’s essential to weigh the benefits against potential hazards when choosing between these two types of equipment.
Real-World Applications and Case Studies
Real-world applications of non intrinsically safe equipment highlight both its utility and its dangers. For instance, in a petrochemical plant, workers might use NIS sensors for routine monitoring; however, if a spark occurs near flammable vapors due to an electrical fault, it could lead to catastrophic results. Case studies have shown that incidents involving non intrinsically safe devices often result in explosions or fires that could have been avoided with proper intrinsic safety measures.
Another example can be found within manufacturing plants using non intrinsically safe cable for communication systems across hazardous areas. A breakdown or malfunction here can compromise safety protocols and endanger lives if not addressed promptly. These scenarios underscore why understanding what is meant by intrinsically safe versus its non-intrinsically safe counterparts is vital for operational integrity.
The Consequences of Using Non-Intrinsically Safe Equipment
The consequences of deploying non intrinsically safe (NIS) equipment can be dire—and sometimes deadly. When organizations overlook the differences between NIS and IS devices, they expose themselves to risks such as explosions or fires due to electrical faults or overheating components in volatile environments. This oversight not only jeopardizes employee safety but also leads to costly downtimes and potential legal ramifications.
Moreover, relying on non intrinsically safe equipment examples without adequate safeguards can result in severe financial losses from damage control efforts after an incident occurs—an expensive lesson learned too late! Companies must prioritize training their personnel about the importance of recognizing the differences between various types of equipment used in hazardous locations: what is an example of intrinsically safe? It’s time organizations take proactive measures rather than reactive ones when it comes to workplace safety.
Non Intrinsically Safe Cable: A Cautionary Tale
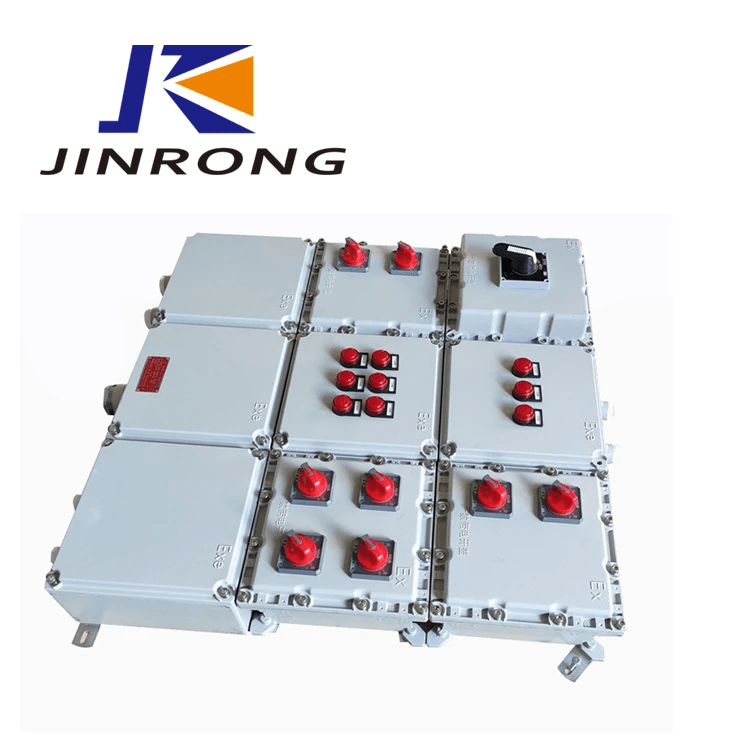
When discussing safety in hazardous environments, non intrinsically safe (NIS) cable often raises alarms. Unlike its intrinsically safe counterparts, NIS cable is designed without the rigorous safety features that prevent ignition sources in explosive atmospheres. This section delves into the characteristics of NIS cable, the risks it poses in hazardous settings, and viable alternatives for safer operations.
Characteristics of NIS Cable
Non intrinsically safe cable is typically constructed with materials that do not inherently protect against sparks or heat generation during normal operation. These cables may lack robust insulation and shielding, making them susceptible to environmental factors like moisture and chemical exposure. Additionally, they often have higher current-carrying capabilities but come with increased risks when used in explosive environments.
Risks in Hazardous Environments
Using non intrinsically safe equipment examples like NIS cables in hazardous areas can lead to catastrophic consequences. The absence of intrinsic safety measures means that any electrical fault could ignite flammable gases or dust present in the environment. Furthermore, since these cables do not meet stringent safety standards, they increase the likelihood of accidents and may result in severe injuries or property damage.
Alternatives for Safer Operations
To mitigate risks associated with non intrinsically safe cable usage, industries should consider switching to intrinsically safe options whenever possible. What is meant by intrinsically safe? It refers to equipment designed to operate safely under normal conditions without producing ignition sources even during faults. By investing in such technology, businesses can ensure compliance with safety regulations while protecting their workforce and assets from potential disasters.
Conclusion
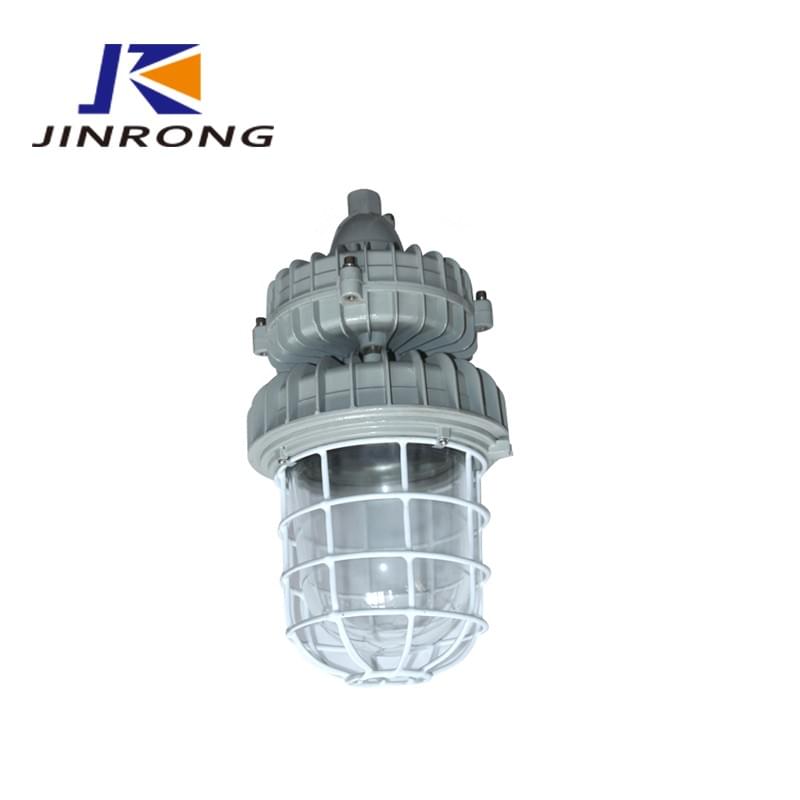
In conclusion, understanding intrinsic safety and its significance in hazardous environments is crucial for ensuring the safety of personnel and equipment. The stark contrast between intrinsically safe and non intrinsically safe (NIS) equipment highlights the importance of selecting the right tools for specific applications. As industries continue to evolve, the need for reliable and safe equipment remains paramount, making intrinsic safety a key consideration.
Key Takeaways on Intrinsic Safety
One of the primary takeaways is that intrinsic safety is all about preventing ignition in explosive atmospheres, which can be achieved through careful design and engineering. What is meant by intrinsically safe? It refers to devices designed to operate safely in hazardous locations by limiting energy levels that could ignite flammable materials. On the flip side, non intrinsically safe equipment examples often pose significant risks, especially in volatile environments where even minor sparks can lead to catastrophic outcomes.
Making Informed Choices for Safety
When evaluating what is the difference between intrinsically safe and non-intrinsically safe systems, it becomes clear that choosing NIS equipment can expose operations to unnecessary dangers. Understanding non intrinsically safe meaning enables professionals to make informed decisions about their operational requirements while prioritizing safety above all else. By opting for intrinsically safe devices whenever possible, companies not only protect their workers but also safeguard their investments against potential liabilities associated with accidents caused by NIS equipment.
The Future of Ex-Proof Equipment with Jinrong
Looking ahead, Jinrong stands at the forefront of innovation in ex-proof manufacturing, focusing on enhancing safety features while maintaining efficiency across various industries. With advancements in technology and a growing emphasis on compliance with international safety standards, Jinrong aims to bridge gaps between traditional practices and modern needs concerning what is an example of intrinsically safe equipment. As we navigate through these developments, it’s essential to recognize that prioritizing intrinsic safety will pave the way for a safer future while reducing reliance on non intrinsically safe solutions.