Introduction
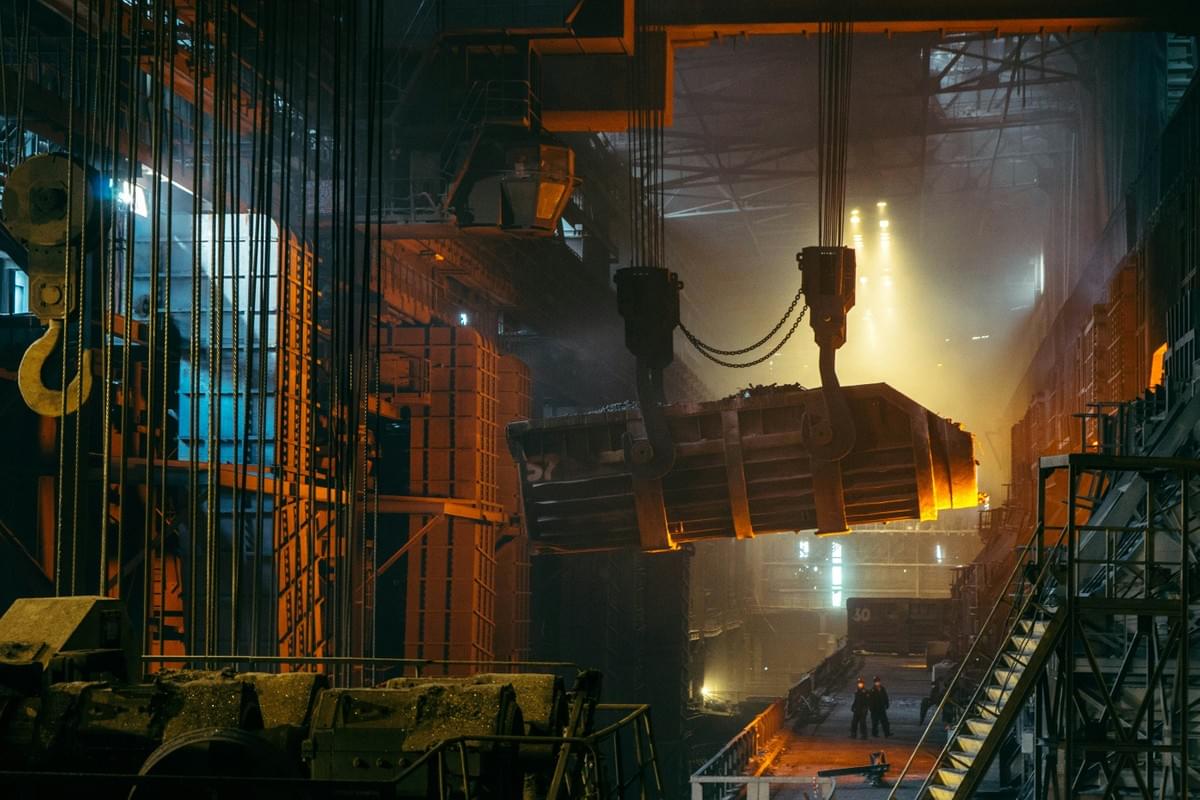
Mining, particularly sub-surface mining, is a critical industry that fuels economies and provides essential resources. However, the inherent dangers associated with this method of extraction cannot be overlooked. Ensuring safety in mining operations is not just a regulatory requirement; it’s a moral obligation to protect workers who brave the depths for our benefit.
The Importance of Safety in Mining
Safety in mining is paramount, as the risks involved can lead to catastrophic consequences if not properly managed. The importance of implementing robust safety measures cannot be overstated—each day, miners face hazards ranging from equipment failures to environmental threats. By prioritizing safety protocols and investing in advanced technologies like explosion-proof equipment, we can significantly reduce these risks and foster a safer working environment.
Understanding Sub-Surface Mining Risks
Sub-surface mining presents unique challenges that differ from surface mining techniques, including increased exposure to geological instabilities and toxic gases. Workers must navigate confined spaces where the risk of accidents escalates without proper safeguards in place. Understanding these specific risks is crucial for developing effective strategies aimed at minimizing hazards associated with sub-surface mining operations.
Exploring Innovative Solutions for Your Safety
To address the myriad risks faced by miners today, innovative solutions are emerging that leverage technology and enhanced equipment design. One such advancement is the development of explosion-proof equipment tailored specifically for sub-surface environments—this gear not only protects workers but also mitigates potential disasters before they occur. By exploring these cutting-edge solutions, mining companies can ensure their workforce remains safe while maximizing productivity.
What is Sub-Surface Mining?
Sub-surface mining is a method used to extract minerals and resources located beneath the earth's surface. Unlike surface mining, which removes soil and rock layers to access deposits, sub-surface mining involves digging tunnels or shafts to reach valuable materials buried deep underground. This technique is essential for accessing resources that are not easily reachable through other methods, making it a crucial component of the mining industry.
Defining Sub-Surface Mining Techniques
Sub-surface mining encompasses various techniques, including shaft mining, slope mining, and room-and-pillar mining. Shaft mining involves creating vertical shafts that lead directly to the mineral deposits, while slope mining utilizes sloped tunnels for easier access. Room-and-pillar mining creates a grid-like pattern of tunnels with pillars left behind to support the roof—each technique has its own unique advantages and challenges when it comes to efficiency and safety.
Key Differences from Other Mining Methods
One significant difference between sub-surface and other forms of mining lies in the depth at which resources are extracted. Surface mining typically operates on or near the earth's surface, while sub-surface methods delve much deeper into the ground. Additionally, sub-surface operations often require more advanced safety measures due to increased risks associated with working underground—this includes a greater reliance on explosion-proof equipment designed to minimize hazards during extraction.
Benefits and Challenges of Sub-Surface Mining
The benefits of sub-surface mining include its ability to access high-value mineral deposits that would otherwise remain untapped using surface techniques. Moreover, this method can have less environmental impact on the landscape compared to extensive surface excavation practices. However, challenges persist; workers face physical hazards such as cave-ins or toxic gas exposure, necessitating stringent safety protocols and reliable explosion-proof equipment to ensure their protection in these hazardous environments.
Common Hazards in Strip Mining
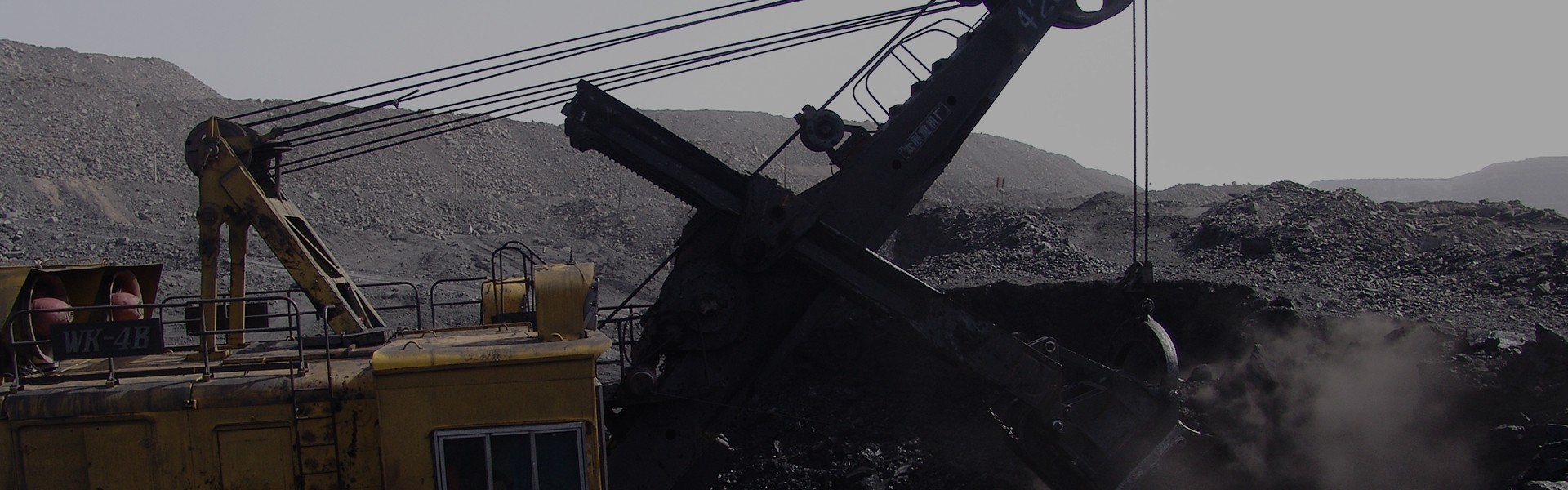
Strip mining, while an efficient method of extracting resources, is not without its dangers. Workers must navigate a landscape fraught with physical risks that can lead to serious injuries or even fatalities. Understanding these hazards is crucial for implementing effective safety measures and ensuring the well-being of those involved in sub-surface mining operations.
Identifying Physical Risks and Hazards
In strip mining, the most common physical risks include cave-ins, equipment accidents, and exposure to harmful substances. Cave-ins can occur when the structural integrity of the excavation site is compromised, leading to potentially life-threatening situations for workers below. Additionally, heavy machinery used in sub-surface mining presents a risk of accidents if proper safety protocols are not followed or if operators lack adequate training.
Another significant hazard involves exposure to toxic materials such as dust and fumes generated during extraction processes. These substances can lead to long-term health issues for miners if proper protective gear and ventilation systems are not utilized. Implementing explosion-proof equipment is essential in mitigating these risks; it ensures that machinery operates safely under hazardous conditions without triggering explosions from flammable materials commonly found in mining environments.
The Role of Environmental Conditions
Environmental conditions play a pivotal role in determining the safety of strip mining operations. Factors such as weather patterns, soil stability, and water drainage can significantly affect both operational efficiency and worker safety. For instance, heavy rainfall can lead to flooding or mudslides at mining sites, posing severe risks to workers who may find themselves trapped or injured.
Moreover, extreme temperatures—whether hot or cold—can impact both machinery performance and worker health. Inadequate heating or cooling systems increase the likelihood of heat stress or hypothermia among miners working underground for extended periods. Therefore, it’s critical for companies engaged in sub-surface mining to regularly assess environmental conditions and adjust their operational strategies accordingly.
Psychological Impact on Workers
The psychological impact on workers engaged in strip mining should not be overlooked; it can be just as detrimental as physical hazards. The constant awareness of potential dangers creates a high-stress environment that may lead to anxiety and decreased morale among workers over time. This mental strain can result in impaired focus and decision-making abilities—factors that could compromise safety protocols during critical tasks.
Additionally, job-related stressors such as long hours away from home contribute further to mental fatigue and burnout among miners. Creating a supportive work culture where employees feel valued and safe is essential for maintaining mental well-being within this high-risk industry. Companies must prioritize mental health initiatives alongside traditional safety measures like training programs focused on using explosion-proof equipment effectively.
Advanced Safety Solutions for Strip Mining
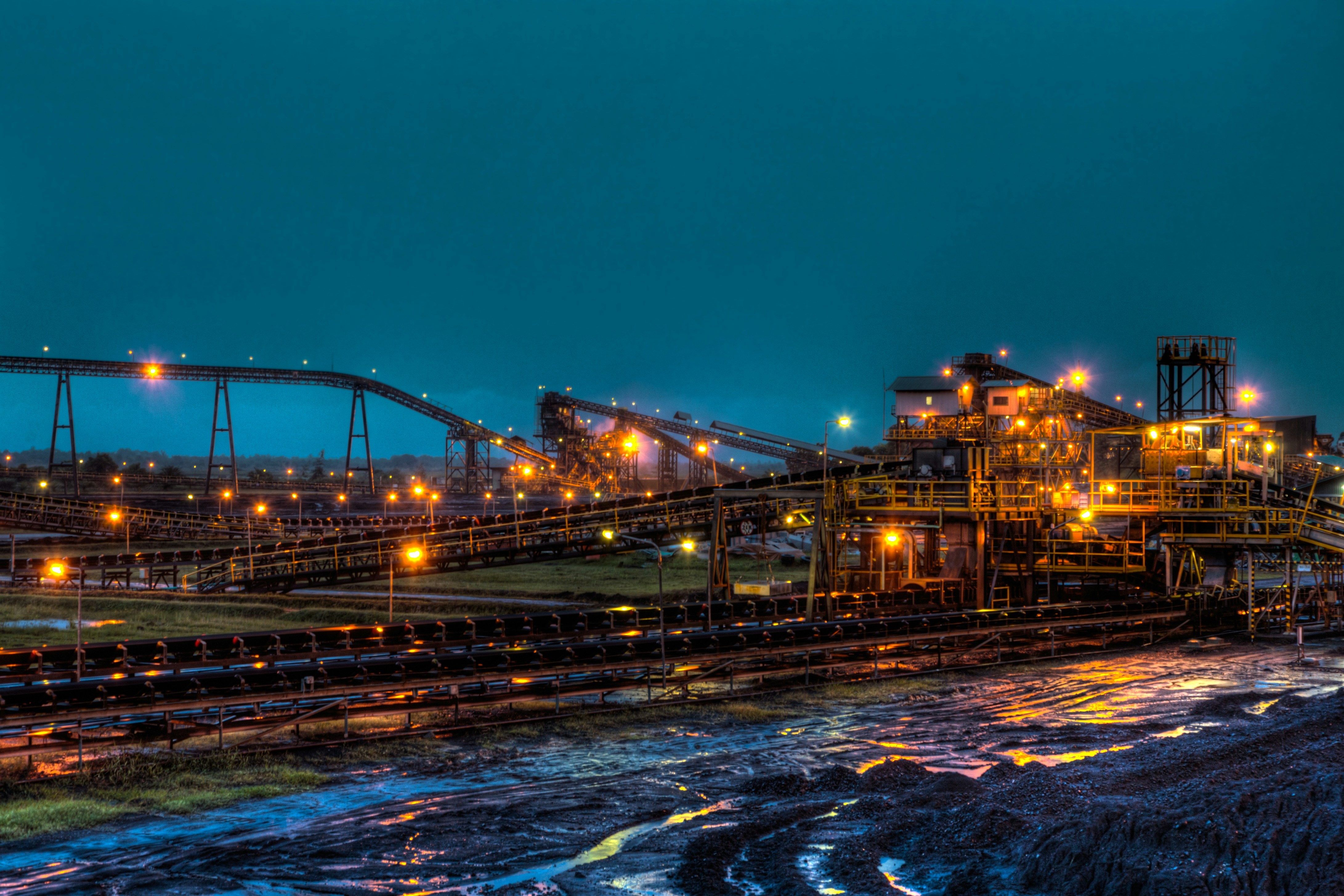
In the realm of strip mining, safety is paramount. As operations delve deeper into the earth, ensuring the well-being of workers becomes increasingly complex. This section explores advanced safety solutions designed to mitigate risks associated with sub-surface mining, focusing on explosion-proof equipment and innovative technologies.
The Necessity of Explosion-Proof Equipment
When it comes to sub-surface mining, the presence of flammable gases and dust makes explosion-proof equipment not just a luxury but a necessity. These specialized tools and machinery are engineered to prevent ignition in hazardous environments, protecting both workers and infrastructure from catastrophic events. Investing in explosion-proof equipment significantly reduces the risk of accidents, fostering a safer work environment where miners can focus on their tasks rather than worrying about potential explosions.
Moreover, using explosion-proof equipment enhances compliance with industry regulations that mandate safety measures in high-risk areas. Companies that prioritize this essential gear not only safeguard their workforce but also bolster their reputation as responsible operators in the mining sector. Ultimately, integrating such technology into daily operations is a proactive step towards minimizing risks inherent in sub-surface mining activities.
Incorporating Technology for Enhanced Safety
The integration of technology within strip mining operations has revolutionized safety protocols and practices. Advanced monitoring systems can detect gas leaks or structural weaknesses before they escalate into dangerous situations, allowing for timely interventions that save lives and resources alike. Moreover, wearable technology—such as smart helmets equipped with sensors—enables real-time health monitoring of miners, alerting them to potential hazards instantly.
Automation also plays a crucial role in enhancing safety by reducing human exposure to dangerous environments during critical phases of extraction or transport processes. Automated machinery can operate under conditions deemed unsafe for human workers, thus minimizing risk while maintaining productivity levels. Embracing these technological advancements ensures that companies engaged in sub-surface mining stay ahead of potential dangers while optimizing operational efficiency.
Case Studies: Successful Safety Implementations
Several companies have successfully implemented advanced safety solutions within their strip mining operations, showcasing how effective strategies can lead to significant improvements in worker safety and operational success. For instance, one major mining corporation adopted state-of-the-art explosion-proof equipment across its sites and reported a remarkable decrease in accident rates by over 40%. This case highlights how prioritizing such investments not only protects employees but also enhances overall productivity.
Another compelling example involves a firm utilizing drone technology for site inspections instead of sending personnel into potentially hazardous areas directly. By employing drones equipped with high-resolution cameras and gas detection sensors, they identified risks without endangering workers' lives—a game-changer for sub-surface mining operations aiming to improve safety standards efficiently. These case studies illustrate that when companies commit to innovative solutions like explosion-proof equipment and cutting-edge technologies, they pave the way for safer working environments across the industry.
Jinrong’s Contribution to Mining Safety
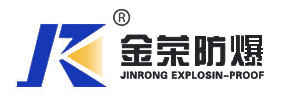
When it comes to sub-surface mining, safety is not just a priority; it’s a necessity. Jinrong has emerged as a leader in the industry by focusing on the development of explosion-proof equipment designed specifically for the unique challenges of mining environments. Their commitment to safety ensures that workers can operate with confidence, knowing they are protected against potential hazards.
Commitment to Explosion-Proof Equipment
Jinrong's dedication to producing explosion-proof equipment is rooted in a deep understanding of the risks associated with sub-surface mining. These specialized tools and machinery are engineered to withstand extreme conditions and prevent catastrophic incidents caused by flammable gases or dust explosions. By prioritizing safety in their designs, Jinrong not only protects workers but also enhances overall operational efficiency, making them an invaluable partner in mining safety.
Overview of Jinrong’s Product Range
The product range offered by Jinrong is extensive and tailored specifically for sub-surface mining applications. From advanced ventilation systems that manage air quality to robust drilling equipment designed for maximum durability, each product reflects their commitment to safety. Additionally, they offer training programs that help operators understand how to effectively use this explosion-proof equipment, ensuring that every aspect of worker safety is covered.
Customer Testimonials on Safety Improvements
Customers who have integrated Jinrong's explosion-proof equipment into their operations have seen significant improvements in workplace safety and efficiency. Many testimonials highlight how these innovations have drastically reduced accident rates and boosted employee morale among miners working in challenging conditions. With such positive feedback from industry professionals, it's clear that partnering with Jinrong leads not just to safer environments but also fosters a culture of responsibility and care within sub-surface mining operations.
Best Practices for a Safe Mining Environment
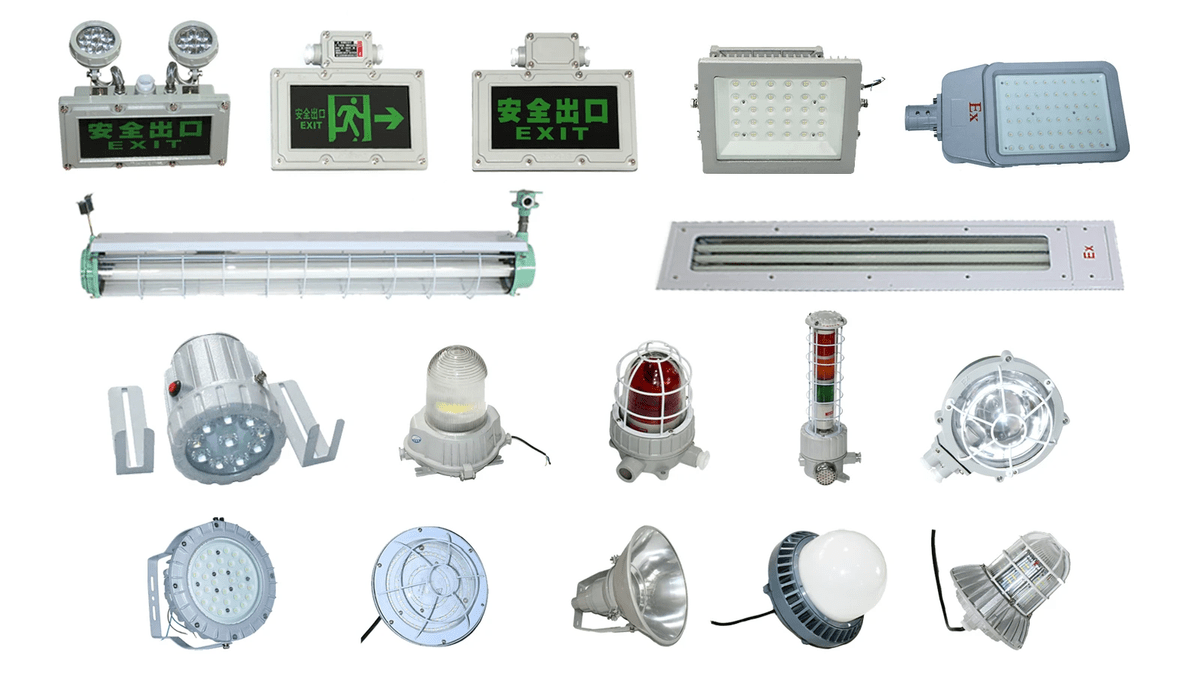
Creating a safe mining environment is crucial, especially in the realm of sub-surface mining where risks can be significantly heightened. Implementing best practices not only protects workers but also enhances operational efficiency. Here, we will explore key strategies that can bolster safety and promote a culture of vigilance throughout the mining operation.
Training and Educating Your Workforce
Training is the backbone of safety in sub-surface mining operations. Regularly scheduled training sessions ensure that all employees are well-versed in safety protocols, including the proper use of explosion-proof equipment. By educating your workforce about potential hazards and emergency procedures, you empower them to act decisively in critical situations, reducing the likelihood of accidents.
Moreover, ongoing education keeps workers updated on new technologies and practices that enhance safety measures. Incorporating hands-on training with simulation exercises allows employees to experience real-life scenarios without facing actual danger. This proactive approach fosters confidence among workers and reinforces their commitment to maintaining a safe work environment.
Regular Maintenance and Inspection Protocols
In sub-surface mining, equipment reliability is non-negotiable; this is where regular maintenance comes into play. Establishing strict inspection protocols for all machinery, especially explosion-proof equipment, helps identify potential issues before they escalate into serious problems. Scheduled checks not only prolong the lifespan of your equipment but also ensure that safety features are functioning correctly at all times.
Furthermore, keeping an organized log of maintenance activities provides transparency and accountability within your team. This documentation serves as a reference point during audits or inspections by regulatory bodies, showcasing your commitment to safety standards in sub-surface mining operations. Consistency in maintenance practices ultimately contributes to a safer working environment for everyone involved.
Building a Culture of Safety in Mining
Creating a culture of safety isn’t just about following rules; it’s about fostering an environment where every worker feels responsible for their own safety and that of their colleagues. In sub-surface mining operations, this cultural shift can be achieved through open communication channels where employees feel comfortable reporting unsafe conditions or suggesting improvements related to explosion-proof equipment usage.
Encouraging teamwork and collaboration among staff members further strengthens this culture; when workers look out for one another, it creates a sense of camaraderie that translates into safer practices on-site. Recognizing individuals or teams who demonstrate exceptional commitment to safety can serve as motivation for others to follow suit—after all, who doesn’t love being acknowledged for doing the right thing?
Ultimately, building this culture requires commitment from management down to entry-level positions; everyone must prioritize safety as part of their daily routine within the sub-surface mining industry.
Conclusion
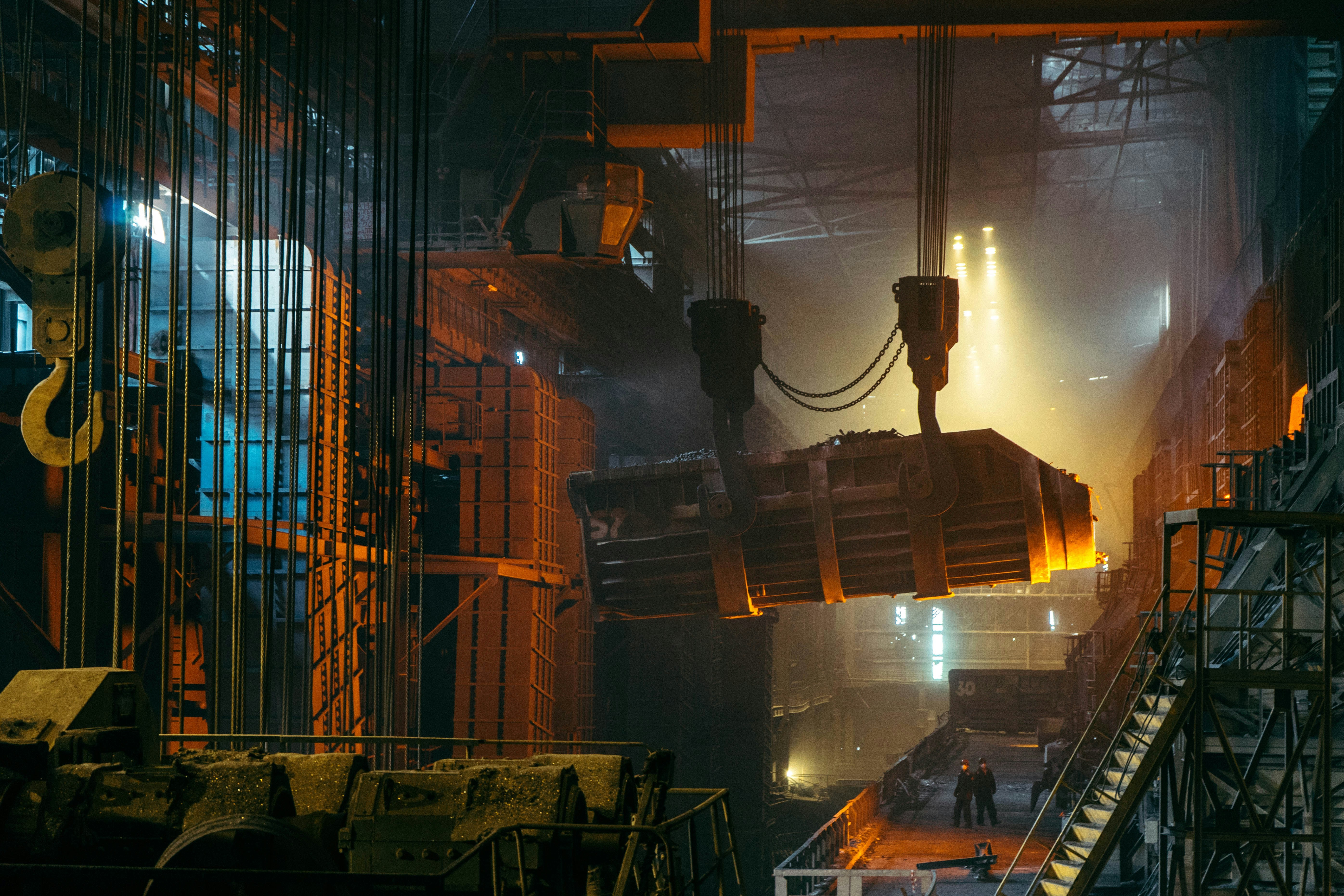
In the world of sub-surface mining, safety is not just a checkbox; it’s a fundamental principle that guides every operation. Implementing effective safety measures requires a proactive approach that encompasses rigorous training, advanced technology, and strict adherence to best practices. By prioritizing safety, mining operations can protect their workforce while optimizing productivity and efficiency.
Implementing Effective Safety Measures
To truly enhance safety in sub-surface mining, companies must adopt comprehensive protocols tailored to their specific environments. This includes regular risk assessments to identify potential hazards and ensure that all employees are equipped with explosion-proof equipment designed to withstand various dangers inherent in the mining process. Furthermore, fostering an ongoing culture of safety through training sessions and workshops can empower workers to recognize risks and take preventive actions proactively.
The Future of Safety in Sub-Surface Mining
Looking ahead, the future of safety in sub-surface mining promises exciting advancements driven by innovation and technology. With the integration of smart devices and real-time monitoring systems, miners will have unprecedented access to data that can predict hazards before they escalate into serious incidents. Moreover, as regulations continue to tighten around environmental impacts and worker safety, investment in cutting-edge explosion-proof equipment will become not just beneficial but essential for compliance and operational success.
Partnering with Experts for Maximum Safety
To achieve maximum safety in sub-surface mining operations, partnering with industry experts is crucial. These professionals bring invaluable insights into best practices for implementing effective safety measures while ensuring compliance with evolving regulations regarding explosion-proof equipment standards. Collaborating with specialists also allows companies to stay ahead of technological advancements that enhance workplace conditions—ultimately leading to safer environments for all involved.