Introduction
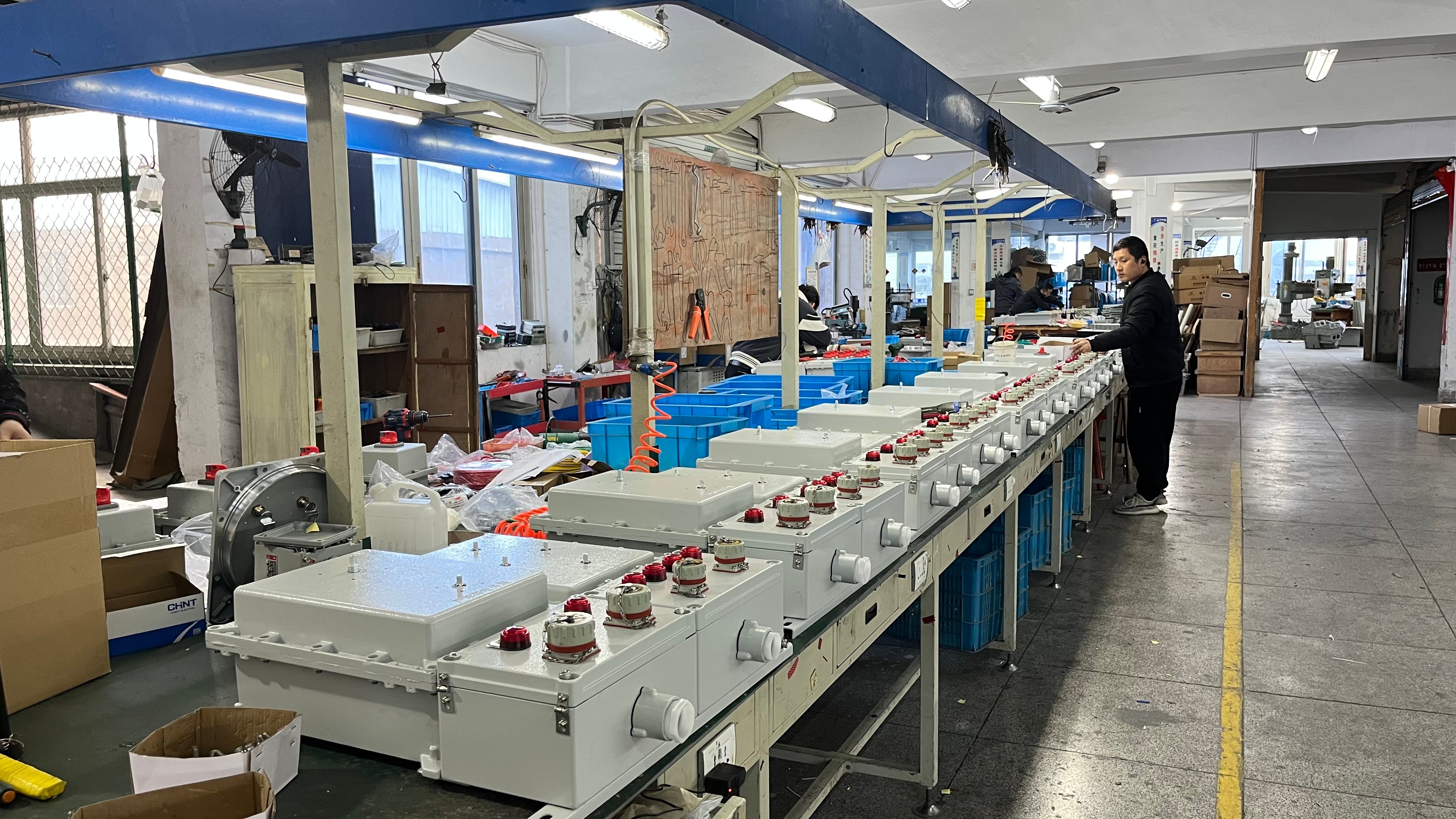
When it comes to factory lighting, understanding the guidelines and requirements is crucial for creating a safe and efficient work environment. Proper lighting not only enhances productivity but also ensures the safety of workers. Designing a lighting system for factories involves careful consideration of various factors, from illuminance levels to energy efficiency and compliance with industry standards.
Understanding Factory Lighting Requirements
Meeting the specific lighting needs of different areas within a factory is essential for ensuring optimal working conditions. From assembly lines to storage areas, each space requires a tailored lighting solution to meet the tasks performed and the safety standards in place.
Importance of Safe and Efficient Lighting in Factories
Safe and efficient lighting in factories is vital for maintaining a productive and secure work environment. Proper illumination reduces the risk of accidents, improves visibility, and contributes to employee well-being. It also plays a key role in meeting regulatory requirements related to workplace safety.
Key Considerations for Factory Lighting Design
Designing factory lighting involves considering various factors such as illuminance levels, color rendering index (CRI) standards, energy efficiency, cost considerations, and compliance with industry regulations. By carefully addressing these key considerations, it's possible to create a lighting system that meets both functional needs and safety requirements.
General Requirements for Factory Lighting
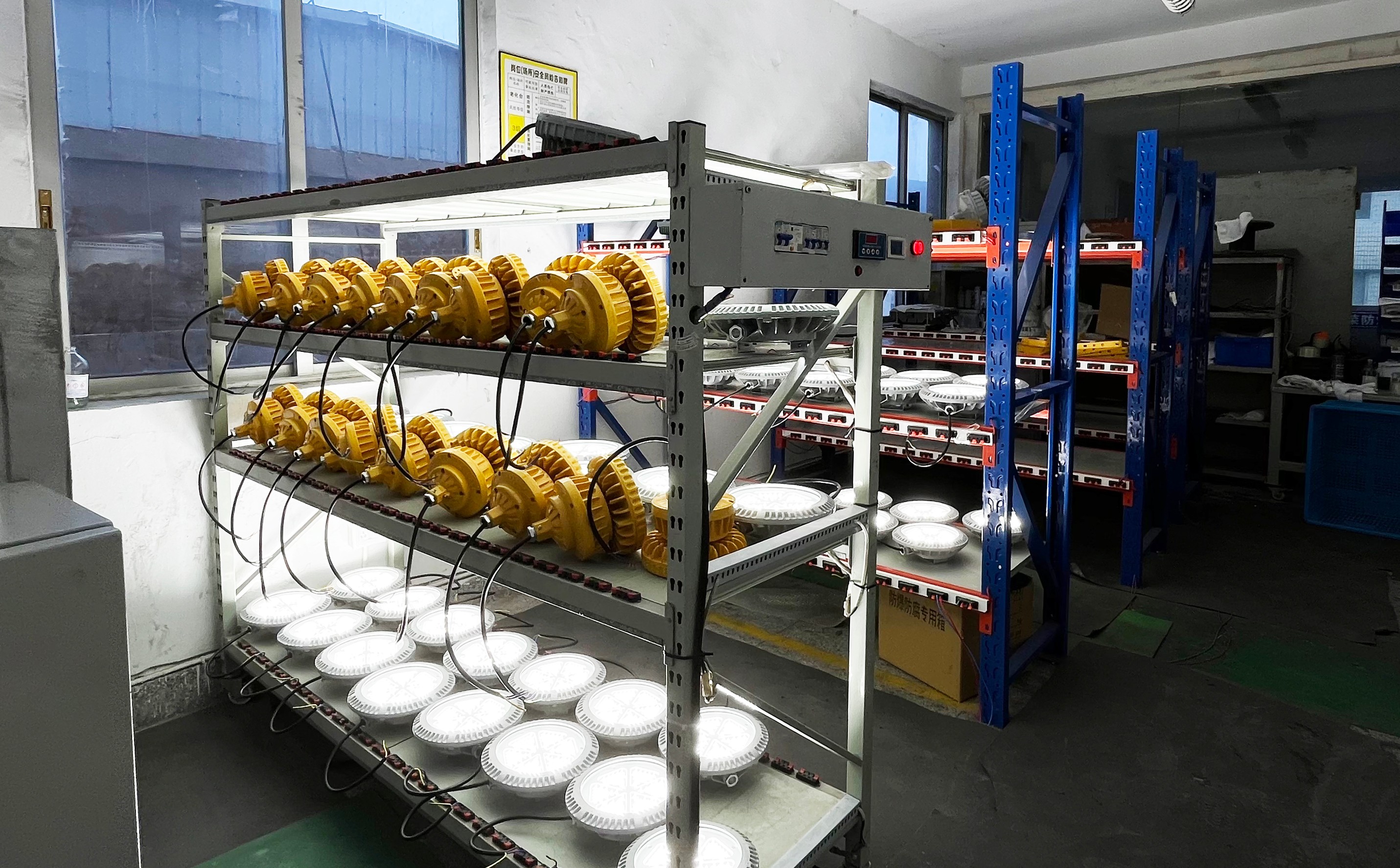
When it comes to factory lighting, there are several important factors to consider in order to ensure a safe and efficient working environment. Illuminance levels for different areas within the factory must meet specific guidelines to provide adequate lighting for tasks such as assembly, inspection, and maintenance. Additionally, color rendering index (CRI) standards play a crucial role in ensuring that workers can accurately distinguish between different colors of wires, labels, and other important details. Energy efficiency and cost considerations are also essential, as they impact both the environmental sustainability of the factory and its overall operational expenses.
Illuminance Levels for Different Areas
Different areas within a factory have varying lighting needs based on the specific tasks performed in each space. For example, assembly lines may require higher illuminance levels to ensure clear visibility of small components and intricate details, while storage areas may need lower levels of lighting. Understanding these requirements is crucial in designing an effective lighting system that meets the needs of all work areas.
Color Rendering Index (CRI) Standards
Color rendering index (CRI) standards are used to measure how accurately a light source displays colors compared to natural sunlight. In a factory setting, high CRI lighting is essential for accurately identifying different colored materials and components. This is particularly important when working with electrical wiring or other products where color coding plays a critical role in safety and functionality.
Energy Efficiency and Cost Considerations
Energy efficiency is a key consideration when selecting lighting fixtures for a factory environment. Not only does energy-efficient lighting reduce operational costs by lowering electricity consumption, but it also contributes to sustainability efforts by reducing the carbon footprint of the facility. LED lighting options are often preferred due to their long lifespan and low energy consumption.
Explosion Proof Lighting Regulations
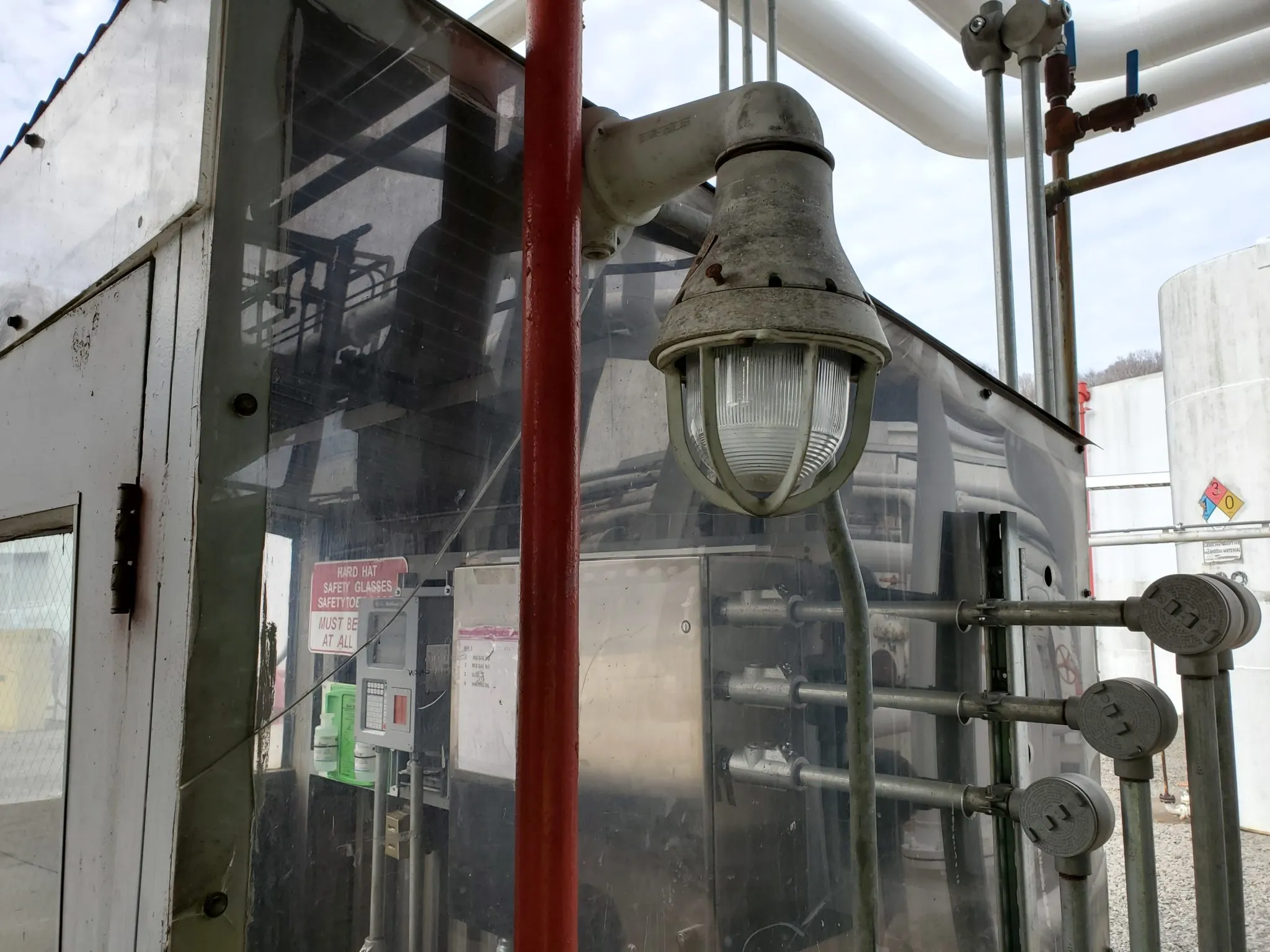
What is the Code for Explosion Proof Lighting?
When it comes to explosion proof lighting, it's crucial to adhere to strict codes and standards set by regulatory bodies such as the National Electric Code (NEC) and the Occupational Safety and Health Administration (OSHA). These codes outline specific requirements for designing, installing, and maintaining explosion proof lighting systems in hazardous locations within factories.
Where is Explosion Proof Lighting Required?
Explosion proof lighting is required in areas where flammable gases, vapors, or dust particles are present, such as chemical processing plants, oil refineries, grain elevators, and other industrial facilities. These hazardous environments necessitate the use of specialized lighting fixtures that prevent ignition of potentially explosive atmospheres.
Certification and Compliance for Explosion Proof Lighting
To ensure safety and compliance with regulations, explosion proof lighting fixtures must undergo rigorous testing and certification by accredited organizations. Manufacturers must provide documentation proving compliance with industry standards such as UL844 for Class I Division 1 locations or ATEX Directive for European markets.
Jinrong's Expertise in Ex-Proof Manufacturing
Jinrong has a proven track record of expertise in manufacturing high-quality explosion proof lighting solutions that meet stringent industry regulations. With a focus on innovation and safety, Jinrong offers a wide range of certified ex-proof fixtures designed to withstand harsh industrial environments while providing reliable illumination.
Factors to Consider for Explosion Proof Lighting
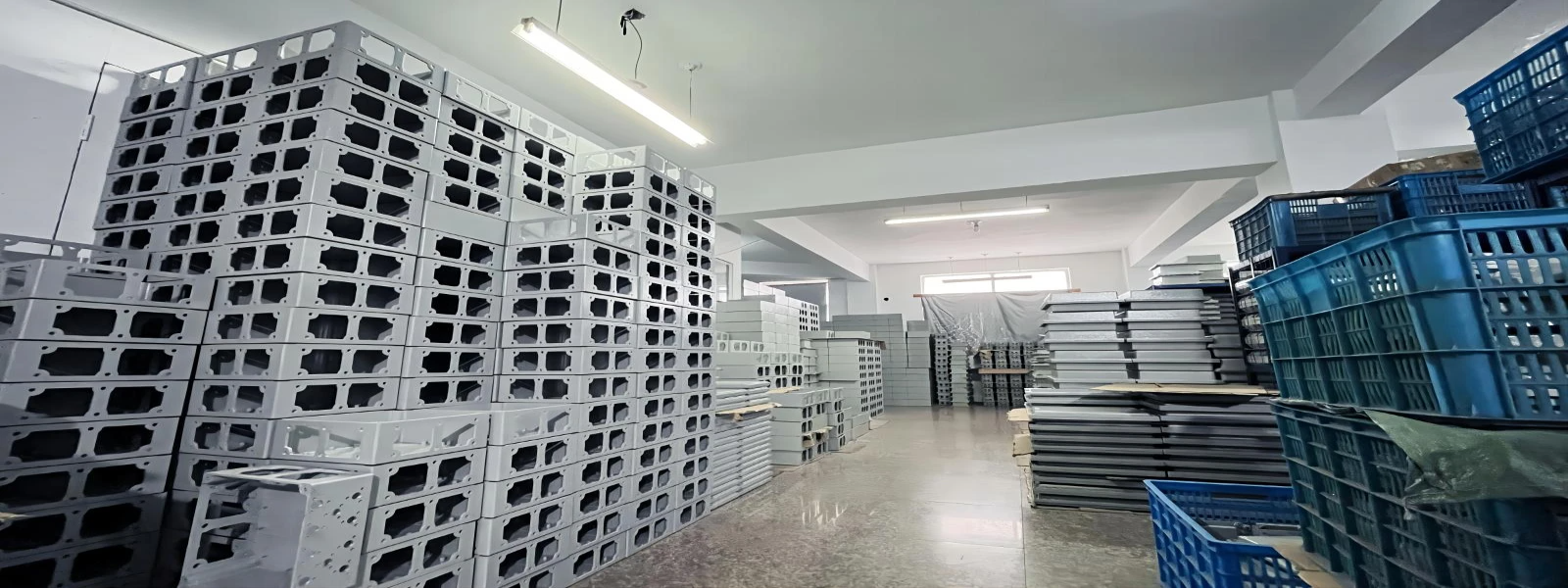
When considering explosion proof lighting, it is crucial to assess the environmental conditions and hazardous locations within the factory. Understanding where potentially explosive atmospheres may occur is essential for determining the appropriate lighting fixtures and ensuring compliance with safety regulations.
Environmental Conditions and Hazardous Locations
In order to meet factory lighting guidelines, it is important to identify areas where flammable gases, vapors, or dust may be present. These hazardous locations can include chemical processing plants, oil refineries, grain elevators, and other industrial settings where combustible materials are handled or stored.
In addition to identifying areas where flammable gases, vapors, or dust may be present, it is also crucial to consider the types of hazardous substances that could be encountered in these locations. For example, in chemical processing plants, there may be a variety of corrosive chemicals that could pose a risk if exposed to certain lighting fixtures. Understanding the specific substances present in these environments will help determine the most suitable lighting solutions to ensure safety and compliance with regulations.
Types of Hazardous Substances Present
Another key factor in designing explosion proof lighting systems is determining the specific types of hazardous substances that could be present in the environment. Different substances have varying levels of combustibility and reactivity, which must be taken into account when selecting suitable light fixtures.
Furthermore, the temperature ratings and durability of light fixtures are crucial considerations in explosion-proof lighting system design. The fixtures must be able to withstand high temperatures and harsh conditions without compromising their functionality or safety. This requires careful selection of materials and construction methods to ensure that the light fixtures can perform reliably in hazardous environments.
Temperature Ratings and Durability of Light Fixtures
When choosing explosion proof lighting fixtures, it is essential to consider their temperature ratings and durability. These fixtures must be able to withstand high temperatures and harsh conditions without posing a risk of ignition or failure, ensuring safety in potentially explosive atmospheres.
By carefully evaluating environmental conditions, types of hazardous substances present, and the durability of light fixtures, manufacturers can ensure that their explosion proof lighting systems meet general requirements for explosion proof light fixtures while complying with safety standards.
Designing a Safe and Efficient Lighting System
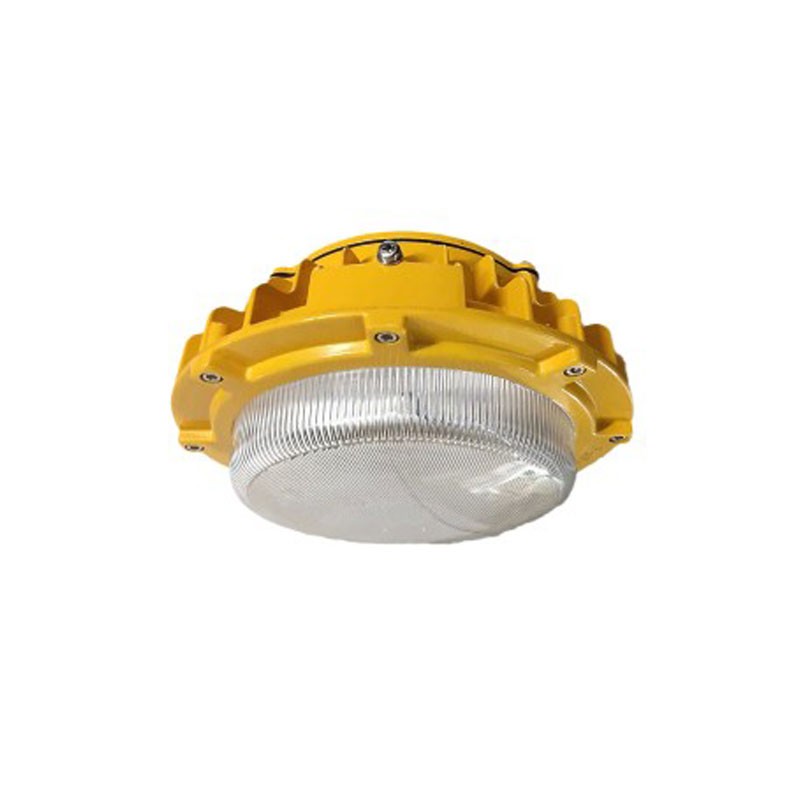
When it comes to designing a safe and efficient lighting system for your factory, it's essential to consider the best practices for placement and distribution of light fixtures. Proper spacing and positioning of fixtures can ensure uniform illumination throughout the workspace, minimizing shadows and glare. This not only enhances visibility but also contributes to a safer working environment for your employees.
Best Practices for Placement and Distribution of Light Fixtures
To optimize the effectiveness of your factory lighting, consider the layout of your workspace and the specific tasks performed in each area. High-bay fixtures are ideal for large open areas, while low-bay fixtures are better suited for lower ceilings or more confined spaces. Additionally, utilizing motion sensors or dimming controls can help conserve energy by adjusting light levels based on occupancy or natural daylight.
When considering the placement and distribution of light fixtures in your factory, it's important to take into account the specific tasks being performed in each area. For example, workstations that require detailed assembly or inspection may benefit from task lighting, such as adjustable LED fixtures or spotlights. These can be strategically placed to minimize glare and shadows, providing optimal visibility for workers. Additionally, incorporating daylight harvesting controls can further enhance energy efficiency by automatically adjusting light levels based on the amount of natural light available.
Maintenance and Cleaning Guidelines
Regular maintenance and cleaning of light fixtures are crucial to ensure optimal performance and longevity. Dust, dirt, and debris can accumulate on fixtures over time, reducing their efficiency and potentially creating safety hazards. Establishing a routine maintenance schedule for cleaning or replacing bulbs, lenses, or diffusers will help maintain consistent illumination levels while prolonging the lifespan of your lighting system. Additionally, incorporating regular inspections of wiring and connections can help identify any potential issues before they become major problems. This proactive approach can save time and money in the long run by preventing costly repairs or replacements.
Integration with Emergency Lighting Systems
Incorporating emergency lighting systems into your overall factory lighting design is essential to ensure safety during power outages or other emergencies. Emergency lights should be strategically placed in critical areas such as exit routes, stairwells, and assembly points to guide employees to safety in the event of an evacuation. Integrating these systems seamlessly with your primary lighting ensures uninterrupted visibility during unforeseen circumstances.
Conclusion
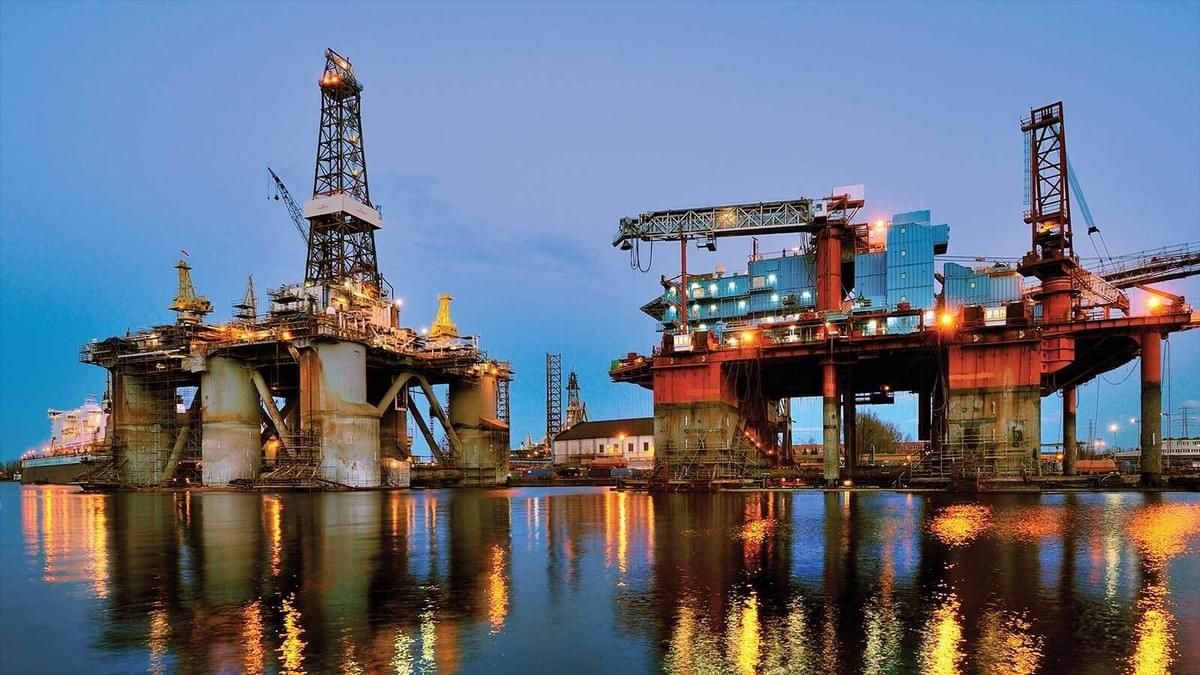
When it comes to choosing the right lighting solution for your factory, it's crucial to consider the general requirements of factory lighting as well as the specific requirements for explosion proof lighting. Understanding what is the code for explosion proof lighting and where it is required will ensure compliance with factory lighting standards. Partnering with Jinrong for expert guidance on explosion proof lighting | certification and compliance will guarantee a safe and efficient lighting system that meets all necessary guidelines.
Choosing the Right Lighting Solution for Your Factory
Selecting the appropriate lighting solution for your factory involves careful consideration of both general and explosion proof lighting guidelines. It's important to assess illuminance levels, color rendering index standards, energy efficiency, and cost considerations to ensure optimal performance. Additionally, understanding the specific requirements for explosion proof light fixtures in hazardous locations is essential for maintaining a safe working environment.
After carefully considering the general and explosion proof lighting guidelines, it's important to evaluate the illuminance levels required for different areas of the factory. This involves understanding the specific lighting needs for production floors, storage areas, and office spaces to ensure that the right amount of light is provided for each environment. Additionally, color rendering index standards should be taken into account to ensure that the lighting solution chosen accurately represents colors in the workspace, which is especially important for quality control and safety purposes.
Ensuring Compliance with Factory Lighting Standards
Compliance with factory lighting standards is non-negotiable when it comes to ensuring the safety and efficiency of your facility. Familiarizing yourself with the code for explosion proof lighting and its certification and compliance requirements will help you meet these standards effectively. By adhering to these regulations, you can guarantee that your factory's lighting system meets all necessary safety measures.
Partnering with Jinrong for Expert Guidance
Jinrong offers expertise in designing and manufacturing explosion proof light fixtures that comply with general requirements for explosion proof as well as factory lighting guidelines. Their knowledge of environmental conditions, hazardous substances, temperature ratings, and durability ensures that their products are tailored to meet specific needs while adhering to industry standards.
Remember, when it comes to choosing the right lighting solution for your factory, ensuring compliance with factory lighting standards is key. Partnering with Jinrong will provide you with expert guidance on meeting these requirements while also addressing specific needs related to explosion proof light fixtures in hazardous locations.