Introduction
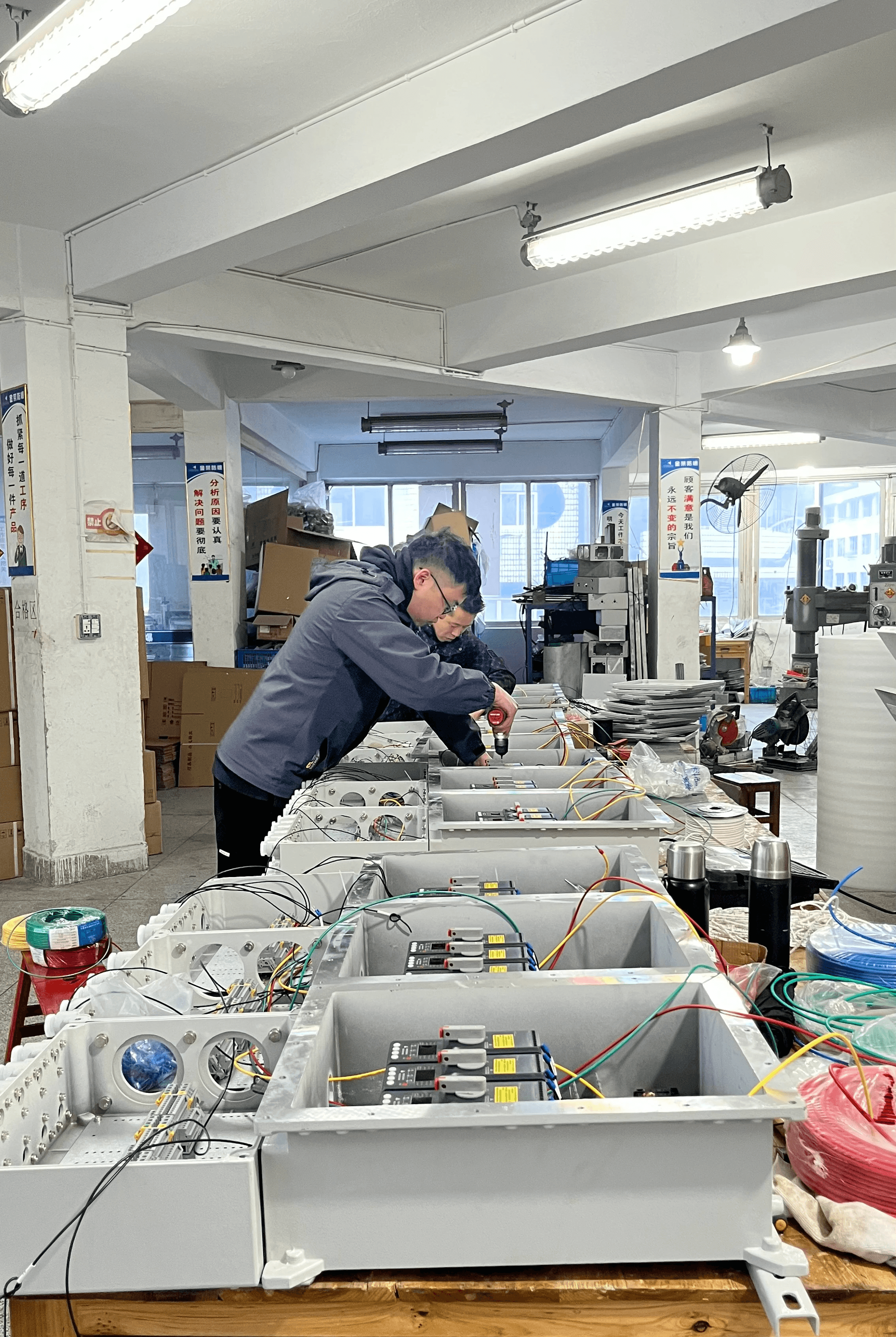
In an increasingly industrialized world, safety is paramount, especially in environments where flammable materials are present. Understanding intrinsic safety is crucial for ensuring that equipment and processes do not ignite hazardous substances. By delving into what is intrinsic safety, we can appreciate its significance in maintaining safe operational conditions.
Understanding the Basics of Intrinsic Safety
At its core, intrinsic safety refers to a design approach that limits the energy available for ignition in potentially explosive atmospheres. This means that even in the event of a fault, devices designed with intrinsic safety principles will not produce enough energy to cause an explosion. When asking what is meant by intrinsic safety?, it becomes clear that this methodology prioritizes prevention by incorporating specific engineering controls and protective measures.
The Role of Intrinsic Safety in Hazardous Areas
Intrinsic safety plays a vital role in hazardous areas such as oil rigs, chemical plants, and mining operations where flammable gases or dust are present. By ensuring that electrical equipment operates safely under these conditions, industries can significantly reduce the risk of catastrophic events. Moreover, understanding the difference between intrinsic and extrinsic safety helps stakeholders make informed decisions about which safety measures are best suited for their specific applications.
Why Intrinsic Safety Matters for Industries
The importance of intrinsic safety cannot be overstated; it directly impacts operational efficiency and worker protection in high-risk environments. Industries benefit from reduced downtime and lower accident rates when they implement robust intrinsic safety measures effectively. Furthermore, exploring what is the difference between functional safety and intrinsic safety reveals how integrating both approaches can lead to comprehensive risk management strategies tailored to unique industry needs.
What is Intrinsic Safety?
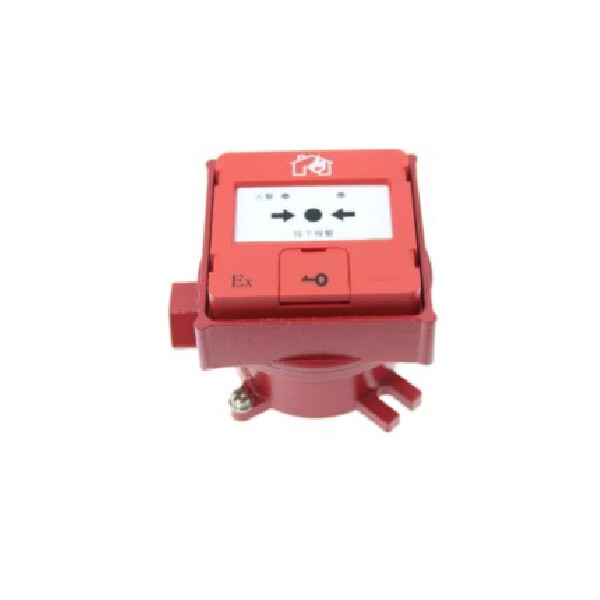
When we dive into the world of safety in hazardous environments, one term often pops up: intrinsic safety. So, what is intrinsic safety? In essence, it’s a protection technique designed to prevent ignition in explosive atmospheres by limiting the energy available for ignition. This concept is crucial for industries that operate in environments where flammable gases or dust are present, ensuring both personnel and equipment remain safe.
Defining Intrinsic Safety
At its core, intrinsic safety refers to an approach that ensures electrical equipment can’t produce enough energy to ignite a hazardous atmosphere. This means that devices are designed to operate at low power levels and incorporate various protective measures to mitigate risks. Understanding intrinsic safety is vital for industries such as oil and gas, pharmaceuticals, and mining, where the stakes are high and the potential hazards are real.
Key Principles of Intrinsic Safety
The key principles of intrinsic safety revolve around limiting energy—both thermal and electrical—so that any potential spark or heat produced cannot ignite flammable materials. The design includes barriers that restrict voltage and current flow while ensuring reliable operation under normal conditions. By adhering to these principles, organizations can confidently navigate what is meant by intrinsic safety in their operations.
Real-world Applications of Intrinsic Safety
Intrinsic safety finds its way into numerous applications across various industries. For example, in oil refineries, intrinsically safe devices like sensors and communication tools help monitor processes without posing an explosion risk. Furthermore, understanding intrinsic safety allows businesses to comply with regulations while protecting their workforce from potentially devastating accidents—demonstrating its crucial role in maintaining operational integrity.
What is Meant by Intrinsic Safety?
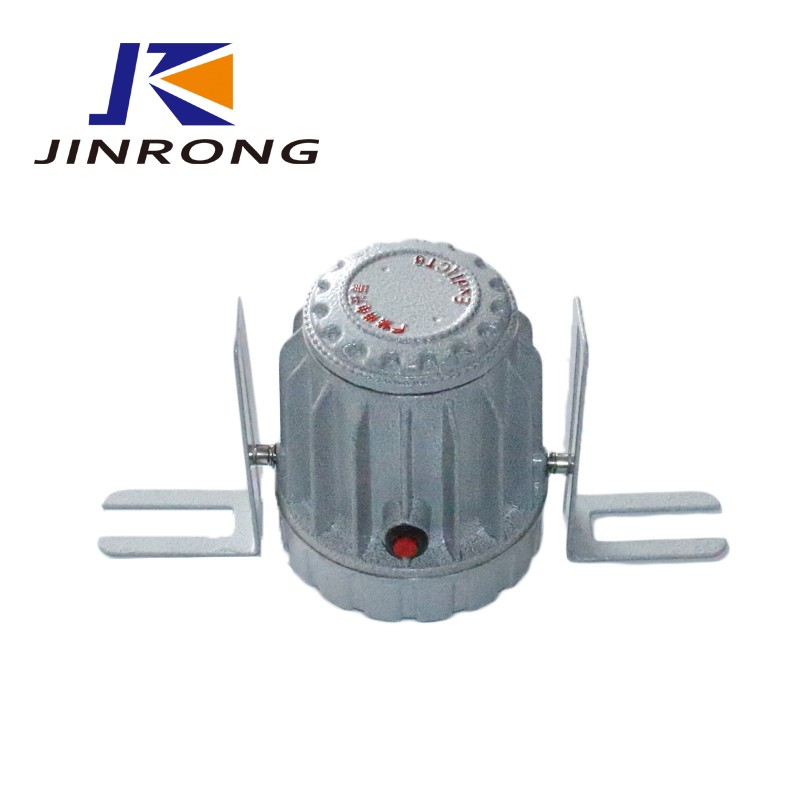
When exploring the concept of intrinsic safety, it’s essential to clarify what is meant by intrinsic safety in practical terms. This safety method focuses on preventing ignition in hazardous environments by limiting the energy available for ignition sources. By understanding intrinsic safety, industries can better protect personnel and equipment in potentially explosive atmospheres.
Common Misconceptions
One prevalent misconception about intrinsic safety is that it guarantees total protection against explosions. While it significantly reduces the risk, no system can claim absolute safety; thus, understanding intrinsic safety involves recognizing its limitations as well. Another common myth is that intrinsic safety only applies to specific industries; however, it's relevant across various sectors where flammable gases or dust are present.
Many people often confuse what is the difference between functional safety and intrinsic safety, thinking they are interchangeable concepts. In reality, functional safety encompasses a broader range of systems designed to prevent hazardous events, while intrinsic safety specifically addresses energy limitation to avoid ignition risks. Clearing up these misconceptions helps ensure that organizations implement appropriate strategies for their unique needs.
The Science Behind Intrinsic Safety
The science behind intrinsic safety revolves around controlling electrical energy within devices used in hazardous areas. By limiting voltage and current levels, devices are designed so that even under fault conditions, they cannot produce enough energy to ignite flammable materials. Understanding intrinsic safety requires knowledge of how components work together to maintain safe operating conditions in explosive environments.
Key components include barriers and isolators that effectively manage energy flow while ensuring reliable operation of equipment under various conditions. This careful design prevents overheating and sparks from occurring during normal use or unexpected faults—core principles that define what is meant by intrinsic safety in real-world applications. Emphasizing these scientific principles helps demystify how technology can coexist safely with hazardous substances.
Importance in Explosive Environments
Intrinsic safety plays a crucial role in protecting lives and property within explosive environments like oil rigs, chemical plants, or grain silos where flammable vapors or dust may be present. By adhering to strict standards for what is intrinsic safety technology, businesses can mitigate risks associated with potential ignition sources effectively. The importance of this approach cannot be overstated; it's not just about compliance but ensuring operational continuity without compromising worker health and environmental integrity.
In a world increasingly reliant on advanced technology within these high-risk settings, understanding what is the difference between extrinsic and intrinsic safety becomes vital for decision-makers seeking reliable solutions. Choosing intrinsically safe equipment means investing not only in regulatory compliance but also fostering a culture of proactive risk management within organizations operating under challenging conditions. Ultimately, prioritizing such systems enhances overall workplace security while minimizing the potential impact of accidents.
What is the Difference Between Intrinsic and Extrinsic Safety?
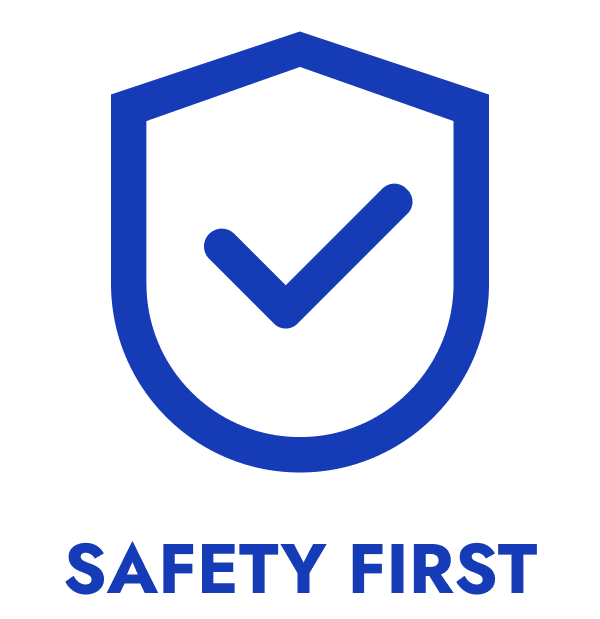
Understanding the nuances between intrinsic and extrinsic safety is crucial for industries operating in hazardous environments. While both approaches aim to mitigate risks, they do so through different methodologies. So, what is intrinsic safety? It focuses on limiting energy levels to prevent ignition, whereas extrinsic safety relies on protective barriers to isolate hazards.
Definitions and Distinctions
Intrinsic safety refers to a design approach that ensures electrical devices operate safely in potentially explosive atmospheres by limiting their energy output. Essentially, it prevents the release of sufficient energy that could ignite flammable gases or dust. On the other hand, extrinsic safety involves using protective measures such as enclosures or barriers that keep hazardous elements away from ignition sources, thus creating a safer environment.
When we ask ourselves what is meant by intrinsic safety?, we see that it emphasizes minimizing risk at the source rather than relying on external protection methods. This distinction becomes vital when evaluating which approach best suits specific operational needs.
Use Cases for Each Approach
The choice between intrinsic and extrinsic safety often depends on the application and environment in question. For instance, industries like oil and gas frequently employ intrinsic safety because it allows for greater flexibility in device placement without compromising safety standards. Conversely, extrinsic safety might be more suitable for environments where equipment can be physically isolated from hazards but still requires robust protection measures.
In scenarios requiring portability or frequent movement of equipment—think maintenance tasks—what is the difference between functional safety and intrinsic safety? Intrinsically safe devices can be moved easily without needing additional protective barriers compared to their extrinsically safe counterparts.
Benefits of Choosing Intrinsic Safety
Choosing intrinsic safety offers several advantages worth considering. First off, it simplifies compliance with regulations since intrinsically safe devices usually have built-in certifications that meet industry standards for explosive atmospheres. Furthermore, this approach reduces installation costs because there’s less need for additional protective equipment or complex barrier systems.
Another compelling reason why industries lean toward understanding intrinsic safety lies in its adaptability; intrinsically safe systems can often be integrated seamlessly into existing infrastructure without major overhauls. Finally, opting for this method fosters innovation by encouraging manufacturers to develop safer technologies while addressing evolving industry challenges.
What is the Difference Between Functional Safety and Intrinsic Safety?
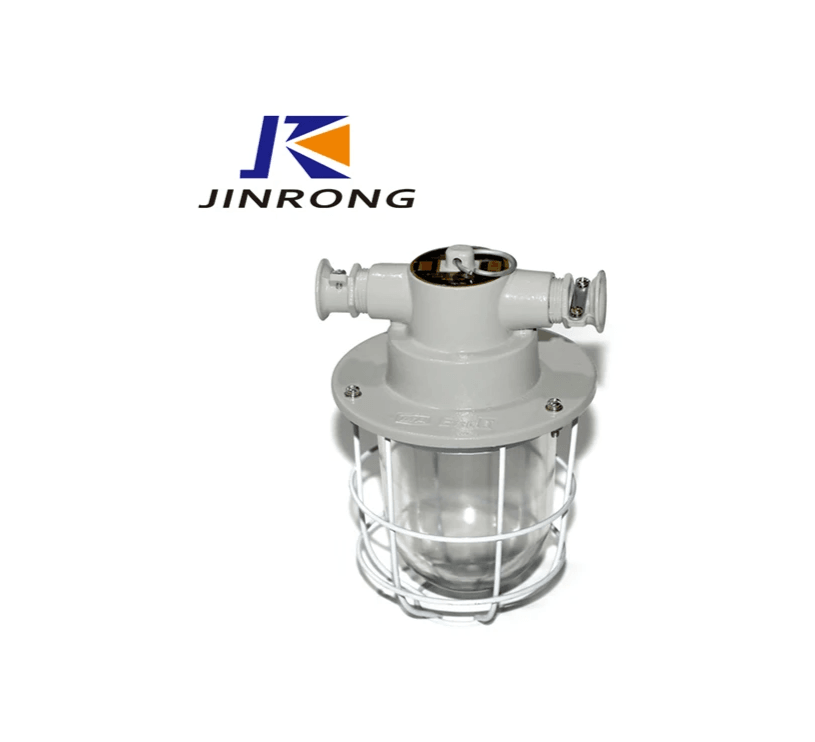
When navigating the complex world of safety protocols in hazardous environments, it's crucial to differentiate between functional safety and intrinsic safety. While both aim to prevent accidents and ensure safe operations, they do so through different mechanisms and principles. Understanding these differences can help industries choose the right approach for their specific needs.
Defining Functional Safety
Functional safety refers to a system's ability to operate correctly in response to inputs while ensuring that any potential risks are mitigated effectively. It focuses on the overall performance of safety-related systems, particularly in ensuring that failures do not lead to hazardous situations. In contrast, intrinsic safety is more about designing electrical equipment that inherently prevents ignition in explosive atmospheres, emphasizing safe operation within those environments.
Comparative Analysis
What is the difference between functional safety and intrinsic safety? The primary distinction lies in their focus: functional safety encompasses a broader range of operational integrity, while intrinsic safety specifically addresses the prevention of ignition sources in hazardous areas. Additionally, functional safety often involves complex algorithms and redundancy measures, whereas intrinsic safety relies on limiting energy levels to ensure safe operation without additional fail-safes.
Moreover, while both approaches are essential for maintaining workplace safety, they can serve different purposes depending on industry requirements. For example, industries dealing with volatile substances may prioritize intrinsic safety due to its direct impact on preventing explosions. On the other hand, sectors like automotive manufacturing may lean more towards functional safety as they focus on system reliability across various conditions.
Integrating Both Safety Approaches
Integrating both functional and intrinsic safety approaches can yield significant benefits for organizations operating in hazardous environments. By combining these methodologies, companies can create robust systems that not only prevent ignition but also ensure operational reliability under various conditions. This holistic approach not only enhances workplace security but also fosters compliance with stringent regulatory standards.
Incorporating insights from both what is meant by intrinsic safety? and what is the difference between extrinsic and intrinsic safety? helps organizations strike a balance between protecting their workforce and maintaining efficient operations. As technology advances, understanding how these two concepts complement each other will be crucial for driving innovation in hazardous area applications.
What is Intrinsic Safety vs Non-Incendive?
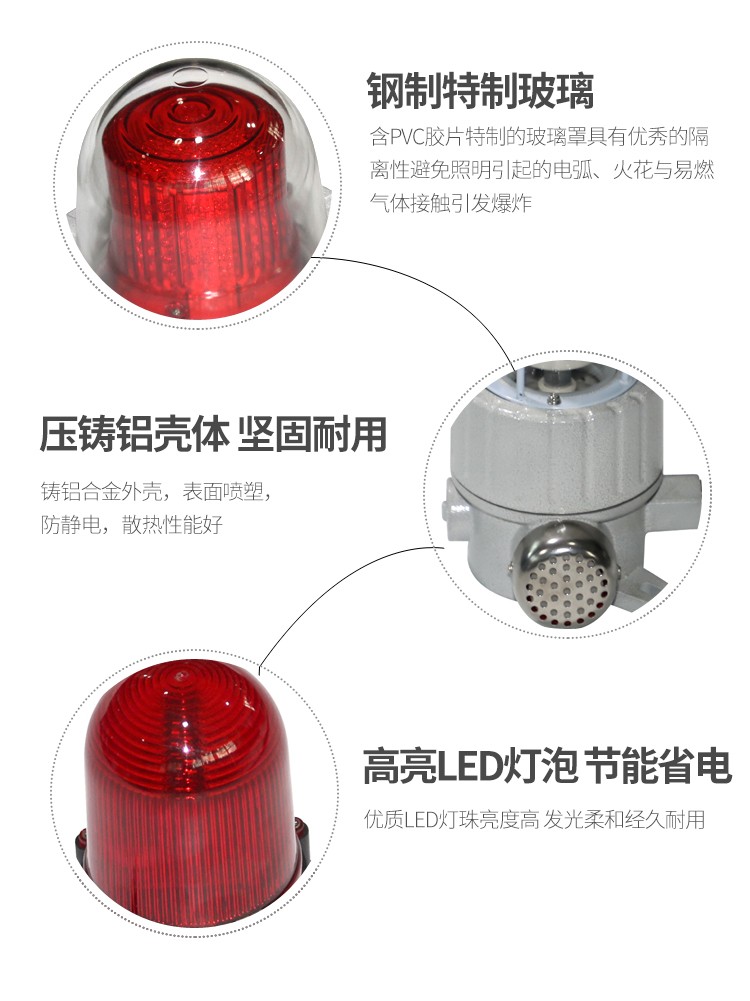
When navigating the complex world of safety in hazardous environments, understanding intrinsic safety versus non-incendive safety becomes crucial. Both concepts aim to mitigate risks associated with explosive atmospheres, but they do so through different mechanisms and standards. This section will clarify what is intrinsic safety, delve into non-incendive safety, and help you decide which approach best suits your operational needs.
Understanding Non-Incendive Safety
Non-incendive safety refers to equipment designed to operate safely in hazardous areas without generating sparks or excessive heat that could ignite flammable materials. Unlike intrinsic safety, which limits energy levels within devices to prevent ignition, non-incendive systems are built to withstand certain conditions while still allowing for a higher degree of functionality. While both approaches focus on preventing explosions, understanding non-incendive safety requires a grasp of how it differs from what is meant by intrinsic safety and its specific applications.
For instance, non-incendive equipment can be used where there are only occasional flammable gases or vapors present. This makes it suitable for environments that may not be continuously hazardous but still require some level of precaution. However, it’s essential to note that this does not mean it’s foolproof; under specific conditions, even non-incendive systems can pose risks if not properly managed.
Comparing Safety Levels
When comparing the two approaches—what is intrinsic safety versus non-incendive—the differences in their respective levels of protection become apparent. Intrinsic safety provides a higher level of assurance as it inherently reduces the energy available for ignition in any potential explosive atmosphere. In contrast, while non-incendive systems are designed with certain safeguards in mind, they do not limit energy levels as strictly as intrinsic devices do.
In practical terms, this means that while both types of equipment can be suitable for certain applications within hazardous areas, the choice between them often hinges on the specific risk assessment conducted for each environment. For industries dealing with highly volatile materials or continuous exposure to flammable substances, opting for intrinsic safety may be the more prudent choice. Conversely, less critical applications might find non-incendive solutions sufficient and more cost-effective.
Choosing the Best Strategy for Your Needs
Deciding between what is intrinsic safety and non-incendive solutions involves evaluating your unique operational requirements alongside regulatory standards such as ATEX or IECEx certifications. Factors like the nature of materials handled and frequency of exposure to hazardous conditions should heavily influence your decision-making process here. It’s vital to conduct thorough risk assessments and consult relevant guidelines before settling on either strategy.
Understanding both approaches allows industries to tailor their equipment choices based on their specific risk profiles while ensuring compliance with necessary regulations regarding what is meant by intrinsic safety and its implications in explosive environments. Ultimately, selecting between these two strategies boils down to balancing operational needs against potential hazards—an essential consideration for anyone working in high-stakes settings.
Jinrong’s Contributions to Intrinsic Safety
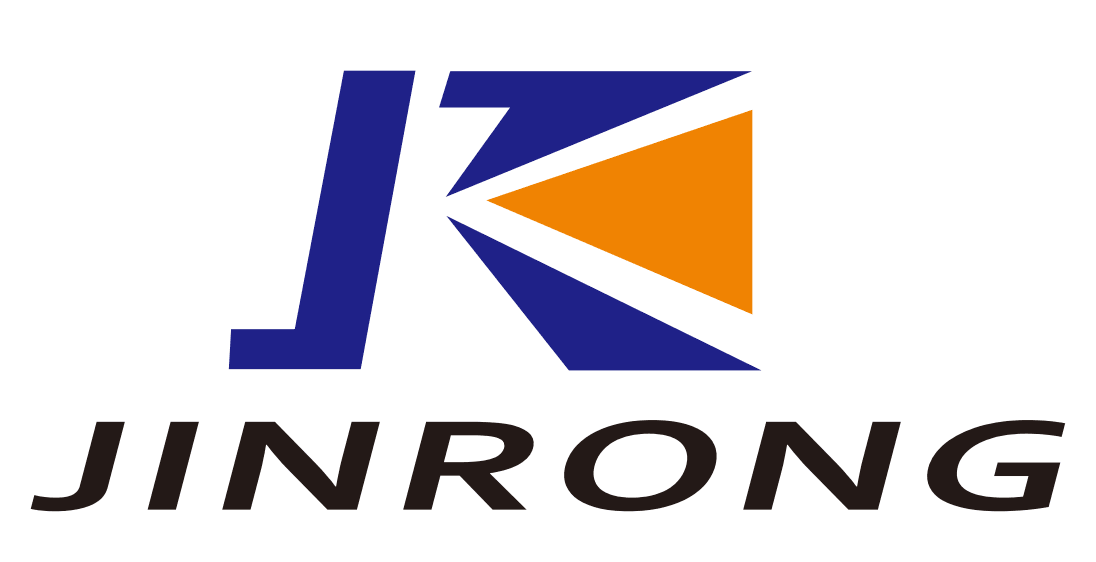
Jinrong has carved a significant niche in the realm of intrinsic safety, establishing a legacy that resonates throughout various industries. Their commitment to advancing safety standards in hazardous environments has made them a trusted name among professionals seeking reliable solutions. Understanding intrinsic safety is not just about compliance; it's about creating safer workplaces, and Jinrong leads the charge.
Overview of Jinrong's Legacy
Founded with a vision to enhance workplace safety, Jinrong has consistently pushed the boundaries of what is possible in intrinsic safety technology. Their innovations have set benchmarks that other companies aspire to reach, ensuring that what is meant by intrinsic safety becomes clear and widely understood across sectors. By prioritizing research and development, Jinrong not only adheres to existing regulations but also anticipates future needs in explosive environments.
Product Offerings in Intrinsic Safety
Jinrong's product offerings span a wide range of devices designed specifically for use in hazardous areas, showcasing their dedication to intrinsic safety principles. From advanced sensors to robust control systems, each product exemplifies the key differences between functional safety and intrinsic safety while maintaining top-tier performance standards. This diverse portfolio ensures that industries can find tailored solutions that meet their unique requirements—whether they are looking for answers regarding what is intrinsic safety or how it compares with non-incendive systems.
Partnering with Distributors Effectively
To amplify their impact on intrinsic safety technologies, Jinrong places great emphasis on building effective partnerships with distributors worldwide. This strategic approach allows them to extend their reach while educating partners on critical distinctions such as what is the difference between intrinsic and extrinsic safety? Through these collaborations, they ensure that knowledge about best practices permeates the market, empowering end-users to make informed decisions based on solid understanding of both intrinsic and non-incendive strategies.
Conclusion
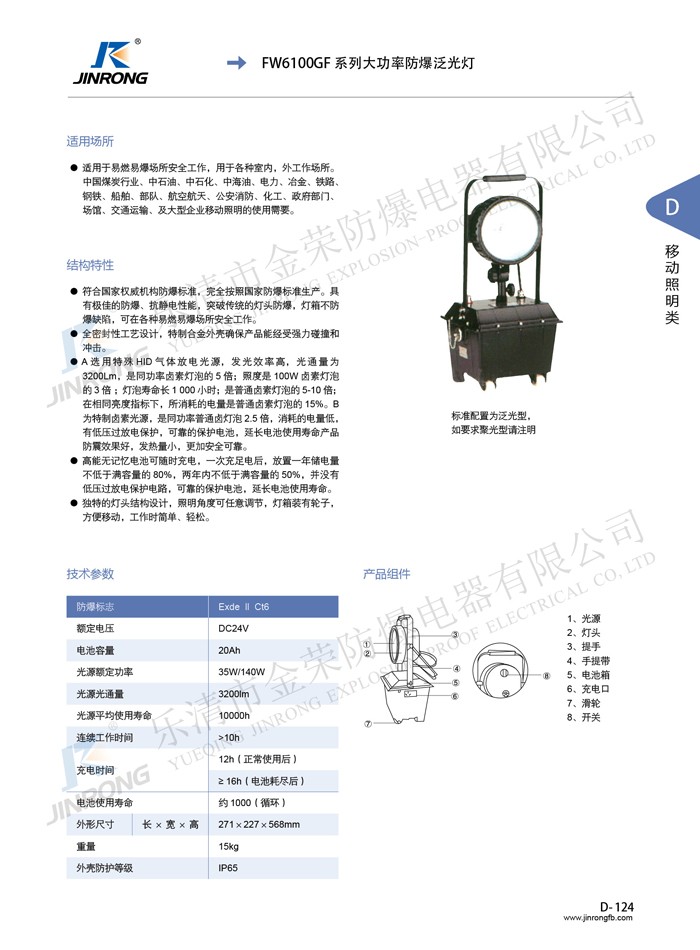
In wrapping up our exploration of intrinsic safety, it’s clear that this concept is not just a safety measure but a critical aspect of operational integrity in hazardous environments. Understanding intrinsic safety allows industries to operate effectively while minimizing risks associated with explosive atmospheres. As we look ahead, the future of intrinsic safety technologies promises even greater advancements, ensuring that businesses can navigate the complexities of safety regulations and environmental challenges.
The Future of Intrinsic Safety Technologies
The landscape of what is intrinsic safety is continually evolving with technological advancements and increased regulatory demands. Future innovations will likely focus on enhancing communication technologies and integrating smart devices into hazardous areas while maintaining stringent safety standards. As industries embrace digital transformation, understanding intrinsic safety will become even more crucial for ensuring safe operations.
Importance of Compliance and Certification
Compliance with industry standards is vital when discussing what is meant by intrinsic safety. Adhering to regulations not only protects workers but also safeguards equipment investments and prevents costly downtime. Certification processes play a key role in validating that products meet the necessary criteria for use in potentially explosive environments, emphasizing the importance of understanding both functional safety and intrinsic safety.
Driving Innovation in Hazardous Area Safety
Innovation in hazardous area safety hinges on understanding the differences between various approaches, such as what is the difference between intrinsic and extrinsic safety? By leveraging cutting-edge technology alongside traditional methods, companies can create safer work environments while maximizing efficiency. Ultimately, driving innovation involves a commitment to continuous improvement, ensuring that both functional and intrinsic safety principles are integrated seamlessly into everyday operations.