Introduction
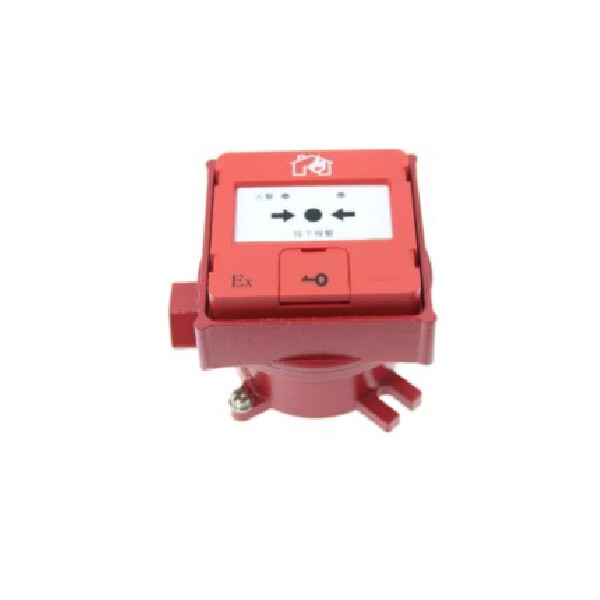
In industries where flammable materials are present, understanding explosion proof classification is not just a regulatory requirement; it’s a matter of life and death. Navigating the complexities of hazardous areas requires a firm grasp of safety standards that dictate how equipment should be designed and used to minimize risks. This introduction will set the stage for exploring essential topics such as ATEX and EX classification, classification zones for explosions, and the intricacies of class 1, class 2, and class 3 hazardous locations.
Understanding Explosion Proof Classification
Explosion proof classification serves as the backbone of safety in environments where explosive atmospheres may occur. It categorizes equipment based on its ability to contain any potential explosions within designated enclosures, thus preventing ignition of surrounding flammable substances. By delving into what is ATEX and EX classification, we can better appreciate how these standards shape our approach to safety in hazardous locations.
The Importance of Safety Standards
Safety standards play a pivotal role in protecting workers from hazardous conditions that could lead to catastrophic events. They provide guidelines that help industries comply with legal requirements while ensuring that employees can operate safely within potentially dangerous environments. Without these standards, navigating hazardous areas would be akin to sailing without a compass—dangerous and unpredictable.
Navigating Hazardous Areas
Navigating hazardous areas demands an acute awareness of both environmental conditions and regulatory frameworks governing them. Understanding what are the classification zones for explosions allows organizations to implement appropriate measures tailored to specific risks associated with each zone type. From identifying class 1, class 2, and class 3 hazardous locations to recognizing what is the classification of explosion-proof enclosure necessary for safety compliance, knowledge is indeed power in these high-stakes situations.
What is ATEX and EX Classification?
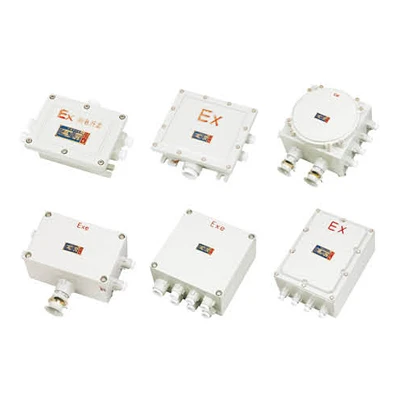
Overview of ATEX Directives
The ATEX directives consist of two main components: ATEX 114 (previously known as 94/9/EC) and ATEX 1999/92/EC. The first directive focuses on the equipment and protective systems intended for use in explosive atmospheres, while the second outlines the minimum safety requirements for workplaces where explosive atmospheres may occur. Understanding these directives is essential for ensuring compliance with safety regulations, making them a cornerstone of explosion proof classification.
In practical terms, these directives categorize equipment based on its suitability for use in various zones where flammable gases or dust may be present. This categorization helps organizations determine what type of protection measures are necessary, ultimately reducing the risk of accidents in hazardous locations.
The Role of EX Classification
The role of EX classification cannot be overstated; it serves as a guiding principle for identifying and mitigating risks associated with explosive environments. This classification includes designations such as gas groups and temperature classes that help define how equipment should be constructed to prevent ignition sources from causing explosions. By adhering to these classifications, companies can ensure their machinery meets stringent safety standards required by regulations like those set forth by ATEX.
Moreover, EX classification also plays a critical role in employee training and awareness programs within industries that deal with hazardous materials. Employees must understand what constitutes an explosion-proof enclosure versus standard equipment, allowing them to operate safely within designated zones without risking their lives or those around them.
Key Differences in Standards
While both ATEX and other international standards aim to ensure safety in hazardous environments, key differences exist between them that professionals must recognize. For instance, while ATEX focuses primarily on European markets, other standards like IECEx provide guidelines applicable globally but may differ slightly in terminology or specific requirements related to explosion proof classification.
Another notable difference lies in how each standard classifies hazardous locations—ATEX employs zone classifications (Zone 0, Zone 1, Zone 2), whereas North American standards utilize Class divisions (Class 1, Class 2). Understanding these distinctions is crucial when navigating compliance across different regions or sectors; failure to do so could result not only in regulatory penalties but also increased risks associated with unsafe practices.
In summary, grasping what is ATEX and EX classification forms the bedrock of effective risk management strategies across various industries facing explosive hazards. By familiarizing themselves with the nuances between different standards—alongside their implications on workplace safety—businesses can better protect their employees while maintaining operational efficiency.
What are the Classification Zones for Explosions?
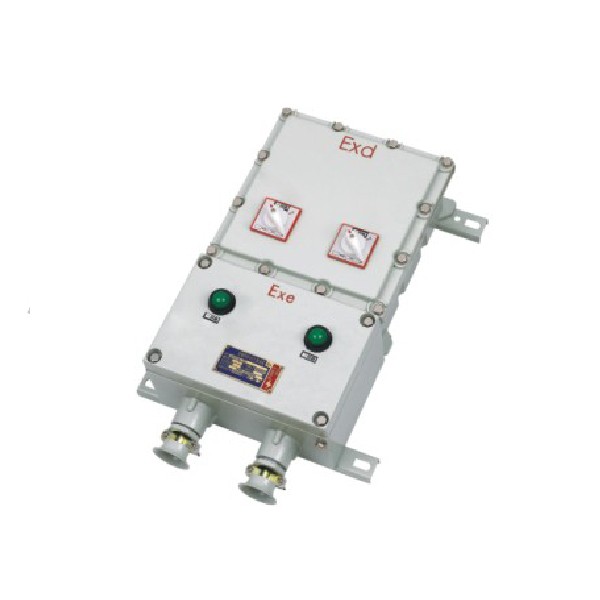
When it comes to ensuring safety in hazardous environments, understanding the classification zones for explosions is paramount. These zones help identify areas where flammable gases, vapors, or dust may be present, guiding the implementation of appropriate explosion proof classification measures. By categorizing these risks, industries can better protect personnel and equipment from potential explosions.
Defining Zone 0, Zone 1, Zone 2
Zone classifications are divided into three main categories: Zone 0, Zone 1, and Zone 2. **Zone 0** refers to areas where explosive gas atmospheres are continuously present or present for long periods. **Zone 1** covers locations where explosive atmospheres are likely to occur during normal operations but not continuously; this is often a transitional area between safe and hazardous zones. Lastly, **Zone 2** pertains to locations where explosive atmospheres are unlikely to occur during normal operations and exist only for short durations.
This clear delineation helps industries understand what is at stake in each zone when considering what is ATEX and EX classification standards. Accurate identification of these zones ensures that suitable safety measures are implemented based on the level of risk involved in each area. With proper classification comes the responsibility of adhering to stringent safety standards designed to mitigate risks associated with hazardous environments.
Importance of Accurate Zone Classification
Accurate zone classification is crucial because it directly impacts safety protocols and equipment design in potentially explosive atmospheres. Misclassifying a zone can lead to inadequate protective measures being employed, increasing the risk of accidents that could endanger lives and property alike. Moreover, understanding what are class 1, class 2, class 3 hazardous locations becomes easier when there’s clarity about explosion zones—ensuring compliance with regulations while promoting workplace safety.
Inaccurate classifications can also have legal ramifications; industries must adhere strictly to regulations set forth by organizations governing explosion proof classification standards such as ATEX directives or other local laws. The significance of accurate zone identification cannot be overstated—it lays the groundwork for effective hazard mitigation strategies tailored specifically for each environment's unique risks.
Examples of Zone Applications
To illustrate these concepts further, let’s examine real-world applications within each zone classification contextually related to explosion proof classification standards. In **Zone 0**, you might find areas like storage tanks containing volatile liquids constantly exposed to air; here strict adherence to ATEX guidelines is non-negotiable given the persistent risk of ignition sources nearby.
Moving on to **Zone 1**, typical examples include refineries or chemical processing plants where flammable vapors may escape during regular operations—this highlights why equipment used here must comply with rigorous Class I Division II specifications under what are class 1 locations guidelines ensuring they withstand potential hazards effectively.
Lastly, consider **Zone 2**, which could encompass places like maintenance shops adjacent but separate from production lines; while not normally exposed to gas releases under typical conditions (thus classified differently), it's essential that any tools or machinery used still meet minimal requirements set by relevant standards—ensuring no surprises arise should an unexpected situation occur!
What are Class 1, Class 2, Class 3 Hazardous Locations?
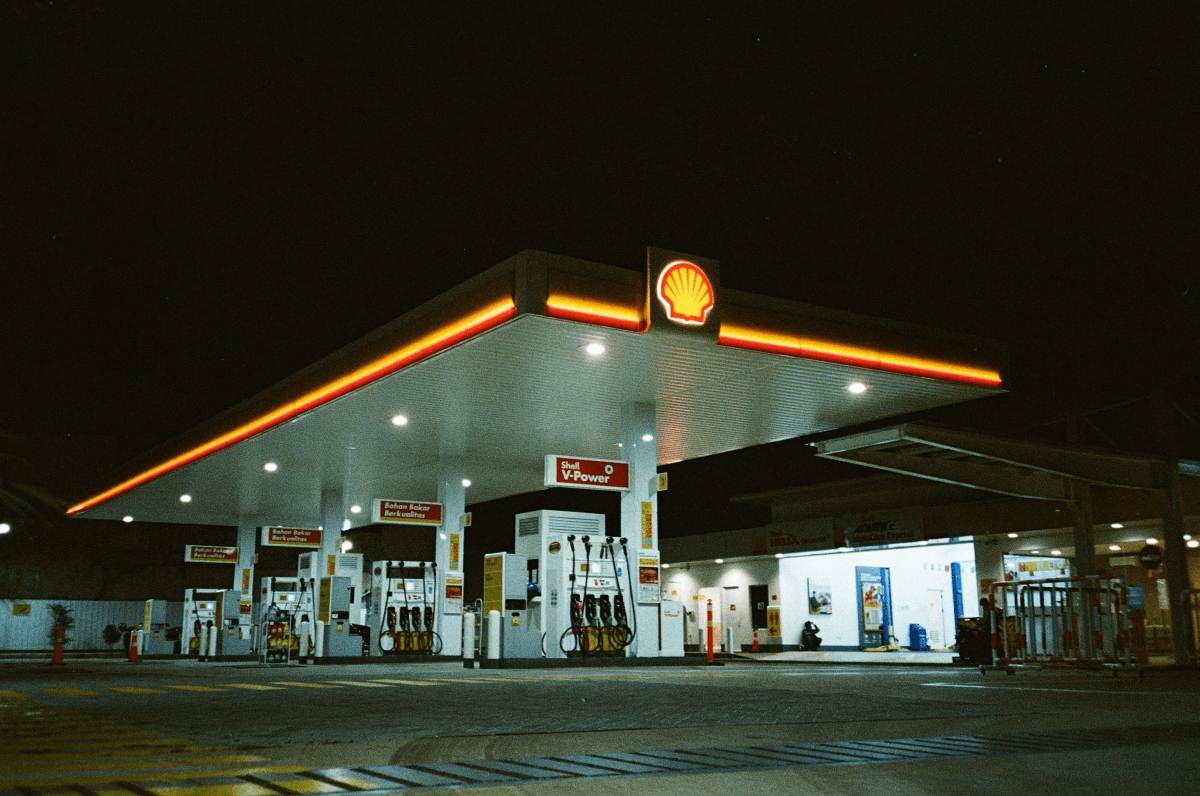
When it comes to explosion proof classification, understanding the distinctions between Class 1, Class 2, and Class 3 hazardous locations is crucial for safety and compliance in various industries. Each class represents a specific type of environment where flammable materials are present, necessitating tailored safety measures. This section will break down these classifications to help you navigate the complexities of hazardous areas effectively.
Breakdown of Class 1 Locations
Class 1 locations are defined as areas where flammable gases or vapors may be present in the air under normal operating conditions. These environments typically include petroleum refineries, chemical plants, and places where natural gas is processed or stored. Understanding what constitutes a Class 1 location is essential for implementing appropriate safety measures and selecting equipment that meets explosion proof classification standards.
The presence of flammable substances in these locations means that any electrical equipment must be designed to prevent ignition sources from causing an explosion. This is where the importance of knowing what is ATEX and EX classification comes into play; it ensures compliance with European directives focused on minimizing risks in hazardous areas. In summary, proper identification and management of Class 1 locations can significantly reduce workplace hazards.
Understanding Class 2 and Class 3 Hazards
Class 2 locations differ from their Class 1 counterparts by focusing on environments where combustible dusts are present but not necessarily gases or vapors. These hazardous areas can be found in grain handling facilities or metal processing plants where dust accumulation poses an explosion risk if ignited. The classification zones for explosions highlight that even seemingly benign materials like flour or sugar can create dangerous conditions when suspended in air.
On the other hand, Class 3 locations involve environments with easily ignitable fibers or flyings but do not have sufficient quantities to produce a fire hazard under normal conditions. Examples include textile manufacturing facilities where lint may accumulate without posing an immediate risk during regular operations. By understanding these classifications—Class 1 through Class 3—industries can better comply with regulations regarding what is the classification of explosion-proof enclosure requirements.
Real-World Examples of Each Class
Real-world examples help illustrate how each class operates within different industries and settings while emphasizing the importance of adhering to explosion proof classification standards. In a petroleum refinery (Class 1), you might find specialized equipment designed to contain potential leaks that could ignite due to flammable vapors present during processing activities.
For a grain elevator (Class 2), operators need to ensure proper ventilation systems are in place to minimize dust accumulation while utilizing equipment certified for explosive atmospheres created by combustible dusts during loading and unloading processes. Lastly, consider a textile mill (Class 3) where stringent housekeeping practices must be implemented regularly to reduce lint buildup around machinery—an often-overlooked aspect that plays a pivotal role in maintaining safety standards.
By recognizing these distinctions among Classes—alongside understanding what are the classification zones for explosions—you can better navigate compliance challenges while fostering safer work environments across diverse sectors.
What is the Classification of Explosion-Proof Enclosure?
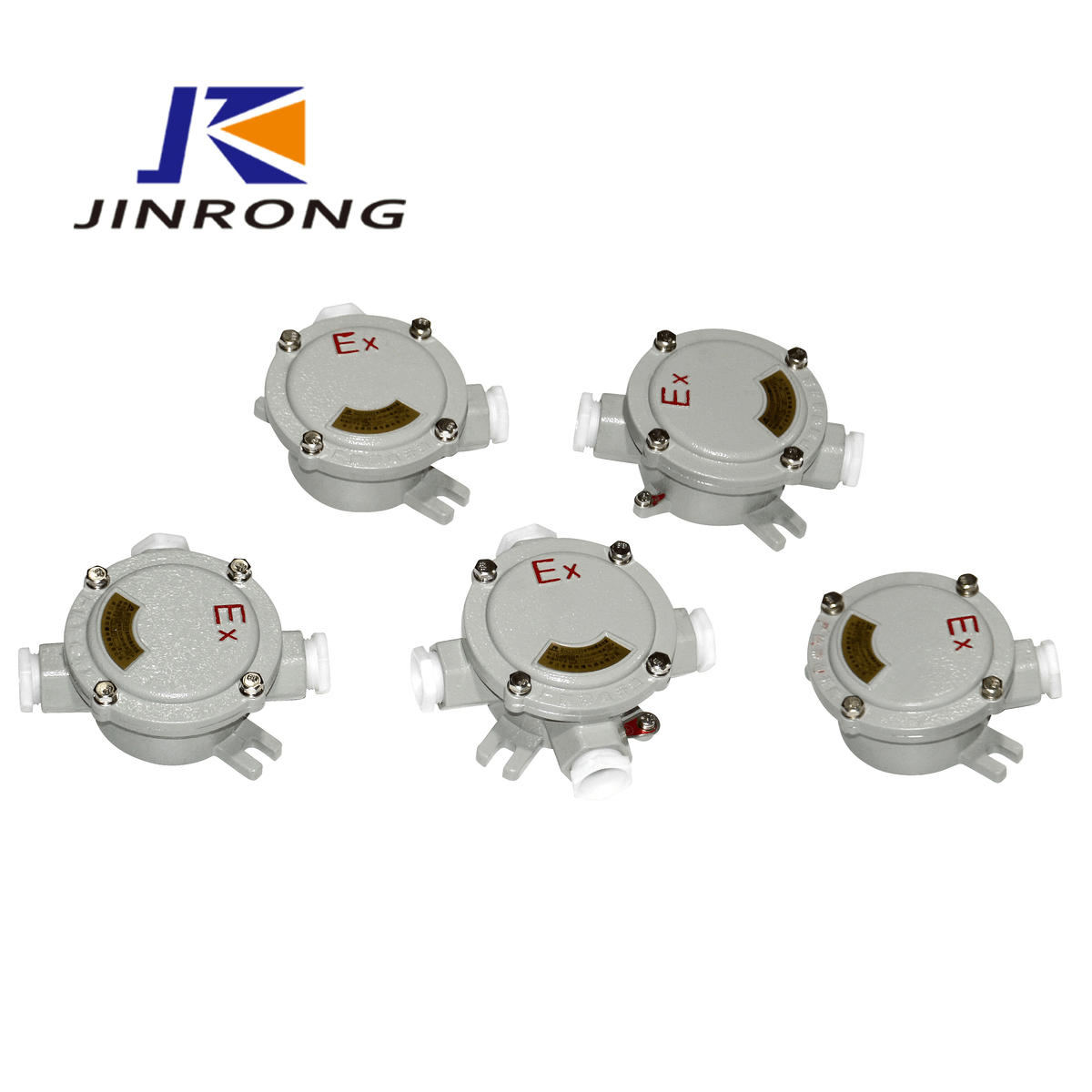
When it comes to ensuring safety in hazardous environments, explosion-proof enclosures play a pivotal role. These enclosures are designed to contain any potential explosions that may occur within them, preventing the ignition of surrounding flammable materials. Understanding the classification of these enclosures is essential for compliance with safety standards and effective risk management.
Definition of Explosion-Proof Enclosures
Explosion-proof enclosures are specially designed containers that house electrical equipment and other devices in environments where explosive gases or dust may be present. The primary function of these enclosures is to prevent an internal explosion from igniting external flammable substances, thereby safeguarding personnel and property. In essence, they provide a barrier between potential ignition sources and hazardous atmospheres, making them crucial in industries that operate under strict explosion proof classification guidelines.
Standards for Enclosure Design
The design of explosion-proof enclosures must adhere to stringent standards set forth by regulatory bodies such as ATEX (Atmosphères Explosibles) in Europe and NEC (National Electrical Code) in the United States. These standards dictate various aspects including material selection, construction methods, and testing procedures to ensure reliability under hazardous conditions. By complying with these rigorous design standards, manufacturers can produce enclosures that not only meet legal requirements but also provide peace of mind when navigating what are class 1, class 2, class 3 hazardous locations.
Importance of Certification in Enclosures
Certification plays a critical role in verifying that an explosion-proof enclosure meets established safety standards and regulations. This certification process involves rigorous testing by accredited organizations to ensure that the enclosure can withstand potential explosive forces without compromising its integrity. For businesses operating in hazardous areas, investing in certified explosion-proof equipment is not just about compliance; it's about fostering a culture of safety while navigating what is ATEX and EX classification effectively.
Innovative Solutions from Jinrong
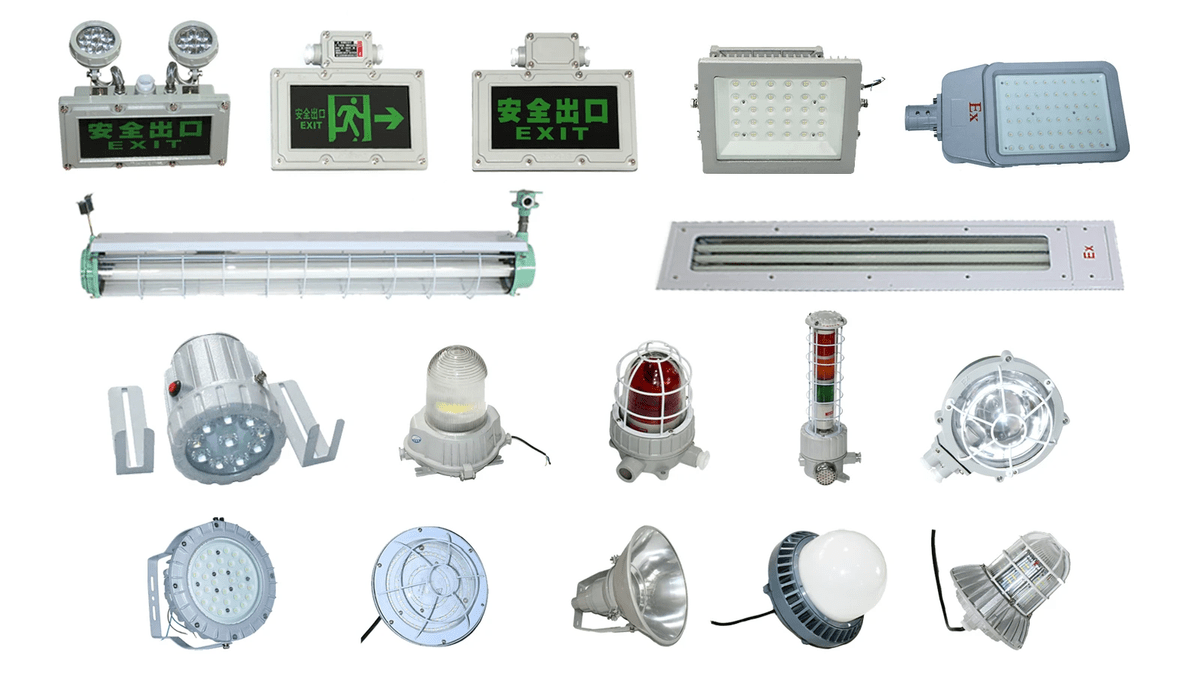
In a world where safety is paramount, Jinrong stands out as a beacon of expertise in explosion proof classification. With years of experience in the field, they have mastered the intricacies of what is ATEX and EX classification, ensuring that their products meet stringent safety standards. Their commitment to excellence not only enhances workplace safety but also fosters confidence among clients operating in hazardous environments.
Overview of Jinrong’s Expertise
Jinrong's expertise lies deeply rooted in understanding the complexities surrounding hazardous locations and their specific needs. They are well-versed in what are the classification zones for explosions, which allows them to tailor solutions that fit various industrial applications. This knowledge enables them to provide clients with reliable guidance on navigating through the labyrinth of regulations and standards necessary for compliance.
Product Range in Explosion Proof Equipment
Jinrong offers an extensive product range designed specifically for explosion proof classification, catering to diverse industries such as oil and gas, chemical processing, and mining. Their equipment includes everything from explosion-proof enclosures to specialized lighting systems that comply with what are class 1, class 2, class 3 hazardous locations criteria. Each product is engineered with precision to ensure maximum safety while maintaining operational efficiency in potentially explosive environments.
Success Stories in Hazardous Area Safety
The success stories emerging from Jinrong’s partnerships highlight their effectiveness in enhancing safety within hazardous areas across various sectors. For instance, a major oil refinery turned to Jinrong when they needed solutions compliant with what is the classification of explosion-proof enclosure requirements; the result was a significant reduction in incidents related to explosive atmospheres. By implementing Jinrong's innovative products and expert advice, companies have not only improved their safety records but also streamlined operations within classified zones.
Conclusion
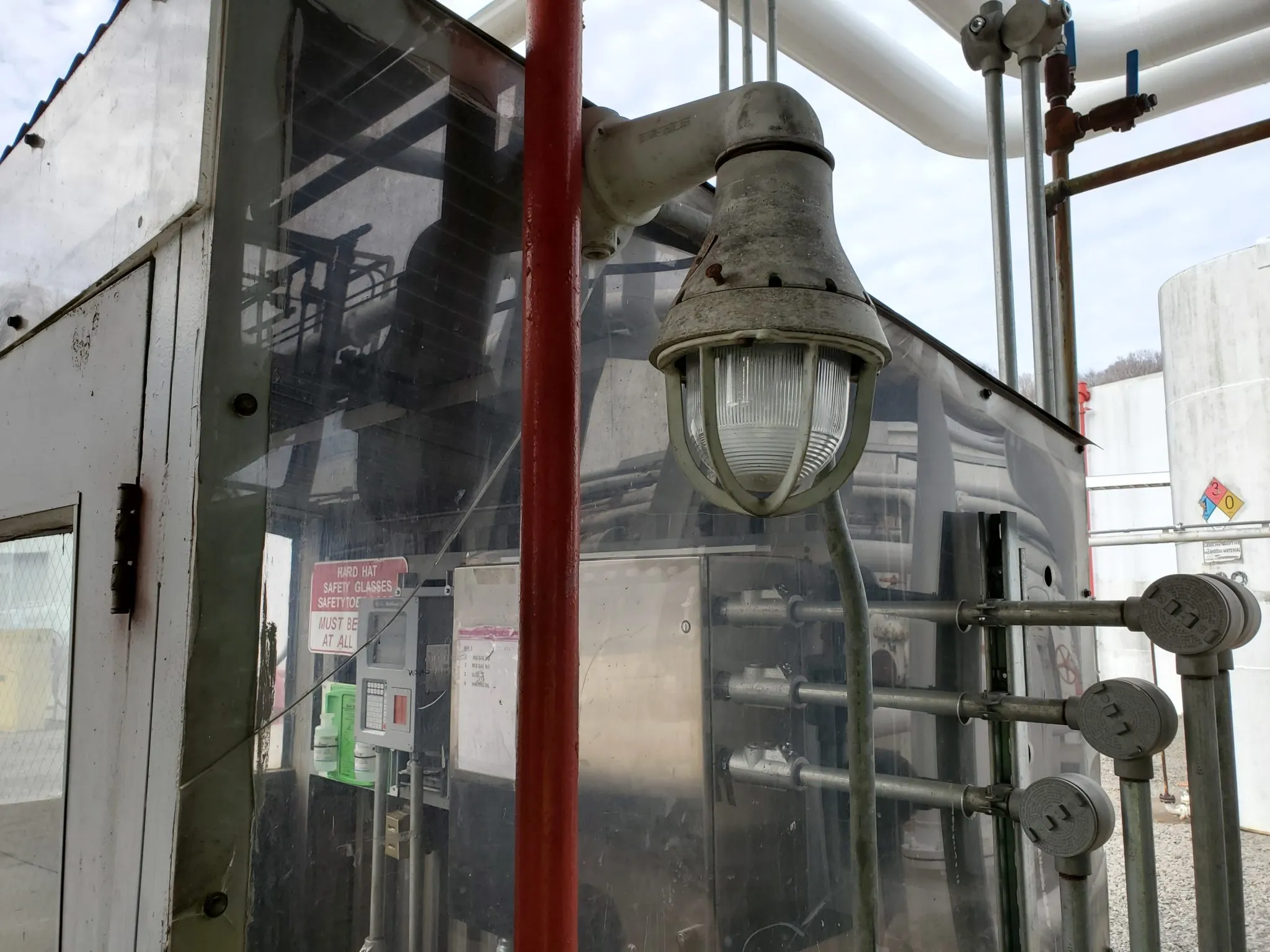
In the ever-evolving landscape of industrial safety, understanding explosion proof classification is not just a matter of compliance; it’s a necessity. With stringent regulations like ATEX and EX classification in place, industries must prioritize safety to protect their workers and assets. As we’ve explored, the classification zones for explosions play a critical role in determining the appropriate measures needed to mitigate risks in hazardous locations.
Crucial Safety Standards for Industries
Safety standards are the backbone of any industry handling flammable materials or operating in potentially explosive environments. The significance of understanding what are Class 1, Class 2, and Class 3 hazardous locations cannot be overstated; these classifications help define the level of risk associated with different environments. By adhering to established standards, businesses can ensure they are not only compliant but also fostering a culture of safety that protects employees and minimizes liability.
Staying Informed on Classification Changes
The world of explosion proof classification is dynamic, with ongoing updates and changes to regulations that can impact how industries operate. Staying informed about what is ATEX and EX classification is crucial for organizations striving to maintain compliance while ensuring worker safety. Regular training sessions and updates from regulatory bodies can help businesses keep pace with changes in classification zones for explosions, ensuring they remain ahead of potential hazards.
Partnering with Experts for Compliance
Navigating the complexities of explosion proof classification requires expertise that many organizations may not possess internally. Partnering with experts who understand what is the classification of explosion-proof enclosure can provide invaluable guidance in selecting appropriate equipment and implementing necessary safety measures. Collaborating with knowledgeable professionals ensures that companies not only meet compliance requirements but also enhance their overall operational efficiency.