Introduction
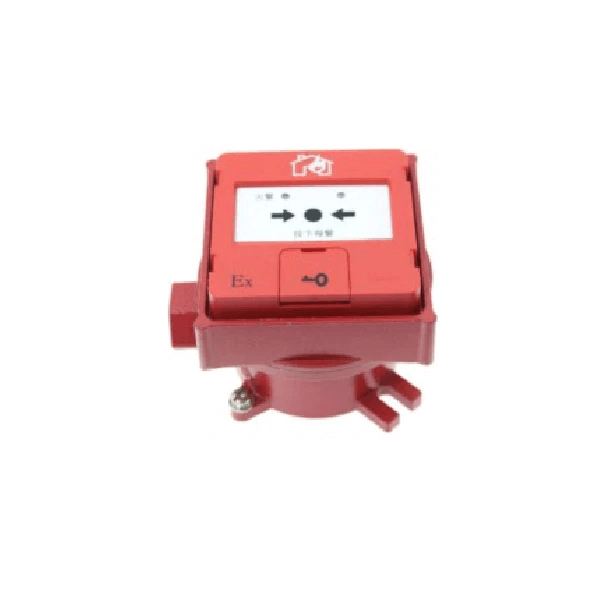
In an era where technology meets the challenges of hazardous environments, understanding intrinsic safety is not just beneficial but essential. Intrinsic safety refers to a design approach that ensures electrical equipment operates safely in potentially explosive atmospheres by limiting energy levels. This principle is vital for industries where hazardous electrical conditions can lead to catastrophic incidents, making it a cornerstone of modern electrical safety standards.
Understanding Intrinsic Safety in Depth
At its core, intrinsic safety means creating devices that are incapable of igniting flammable gases or dust under normal and fault conditions. This is achieved through various engineering techniques that restrict the amount of energy available in the device, ensuring it remains safe even when exposed to volatile environments. The intrinsically safe meaning extends beyond mere compliance; it embodies a commitment to protecting lives and property in challenging operational contexts.
Importance of Electrical Safety Standards
Electrical safety standards serve as the backbone for ensuring equipment operates safely and reliably, particularly in hazardous settings. Adhering to these standards not only protects workers but also minimizes risks associated with electrical failures and explosions. Moreover, achieving ATEX certification—an important milestone for intrinsically safe devices—demonstrates a manufacturer’s dedication to meeting rigorous electrical safety requirements.
Applications in Hazardous Environments
The applications of intrinsic safety are widespread across various industries such as oil and gas, mining, pharmaceuticals, and chemical manufacturing. In these sectors, using intrinsically safe equipment like ex proof junction boxes can significantly reduce the risk of ignition from sparks or heat generated by electrical devices. By employing ATEX-approved products designed for hazardous locations, companies can ensure their operations remain both efficient and secure while navigating the complexities of dangerous work environments.
What is Intrinsic Safety?
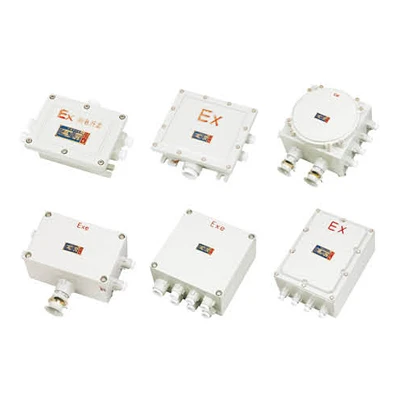
Intrinsic safety is a crucial concept in the realm of electrical safety, particularly when dealing with hazardous environments. It refers to a method of designing and constructing electrical equipment to prevent ignition of flammable gases or dust by limiting the energy available for sparks or hot surfaces. This approach ensures that even in the presence of explosive atmospheres, such as oil rigs or chemical plants, the risk of fire or explosion is minimized.
Definition and Principles of Intrinsic Safety
At its core, intrinsic safety revolves around two main principles: energy limitation and fault tolerance. The intrinsic safety meaning becomes clearer when we consider that devices designed under this principle cannot produce enough energy to ignite a hazardous substance, regardless of fault conditions. By using barriers like an Ex proof junction box and adhering to stringent ATEX certification requirements, manufacturers ensure that their products are safe for use in potentially explosive environments.
The essential idea is that any electrical device operating in hazardous areas must not only function reliably but also do so without posing a risk to personnel or property. This balance between operational efficiency and safety forms the bedrock upon which intrinsic safety standards are built. Thus, understanding these principles is vital for anyone involved in selecting or utilizing intrinsically safe equipment.
Differentiating Intrinsically Safe Devices
First off, intrinsically safe devices are specifically designed with built-in protections against ignition sources—this means they often utilize lower voltage and current levels compared to standard electrical appliances. Additionally, these devices typically have ATEX approval stamped on them, indicating they meet rigorous European standards for operation in explosive atmospheres.
Another critical aspect is how these devices manage energy flow; they often incorporate features such as fuses and isolation barriers to ensure that even if a malfunction occurs, there’s no chance for an ignition source to develop. This differentiation makes it imperative for industries operating in hazardous environments to invest only in certified intrinsically safe equipment—after all, lives depend on it! Understanding these distinctions not only enhances workplace safety but also aids organizations in compliance with applicable regulations.
Understanding Intrinsic Safety in Real-World Applications
In real-world applications, intrinsic safety plays a pivotal role across various industries—from oil and gas extraction to pharmaceuticals manufacturing. For instance, when workers operate handheld instruments within volatile atmospheres like refineries or chemical plants, relying on intrinsically safe tools mitigates risks associated with sparks igniting flammable substances. The implementation of Ex proof junction boxes further ensures that wiring remains secure while maintaining compliance with ATEX certification requirements.
Moreover, many companies now prioritize training their staff on the importance of recognizing and using intrinsically safe devices correctly; after all, knowledge empowers safer practices! By integrating this understanding into daily operations—whether through regular audits or employee workshops—organizations can foster a culture centered around electrical safety while maximizing productivity amidst potential hazards.
Ultimately, comprehending how intrinsic safety manifests across diverse applications can lead businesses toward more informed decisions about their equipment choices while ensuring adherence to strict industry standards.
The Science Behind Intrinsic Safety
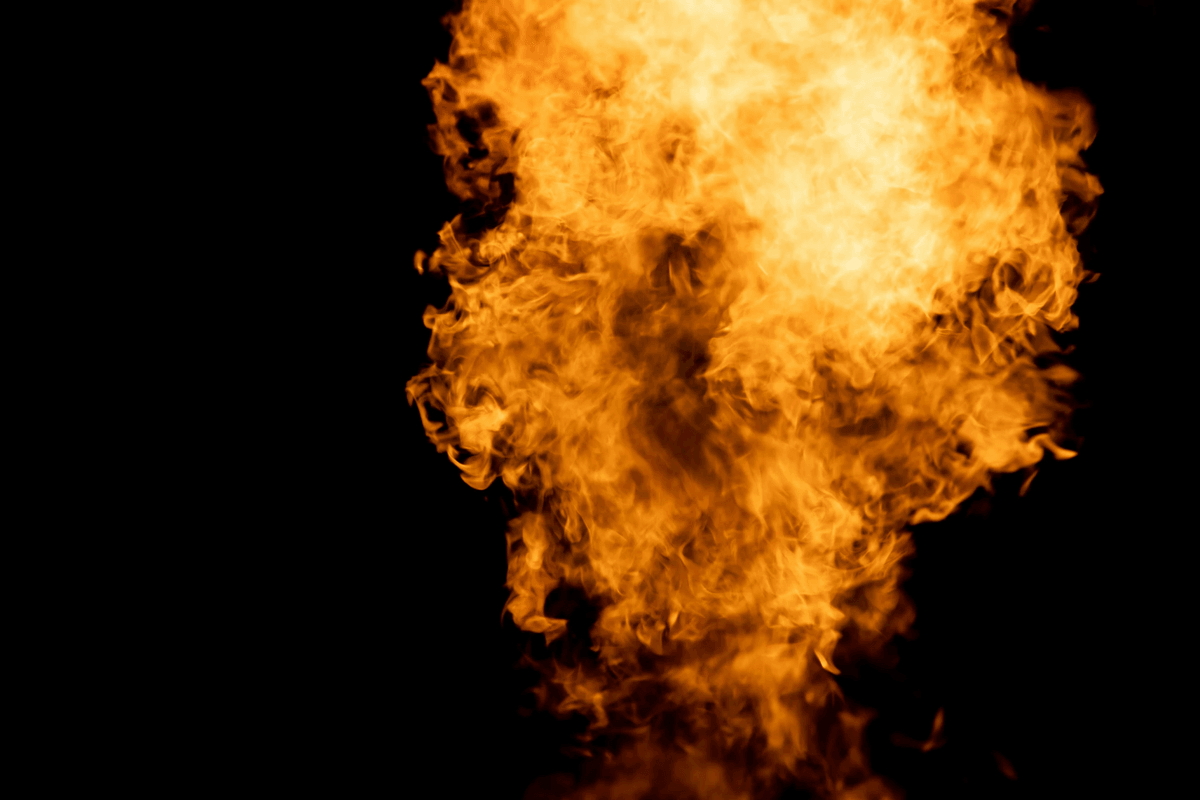
When we dive into the science of intrinsic safety, we're really talking about how to keep electrical systems safe in hazardous environments. This involves a blend of engineering principles and safety standards designed to prevent explosions and other dangerous incidents. Understanding these concepts is crucial for anyone working with intrinsically safe devices, especially in industries where electrical safety is paramount.
Key Concepts in Electrical Safety
At the heart of electrical safety lies the concept of limiting energy—this is where intrinsic safety shines. By ensuring that devices do not produce enough energy to ignite flammable atmospheres, engineers can create systems that are both functional and safe. This principle is foundational for any intrinsically safe equipment, including ex proof junction boxes which are specifically designed to contain potential hazards.
Another key concept is fault tolerance, which refers to a system’s ability to continue operating safely even when something goes wrong. In the context of intrinsic safety, this means designing circuits that can handle faults without leading to catastrophic failures or explosions. Understanding these principles helps organizations comply with ATEX certification requirements and ensures that their operations remain secure.
Lastly, proper grounding and insulation techniques also play vital roles in maintaining electrical safety. These practices help mitigate risks associated with short circuits or overloads that could lead to dangerous situations in hazardous environments. By integrating these concepts into their designs, manufacturers ensure that their intrinsically safe devices perform reliably under adverse conditions.
Energy Limitation and Fault Tolerance
Energy limitation is one of the cornerstones of intrinsic safety; it involves restricting the amount of energy available for ignition sources within an explosive atmosphere. This means designing equipment so that even if a fault occurs, it cannot generate enough heat or spark to ignite flammable gases or dust present in hazardous locations. Such meticulous attention to detail ensures compliance with ATEX approval standards while enhancing overall operational safety.
Fault tolerance complements energy limitation by ensuring that systems remain operational even when unexpected issues arise. For instance, if there’s a failure within an intrinsically safe device, its design should allow it to fail safely without causing harm or igniting nearby combustible materials. This dual approach significantly reduces risks associated with hazardous electrical environments where traditional equipment might falter.
The effectiveness of these principles can be seen through rigorous testing procedures required for ATEX certification processes which assess how well devices perform under various fault scenarios. Manufacturers must demonstrate compliance through extensive evaluations before gaining approval for their products as intrinsically safe solutions—an essential step towards achieving reliable electrical safety in high-risk areas.
Real-World Examples of Intrinsic Safety in Action
Real-world applications of intrinsic safety highlight its importance across various industries such as oil and gas, pharmaceuticals, and chemical processing—where hazardous materials abound! For instance, using intrinsically safe sensors within oil rigs allows operators to monitor conditions without risking ignition from volatile substances present nearby; this showcases how critical proper design is for maintaining operational integrity.
Another compelling example involves ex proof junction boxes used in explosive atmospheres found at petrochemical plants; these robust enclosures protect sensitive wiring from external hazards while ensuring any internal faults don’t lead to catastrophic failures outside the box itself! Such implementations reinforce how adhering strictly to ATEX certification guidelines not only enhances equipment reliability but also safeguards workers’ lives daily.
Additionally, consider mobile communication devices designed specifically for use within hazardous zones—they incorporate intrinsic safety features like limited power outputs and robust casings tailored against environmental threats! These innovations demonstrate ongoing advancements toward creating safer workplaces while allowing essential communications amidst potentially dangerous settings—a perfect marriage between technology and security through effective application of intrinsic safety principles.
ATEX Certification Explained
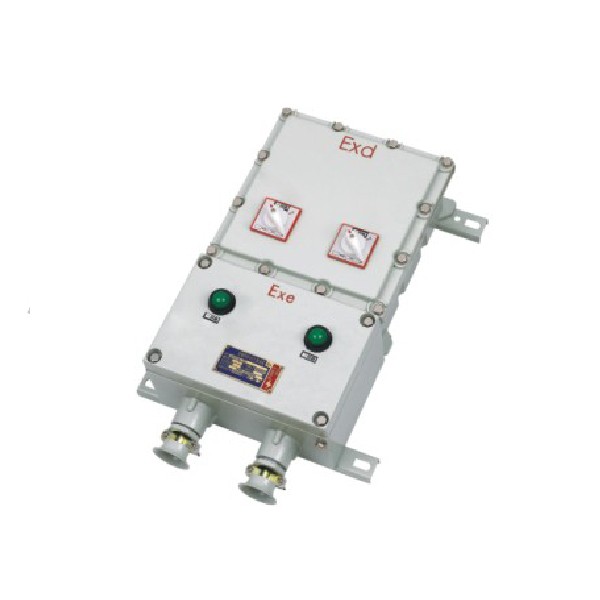
What is ATEX Approval?
ATEX approval refers to the compliance of equipment with European Union directives regarding products intended for use in explosive atmospheres. Specifically, it ensures that devices meet stringent standards for intrinsic safety, thus minimizing the risk of ignition from electrical sources. In essence, obtaining ATEX certification means that a product has been rigorously tested and deemed safe for use in hazardous electrical environments.
Importance of Meeting ATEX Standards
Meeting ATEX standards is not just a legal requirement but also a moral obligation to protect workers' lives and property in hazardous settings. Non-compliance can lead to catastrophic accidents, including explosions or fires that could endanger lives and result in significant financial losses. Therefore, ensuring that all intrinsically safe equipment adheres to these standards is vital for maintaining high levels of electrical safety across industries like oil and gas, mining, and chemical manufacturing.
How ATEX Certification Enhances Safety
ATEX certification enhances safety by establishing rigorous testing protocols and guidelines that intrinsically safe devices must adhere to before they can be deployed in hazardous areas. This process helps identify potential risks associated with faulty or improperly designed equipment, ultimately leading to safer operational practices. By utilizing certified ex proof junction boxes and other intrinsically safe gear, companies can significantly reduce the likelihood of accidents while fostering a culture of safety within their organizations.
Choosing Intrinsically Safe Equipment
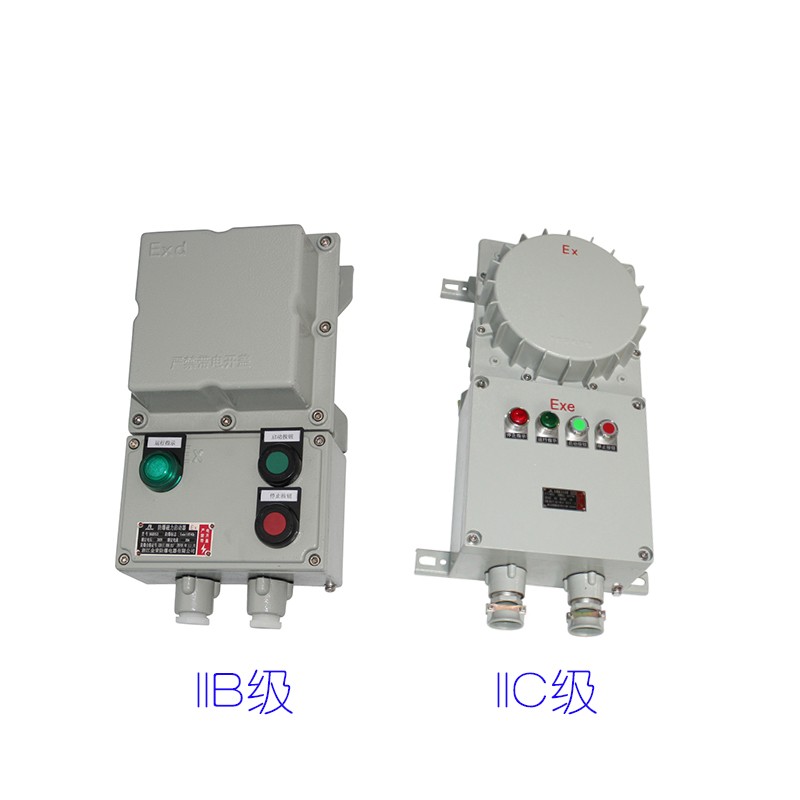
When it comes to selecting intrinsically safe equipment, understanding the nuances of electrical safety is paramount. The right choice can mean the difference between a secure work environment and a hazardous one. As such, knowing what features to look for and how to evaluate options like an ex proof junction box can significantly enhance safety in potentially dangerous settings.
Key Features of Intrinsically Safe Devices
Intrinsically safe devices are designed with unique features that ensure they operate safely in hazardous electrical environments. One key attribute is energy limitation; these devices restrict the amount of electrical energy that can be released, thus preventing ignition sources in flammable atmospheres. Additionally, robust construction and compliance with ATEX certification standards are crucial, as they guarantee that the equipment has been rigorously tested for safety in explosive environments.
Another important feature is fault tolerance; intrinsically safe devices must continue operating safely even when faults occur. This includes having built-in protective measures such as fuses or circuit breakers that prevent excessive current flow. Lastly, clear labeling and documentation regarding ATEX approval help users understand how to operate these devices correctly and safely.
Evaluating Ex Proof Junction Box Options
When considering ex proof junction boxes for your applications, it’s essential to assess their compliance with intrinsic safety standards. Look for products that explicitly state their ATEX certification status; this ensures they meet stringent requirements for use in explosive atmospheres. Furthermore, consider factors like ingress protection (IP) ratings which indicate how well the box can withstand dust and moisture—critical elements when dealing with hazardous electrical environments.
Another evaluation criterion should be material durability; ex proof junction boxes made from high-quality materials are more likely to endure harsh conditions without compromising safety. Be sure to check whether the design allows for easy installation and maintenance while still adhering to intrinsic safety principles. Finally, user reviews or case studies can provide valuable insights into real-world performance, helping you make an informed decision.
Recommended Brands for Intrinsically Safe Gear
There are several reputable brands known for producing high-quality intrinsically safe equipment that meets rigorous electrical safety standards. Companies like Pepperl+Fuchs offer a range of intrinsically safe devices recognized globally for their reliability and innovation in hazardous environments. Their products often come highly recommended due to their extensive experience in developing solutions tailored specifically for industries requiring ATEX approval.
Another notable brand is R.STAHL, which specializes in explosion protection technology including advanced ex proof junction boxes suitable for various applications. Their commitment to quality assurance ensures that all products comply with international safety regulations while providing exceptional performance under challenging conditions. Lastly, you might want to explore offerings from Extronics; they are known for their cutting-edge designs focused on both functionality and user-friendliness while maintaining intrinsic safety principles.
The Role of Jinrong in Intrinsic Safety
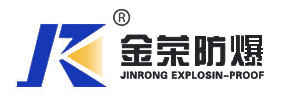
When it comes to intrinsic safety, Jinrong stands as a beacon of expertise and innovation. With years of experience in the electrical safety sector, Jinrong has carved out a niche for itself by focusing on creating solutions that meet stringent standards for hazardous electrical environments. Their commitment to quality ensures that all products not only comply with ATEX certification but also enhance overall safety in various applications.
Overview of Jinrong's Expertise
Jinrong's expertise lies in understanding the intricate balance between functionality and safety within hazardous environments. Their team is well-versed in the principles of intrinsically safe design, ensuring that every product minimizes risk while maximizing efficiency. This deep knowledge translates into innovative solutions that are tailored for industries where electrical safety is non-negotiable.
Jinrong's Product Range in Ex-Proof Equipment
Jinrong offers an impressive array of ex-proof equipment designed specifically for use in hazardous areas. Their product range includes state-of-the-art intrinsically safe devices, such as ex proof junction boxes and other essential components that adhere to ATEX approval standards. By prioritizing energy limitation and fault tolerance, these products ensure optimal performance without compromising on intrinsic safety.
Success Stories from Jinrong's Distribution
The impact of Jinrong’s products can be seen through numerous success stories across various industries. For instance, several oil and gas companies have reported significant improvements in operational safety after integrating Jinrong’s intrinsically safe equipment into their processes. These successes highlight how effective implementation of electrical safety standards can lead to safer working conditions while maintaining productivity.
Conclusion
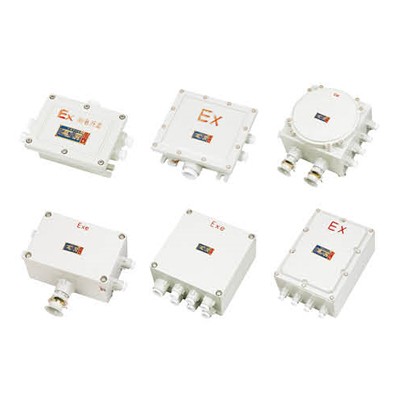
In conclusion, the realm of intrinsic safety is not just a set of standards; it's a vital commitment to protecting lives and property in hazardous electrical environments. As technology evolves, so too do the innovations surrounding intrinsically safe devices, ensuring that they remain effective against increasingly complex challenges. By understanding and implementing these standards, industries can navigate risks with confidence while enhancing overall electrical safety.
The Future of Intrinsic Safety Innovations
The future of intrinsic safety innovations is poised to be exciting and transformative, with advancements in technology paving the way for smarter solutions. Emerging trends include the integration of IoT devices into intrinsically safe systems, allowing for real-time monitoring and improved fault detection in hazardous environments. As industries continue to prioritize safety, we can expect to see more robust designs and enhanced ATEX certification processes that will further ensure compliance with stringent electrical safety standards.
Key Takeaways on Electrical Safety Standards
Understanding the intricacies of electrical safety standards is crucial for anyone working in or around hazardous environments. Intrinsic safety principles not only protect equipment but also safeguard personnel by preventing ignition sources in explosive atmospheres. Remember that ATEX approval is essential when selecting intrinsically safe devices; it signifies that products meet rigorous requirements designed to minimize risk in potentially dangerous settings.
How to Implement Intrinsic Safety Solutions
Implementing intrinsic safety solutions begins with a thorough assessment of your operational environment and identifying potential hazards associated with electrical equipment use. Selecting appropriate intrinsically safe devices—such as ex proof junction boxes—is critical; ensure they are backed by ATEX certification for maximum reliability and performance. Finally, continuous training and awareness programs for employees about intrinsic safety practices will solidify a culture focused on maintaining high electrical safety standards.