Introduction
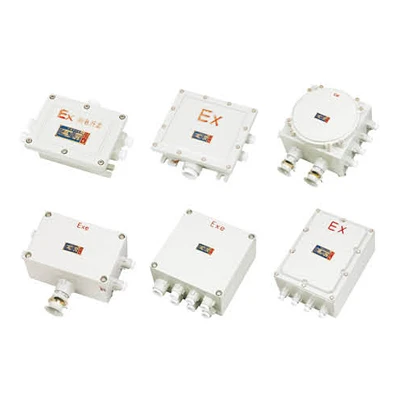
In industries where flammable gases, vapors, or dust are present, ensuring safety is paramount. This is where explosion proof outlets come into play. Understanding what an explosion proof socket is and how it functions can significantly reduce the risks associated with hazardous environments.
Understanding Explosion-Proof Outlets
An explosion proof outlet is designed to contain any potential explosions within the device itself, preventing ignition of surrounding materials. These specialized receptacles are built with robust materials and engineering techniques to withstand extreme conditions. By learning about how do explosion proof outlets work, you can appreciate their critical role in safeguarding personnel and property in dangerous settings.
The Importance of Safety Standards
Safety standards govern the design and use of explosion proof products to ensure they meet stringent requirements for hazardous areas. Adhering to these standards not only protects workers but also minimizes liability for employers by promoting a safer workplace environment. When considering what is the difference between ATEX and explosion proof certifications, it's essential to recognize that compliance with safety regulations can be a game-changer in risk management.
Applications in Hazardous Environments
Explosion proof outlets find their applications across various industries such as oil and gas, chemical manufacturing, mining, and pharmaceuticals. In these sectors, even a minor electrical spark can lead to catastrophic consequences; hence investing in an explosion-proof receptacle box becomes crucial for operational safety. Additionally, understanding what is explosion proof wiring helps ensure that all components work harmoniously together in protecting against potential hazards.
What is an Explosion Proof Socket?
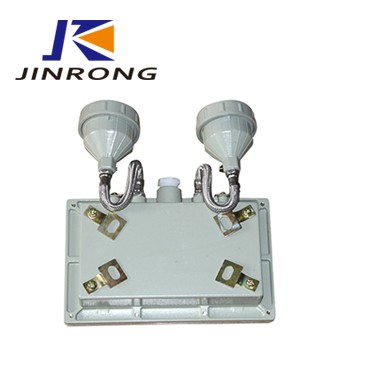
Definition and Purpose
An explosion proof socket, often referred to as an explosion-proof receptacle box, is engineered to contain any explosion that might occur within its housing. The primary purpose of these sockets is to provide a safe connection point for electrical devices in environments where flammable materials are present. By using an explosion proof outlet, businesses can significantly reduce the risk of fire or explosions caused by electrical faults.
Key Features and Specifications
Explosion proof outlets come with several key features that set them apart from standard electrical sockets. They typically include robust sealing mechanisms that prevent the ingress of dust and moisture, along with pressure relief features to manage any internal explosions safely. Additionally, these outlets are often constructed from durable materials resistant to corrosion and impact, ensuring long-lasting performance even in challenging conditions.
Common Materials Used
The materials used in manufacturing explosion proof sockets play a vital role in their effectiveness and longevity. Commonly utilized materials include aluminum, stainless steel, and reinforced plastics—each chosen for their strength and resistance to harsh chemicals or environmental factors. These materials not only enhance the durability of the explosion proof outlet but also contribute to its ability to withstand extreme conditions without compromising safety.
How Do Explosion Proof Outlets Work?
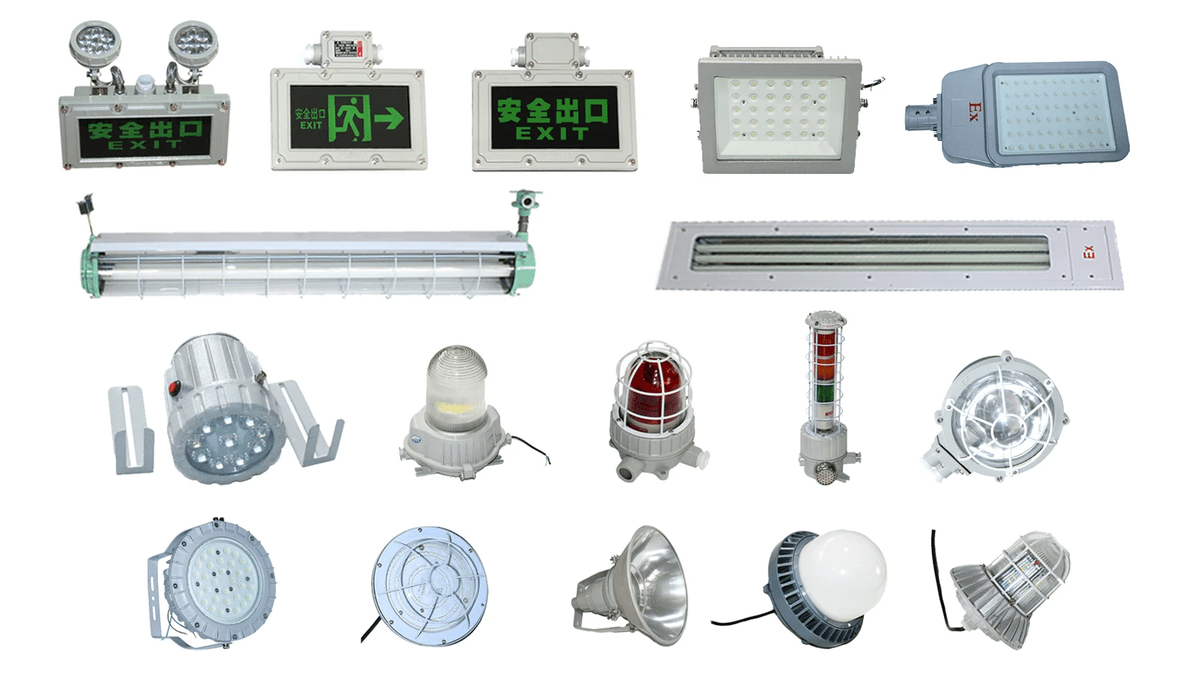
The Mechanism Behind Their Safety
The mechanism behind the safety of an explosion proof outlet lies in its design and construction. Essentially, these sockets are built to withstand internal pressures resulting from an explosion without allowing flames or hot gases to escape into the surrounding environment. This is achieved through careful selection of materials and engineering techniques that create a barrier against ignition sources, making them essential components in hazardous locations.
In addition to their sturdy exterior, what is an explosion proof socket? It’s one that features intrinsic safety measures such as thermal protection and flame arrestors. These features work together to ensure that even if a spark occurs inside the outlet, it won’t lead to a catastrophic event outside of it—keeping everyone safe.
Sealing Techniques Explained
Sealing techniques play a vital role in how do explosion proof outlets work effectively. These sockets employ gaskets and seals made from durable materials like rubber or silicone to create airtight closures around wiring connections and junctions. This prevents any potentially explosive substances from entering the receptacle box and interacting with electrical components.
Moreover, proper sealing not only keeps hazardous materials out but also protects against moisture ingress, which can cause short circuits or corrosion over time. When installing an explosion-proof receptacle box, ensuring that all seals are intact is crucial for maintaining its integrity and effectiveness in preventing explosions.
Pressure Relief Features
Pressure relief features are another key aspect of how explosion proof outlets function safely under pressure conditions. In the event of an internal explosion, these outlets are equipped with mechanisms that allow for controlled venting of gases while preventing the escape of flames or sparks into the surrounding area.
This thoughtful design helps mitigate risks associated with pressure buildup during an incident—essentially acting as a fail-safe system that reduces potential hazards significantly. Whether you’re considering installation or replacement of your existing units, understanding what is explosion proof wiring can further enhance your knowledge about these critical safety devices.
What is the Difference Between ATEX and Explosion Proof?
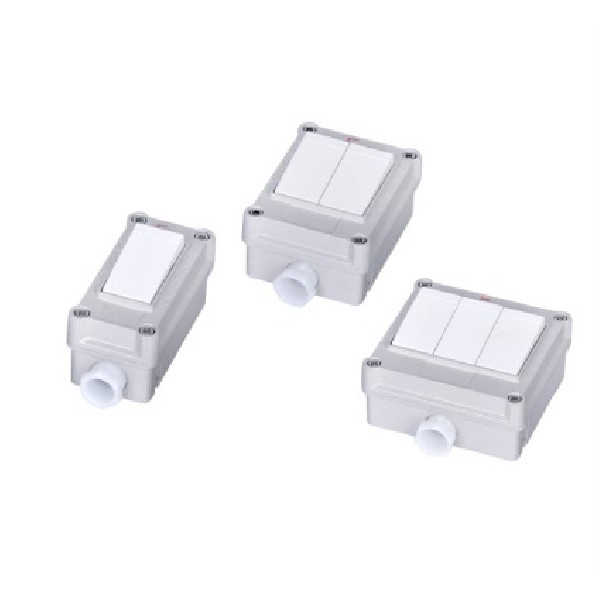
When discussing safety in hazardous environments, two terms often come up: ATEX and explosion proof. While both aim to ensure safety, they cater to different standards and applications. Understanding these differences is crucial for selecting the right equipment, such as an explosion proof outlet or an explosion-proof receptacle box.
Overview of ATEX Standards
ATEX stands for Atmosphères Explosibles, which refers to a set of European Union directives that govern equipment used in explosive atmospheres. These standards ensure that products are designed and manufactured to minimize the risk of ignition in potentially hazardous environments. If you're considering what is an explosion proof socket, knowing about ATEX can help you make informed decisions regarding compliance and safety.
Comparing Certification Requirements
The certification requirements for ATEX products are stringent, focusing on both design and testing processes to ensure reliability under explosive conditions. In contrast, general explosion proof standards may vary significantly by region or industry but generally emphasize robust construction and sealing techniques. When evaluating what is the difference between ATEX and explosion proof options, consider how each certification aligns with your specific needs for installation or replacement of components like an explosion proof outlet.
Choosing the Right Product for Your Needs
Selecting between ATEX-certified equipment and general explosion-proof products depends on your operational environment and regulatory requirements. If you're working within Europe or dealing with specific industries that mandate ATEX compliance, opting for an ATEX-certified product might be essential. Conversely, if you’re focused on general safety without specific regulations dictating your choices, a reliable explosion proof outlet could suffice—just be sure it meets necessary safety standards.
What is Explosion Proof Wiring?
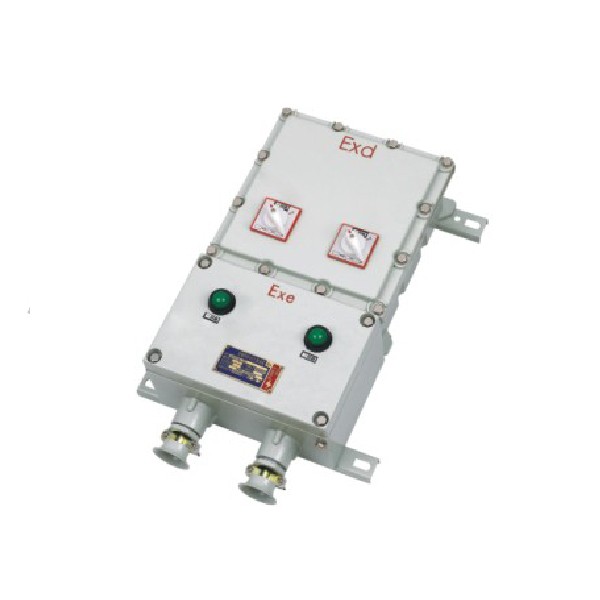
Explosion proof wiring is a critical component in environments where flammable gases, vapors, or dust are present. This specialized wiring system is designed to prevent ignition sources from escaping into potentially hazardous areas, ensuring safety and compliance with industry standards. Understanding what constitutes explosion proof wiring can help you make informed decisions about your electrical installations.
Essential Components of Explosion Proof Wiring
The essential components of explosion proof wiring include specially designed cables, connectors, and junction boxes that can withstand explosive conditions. These cables are often encased in robust materials like steel or thermoplastic to resist mechanical damage and corrosion. Additionally, the connectors and receptacles must be rated for explosion-proof applications to ensure that any sparks or heat produced during operation do not ignite surrounding flammable substances.
When considering what is an explosion proof socket?, it’s important to note that these sockets must complement the wiring by providing secure connections that maintain the integrity of the entire system. The explosion-proof receptacle box serves as a protective enclosure that houses these connections safely away from hazardous materials. Together, these components create a comprehensive system designed for safety in volatile environments.
Installation Guidelines and Best Practices
When it comes to installation guidelines for explosion proof outlet systems, following best practices is paramount for ensuring safety and functionality. First and foremost, always consult local codes and regulations regarding installation procedures specific to hazardous locations. Properly sealing all joints and ensuring tight connections will help prevent any potential leaks of ignitable gases into the electrical system.
During installation of an explosion proof outlet or any related components, it's vital to use tools that are compatible with the materials involved—this means avoiding tools that might create sparks during use. Additionally, ensure that you have clear access to all parts being installed; cramped spaces can lead to mistakes or oversights which could compromise safety standards. Regular inspections post-installation are also key; they ensure everything remains intact over time.
Importance of Professional Installation
While DIY projects can be tempting when dealing with electrical installations like explosion proof outlet setups, enlisting professional help is strongly advised when dealing with hazardous environments. Professionals bring expertise in understanding what is the difference between ATEX and explosion proof systems—knowledge crucial for compliance with safety regulations specific to your industry needs.
Moreover, professionals are trained in identifying potential hazards during installation processes, which may not be immediately apparent to untrained individuals. They also possess experience using specialized equipment necessary for proper installation of components such as an explosion-proof receptacle box or appropriate cabling techniques required by local codes. Ultimately, investing in professional installation not only ensures adherence to safety standards but also enhances the longevity of your electrical systems while minimizing risks associated with improper setups.
Explosion Proof Outlet Installation
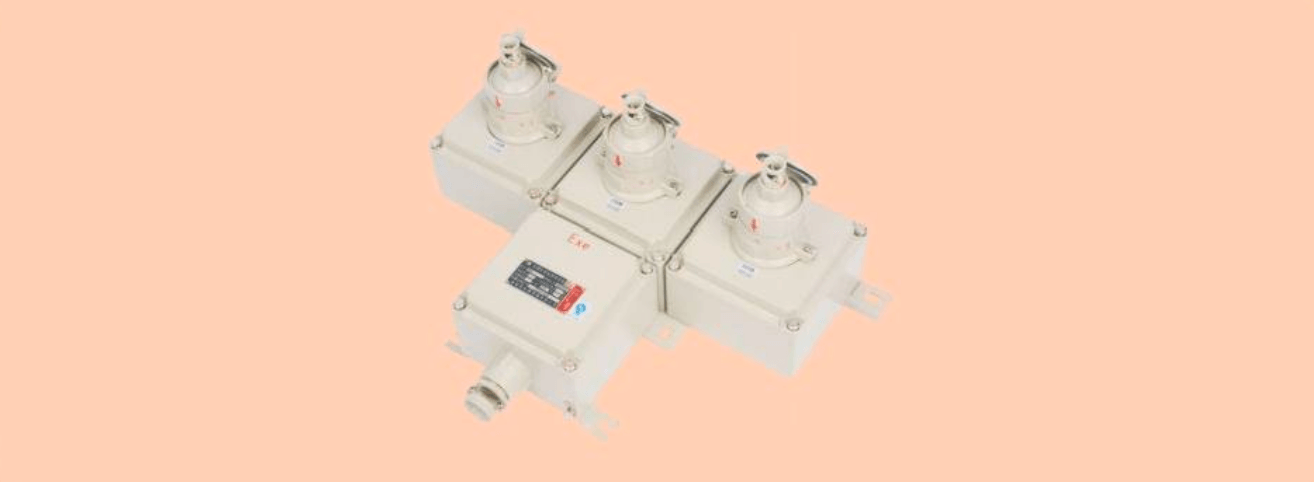
Installing an explosion proof outlet is crucial for maintaining safety in hazardous environments. These specialized outlets are designed to prevent ignition of flammable gases or dust, making their proper installation vital. Following a systematic approach ensures that you get it right the first time, minimizing risks associated with improper setups.
Step-by-Step Installation Process
To begin the installation of an explosion proof outlet, first, ensure that you have all necessary tools and materials at hand. Start by turning off the power supply to the area where you'll be working to avoid any electrical hazards. Next, remove the existing outlet if applicable; this may involve unscrewing it from its receptacle box or disconnecting wiring.
Once the old outlet is out, prepare your new explosion proof socket by carefully reading its installation instructions. Connect the wiring according to standard practices for explosion proof wiring; typically, this involves matching color-coded wires and ensuring secure connections using appropriate fittings. After securing everything in place, carefully mount your explosion-proof receptacle box and ensure a tight seal before restoring power.
Finally, test your newly installed outlet to confirm that it functions correctly without any issues. Make sure there are no loose connections or exposed wires that could lead to failure in hazardous conditions. Remember: proper installation ensures not just functionality but also safety in potentially explosive environments.
Tools and Equipment You’ll Need
Before diving into your explosion proof outlet installation project, gather all necessary tools and equipment for a smooth process. You'll need basic electrical tools such as screwdrivers (flathead and Phillips), wire strippers, pliers, and a multimeter for testing connections once you're done.
Additionally, having an appropriate explosion-proof receptacle box is essential for housing your new socket securely while keeping it safe from environmental hazards. Don’t forget personal protective equipment (PPE) like gloves and safety glasses to protect yourself during the installation process—safety first!
Lastly, consider having a torque wrench handy for tightening screws properly without overdoing it; this will help maintain the integrity of seals essential for preventing explosions in sensitive areas.
Safety Precautions to Follow
Safety should always be at the forefront when dealing with electrical installations—especially when working with an explosion proof outlet! Begin by ensuring that you turn off power at both circuit breakers and any local switches before starting work on your outlet; this minimizes shock risk significantly.
Moreover, make sure you're wearing appropriate PPE throughout the process; gloves can prevent cuts from sharp edges while safety glasses shield against debris during installation tasks like drilling or cutting materials. Additionally, always double-check connections before sealing up your work; loose wires can lead to dangerous situations down the line.
Lastly, familiarize yourself with emergency procedures related to electrical fires or explosions specific to your environment prior to beginning work on an explosion-proof socket install—knowledge is power! Keeping these precautions in mind will help ensure not only successful installations but also peace of mind while operating within hazardous areas.
Explosion Proof Outlet Replacement

When it comes to maintaining safety in hazardous environments, knowing when to replace your explosion proof outlet is crucial. Regular inspections are essential, and there are specific signs that indicate it’s time for a replacement. If you notice visible damage, such as cracks or corrosion on the outlet or its casing, it's a clear signal that the integrity of the explosion-proof receptacle box has been compromised and should be addressed immediately.
Signs It’s Time to Replace Your Outlets
One of the primary signs that you need an explosion proof outlet replacement is frequent tripping of circuit breakers associated with these outlets. This could suggest internal faults or degradation over time, posing potential risks in explosive atmospheres. Additionally, if your outlet shows signs of overheating—like discoloration or a burning smell—it's time to act swiftly, as this can lead to dangerous situations.
Another indicator is inconsistent performance; if devices plugged into the explosion proof socket are malfunctioning or not receiving power consistently, it may point toward an underlying issue with the outlet itself. Regular wear and tear from environmental factors can also take their toll on these outlets, so keeping an eye out for any unusual changes is wise. Finally, if your facility has undergone changes in equipment or processes that increase risk levels beyond what was previously assessed, reviewing your current outlets for adequacy is essential.
How to Choose the Right Replacement
Choosing the right replacement for your explosion proof outlet involves understanding both specifications and compliance standards relevant to your environment. Start by confirming whether you're looking for a traditional explosion proof socket or one certified under ATEX standards; knowing what is the difference between ATEX and explosion proof will guide you in making an informed decision based on regulatory requirements.
Next, consider the specific application needs—does it require additional features like pressure relief mechanisms or enhanced sealing techniques? Understanding how do explosion proof outlets work can help you select one that meets those unique requirements effectively while ensuring safety remains uncompromised.
Lastly, don’t overlook material compatibility; common materials used in manufacturing these sockets include aluminum and stainless steel due to their durability and resistance against corrosive environments. Opting for high-quality products ensures longevity and reliability in potentially hazardous settings.
Tips for a Smooth Replacement Process
Replacing an explosion proof outlet isn’t just about swapping out old for new; following best practices can make all the difference in ensuring safety and effectiveness throughout installation. First off, always prioritize safety by disconnecting power before attempting any work on electrical systems—this cannot be overstated! Properly labeling wires during removal will also save you headaches later when installing your new outlet.
When performing an explosion proof outlet installation, ensure that you're using appropriate tools designed specifically for this type of work; this includes screwdrivers with insulated handles and torque wrenches calibrated correctly according to manufacturer specifications. Additionally, double-check all connections post-installation to ensure everything aligns perfectly with what is considered proper explosion-proof wiring practices.
Finally, keep documentation handy regarding product specifications and previous installations—it not only aids future maintenance but also ensures compliance during inspections by regulatory bodies overseeing hazardous environments. By following these tips closely during your replacement process, you'll contribute significantly towards maintaining a safe working atmosphere while maximizing equipment longevity.
Conclusion
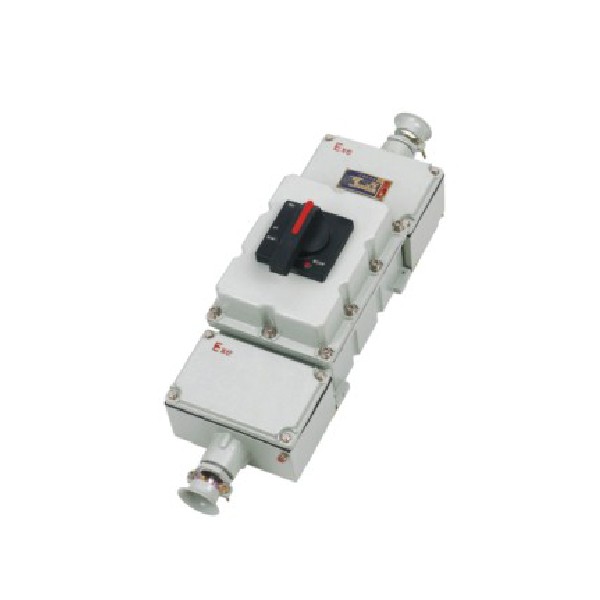
In summary, ensuring safety in hazardous environments is paramount, and explosion-proof solutions are a crucial aspect of this endeavor. By investing in the right explosion proof outlet and understanding how do explosion proof outlets work, you can significantly reduce the risk of accidents. Whether it’s for industrial applications or specialized settings like laboratories, these sockets provide peace of mind.
Ensuring Safety with Explosion-Proof Solutions
Safety should always be your top priority when dealing with potentially explosive environments. An explosion proof socket is designed to contain any sparks or flames that may occur within the receptacle, preventing them from igniting surrounding gases or dust. Understanding what is an explosion proof socket and its features can help you select the best options for your specific needs.
Investing in Quality Products for Longevity
When it comes to electrical installations in hazardous areas, skimping on quality can lead to dire consequences. Investing in high-quality explosion proof wiring and components ensures that your systems remain operational for years without frequent failures or replacements. Remember, a reliable explosion-proof receptacle box not only protects equipment but also safeguards lives—making it worth every penny.
How Jinrong Can Support Your Needs
Jinrong stands out as a trusted provider of explosion-proof solutions tailored to meet various industry standards. From offering detailed guidance on explosion proof outlet installation to providing top-notch products that comply with ATEX regulations, we have you covered! Whether you're looking into options for an upcoming project or need assistance with an explosion proof outlet replacement, Jinrong is here to help every step of the way.