Introduction
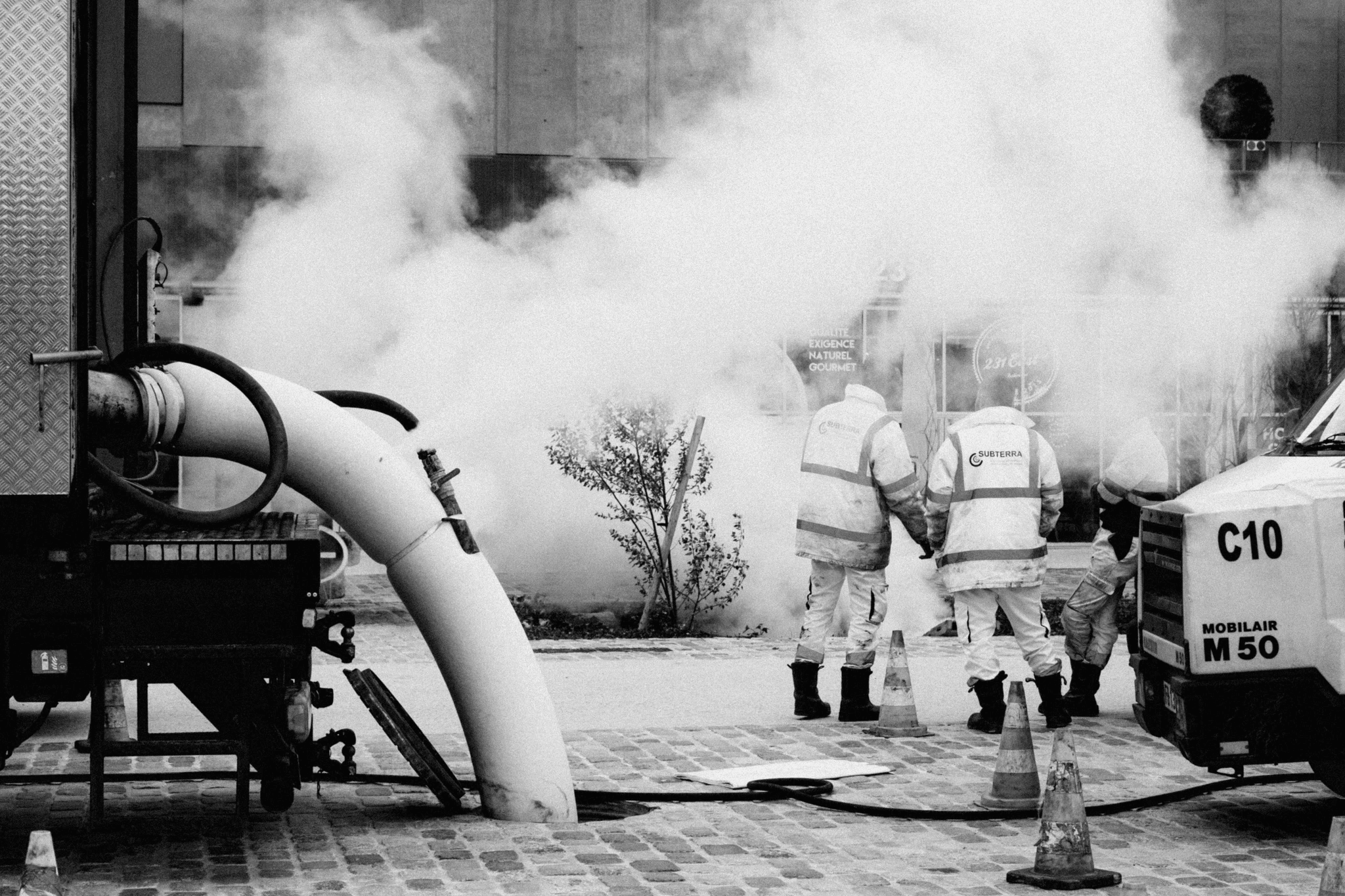
In today's industrial landscape, understanding ATEX zone classification is paramount to ensuring safety in environments where explosive atmospheres may occur. The correct classification of these zones not only protects workers but also minimizes risks to equipment and infrastructure. By grasping the fundamentals of what an ATEX zone is, businesses can implement effective strategies to mitigate hazards and comply with essential regulations.
Understanding the Importance of ATEX Zone Classification
ATEX zone classification serves as a critical framework for identifying hazardous areas within industrial settings. It categorizes locations based on the likelihood of explosive atmospheres forming, thus guiding safety measures and operational protocols. Properly executed classification reduces the potential for accidents and ensures that appropriate protective measures are taken, making it indispensable for any organization handling flammable materials.
The Role of Safety Experts in ATEX Compliance
Safety experts play a vital role in navigating the complexities of ATEX compliance by applying their knowledge to accurately classify areas at risk for explosive atmospheres. They are instrumental in conducting thorough assessments to identify locations where an ATEX may form and recommend necessary precautions tailored to each unique environment. Their expertise ensures that organizations adhere to both local and international standards, fostering a culture of safety across all operations.
Overview of ATEX Regulations and Guidelines
ATEX regulations provide a comprehensive legal framework that governs how industries should manage risks associated with explosive atmospheres. These guidelines outline essential compliance steps that businesses must follow, including how to demarcate ATEX zones effectively and classify areas based on specific hazards like gas or dust. By familiarizing themselves with these regulations, organizations can enhance their safety protocols while minimizing liability and operational disruptions.
What is an ATEX Zone?
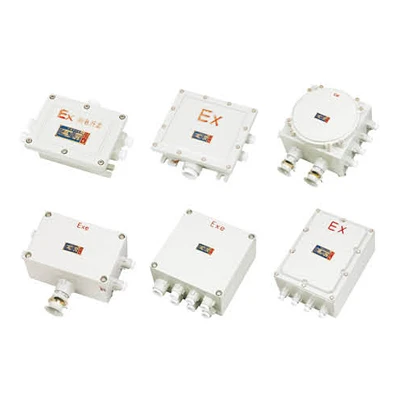
Understanding what constitutes an ATEX zone is crucial for ensuring safety in environments where explosive atmospheres may exist. The term ATEX stems from the French phrase ATmosphères EXplosibles, which refers to the regulations governing such hazardous areas. By properly classifying these zones, businesses can implement effective safety measures and comply with ATEX regulations.
Defining Hazardous Areas in Industry
Hazardous areas are locations where flammable gases, vapors, or dust may form and pose a risk of explosion or fire. These areas are not just limited to oil rigs or chemical plants; they can be found in various industries including food processing, pharmaceuticals, and waste management. Understanding how to demarcate ATEX zones helps organizations identify locations where an ATEX may form, enabling them to take necessary precautions.
Key Characteristics of ATEX Zones
ATEX zones are defined by specific characteristics that help determine the level of risk associated with each area. The primary factors include the type of hazardous material present—whether gas or dust—and its likelihood of occurrence over time. Additionally, the duration and frequency of exposure play a significant role in classifying these zones under ATEX zone classification guidelines.
Types of ATEX Zones Explained
There are two main types of ATEX zones: those classified for gases (Zone 0, Zone 1, and Zone 2) and those designated for dust (Zone 20, Zone 21, and Zone 22). Each zone has its own criteria based on the probability of explosive atmospheres forming; for example, Zone 0 indicates a continuous presence of flammable gas while Zone 2 suggests it’s only present occasionally. Understanding these classifications is essential for implementing proper safety measures and compliance with relevant ATEX regulations.
How to Demarcate ATEX Zones?
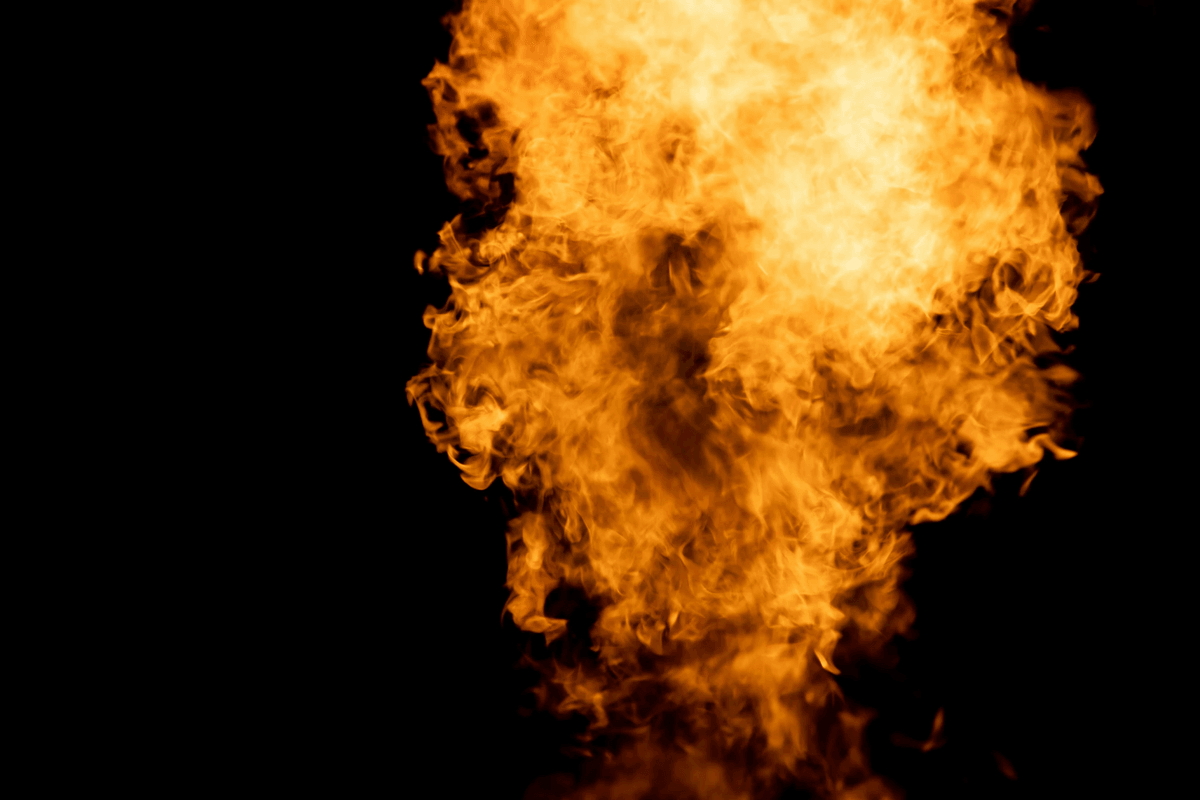
Demarcating ATEX zones is crucial for ensuring safety in environments where explosive atmospheres may occur. Understanding how to demarcate ATEX zones involves a systematic approach that includes classification, risk assessment, and compliance with ATEX regulations. This section will guide you through the essential steps and tools required for effective zone identification.
Step-by-Step Guide to Classification
To begin with ATEX zone classification, the first step is conducting a thorough risk assessment of the area in question. This involves identifying potential sources of ignition and understanding the types of materials present that could lead to an explosive atmosphere. After gathering this information, you can classify areas based on their specific characteristics—determining whether they fall into Zone 0, Zone 1, Zone 2 for gas or Zone 20, Zone 21, or Zone 22 for dust.
Next, it’s vital to document your findings meticulously; this documentation serves as a reference point for ongoing safety measures and compliance with ATEX regulations. The classification should be reviewed regularly or whenever there are changes in processes or materials that might affect the zone status. Finally, ensure that all personnel are trained on what an ATEX zone is and understand their roles in maintaining safety within these classified areas.
Tools and Techniques for Zone Demarcation
When considering how to demarcate ATEX zones effectively, several tools and techniques come into play. For instance, using gas detection equipment can help identify hazardous concentrations of flammable gases or vapors before they become problematic. Additionally, employing thermal imaging cameras can assist in spotting hot spots where dust accumulation might ignite under certain conditions.
Another effective technique is utilizing software designed specifically for hazard analysis; these programs can model potential explosive atmospheres based on various parameters such as material properties and environmental factors. Moreover, physical barriers like signage or colored markings can visually indicate the boundaries of each classified area—making it easier for workers to recognize where special precautions must be taken regarding safety protocols.
Common Challenges in Zone Identification
Identifying locations where an ATEX may form often presents numerous challenges that require careful consideration during the classification process. One common issue is insufficient data about material properties; if you don’t fully understand what substances are present and their behavior under different conditions, accurate classification becomes nearly impossible. Furthermore, evolving processes within industries may lead to changes in hazards that necessitate re-evaluation of existing classifications.
Another challenge lies in ensuring consistency among team members involved in zone identification; miscommunication can lead to discrepancies in how areas are classified or managed over time—potentially putting lives at risk if not addressed properly. Lastly, keeping up-to-date with ever-evolving ATEX regulations adds another layer of complexity; businesses must stay informed about any legislative changes that impact their operations related to hazardous zones.
Classification of Areas: A Deeper Dive
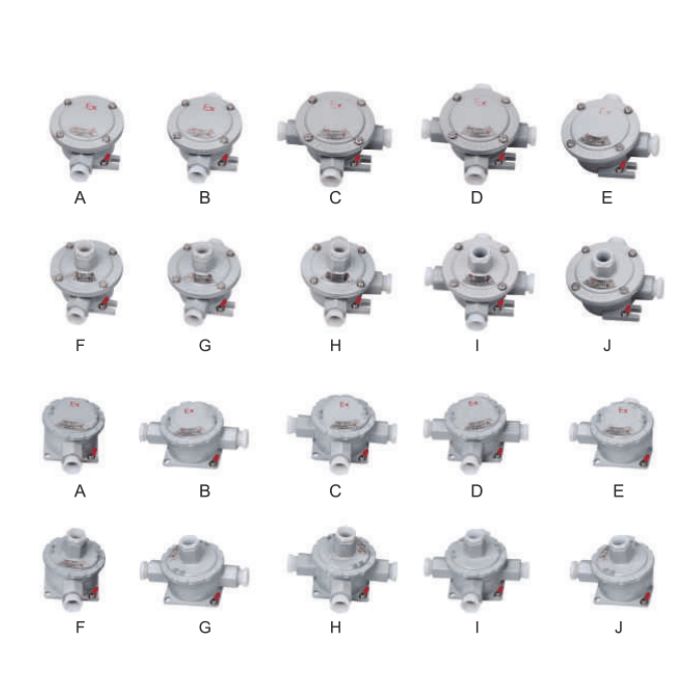
When it comes to ATEX zone classification, understanding how to differentiate between gas and dust environments is crucial. The classification process helps identify locations where an ATEX may form, ensuring that safety measures are adequately implemented. This section delves into the nuances of classifying areas based on the types of hazardous materials present.
Classifying Areas Based on Gas and Dust
Classifying areas based on gas and dust is a fundamental aspect of ATEX regulations. Gas zones are typically categorized into three classes: Zone 0, Zone 1, and Zone 2, depending on the frequency and duration of the presence of flammable gases or vapors. Dust zones follow a similar pattern with Zone 20, Zone 21, and Zone 22 classifications that indicate varying levels of risk associated with combustible dust in the atmosphere.
To successfully classify these areas, one must consider factors such as the type of material involved and its propensity to ignite under specific conditions. For instance, certain gases may only be present during maintenance activities while others might continuously linger in a production area—this distinction is vital for proper ATEX zone classification. Understanding these differences not only aids in compliance but also enhances overall workplace safety by identifying potential hazards before they escalate.
Importance of Material Properties in Classification
The properties of materials play an essential role in the classification of areas within ATEX regulations. Each material has distinct characteristics—such as ignition temperature, volatility, and particle size—that influence how it behaves in various environments. By thoroughly analyzing these properties, safety experts can more accurately determine which locations are at risk for forming an ATEX zone.
For example, a highly volatile gas like acetylene poses a greater threat than less volatile substances when assessing potential hazards in confined spaces or poorly ventilated areas. Additionally, understanding dust properties like particle size can help identify locations where an ATEX may form due to accumulation or dispersion during operational processes. Thus, material properties not only inform effective classification but also guide appropriate precautionary measures tailored to specific risks.
Real-World Examples of Area Classifications
Real-world examples provide valuable insights into how effective ATEX zone classification operates across various industries. In chemical manufacturing plants where flammable gases are prevalent during production processes, you might find Zones 0 or 1 classified around storage tanks or reactors—areas that require stringent safety protocols due to their high-risk nature. Conversely, warehouses storing non-volatile materials may fall under lower-risk classifications like Zone 2.
Another illustrative case can be found within food processing facilities where flour dust can create explosive atmospheres if not properly managed; here you would see Zones 20 or 21 established near milling operations or packaging lines that handle bulk powders regularly. These examples underscore not only the importance but also the practicality behind understanding how to demarcate ATEX zones effectively—ensuring compliance with regulations while fostering a safer working environment for all employees involved.
Identifying Locations Where an ATEX May Form
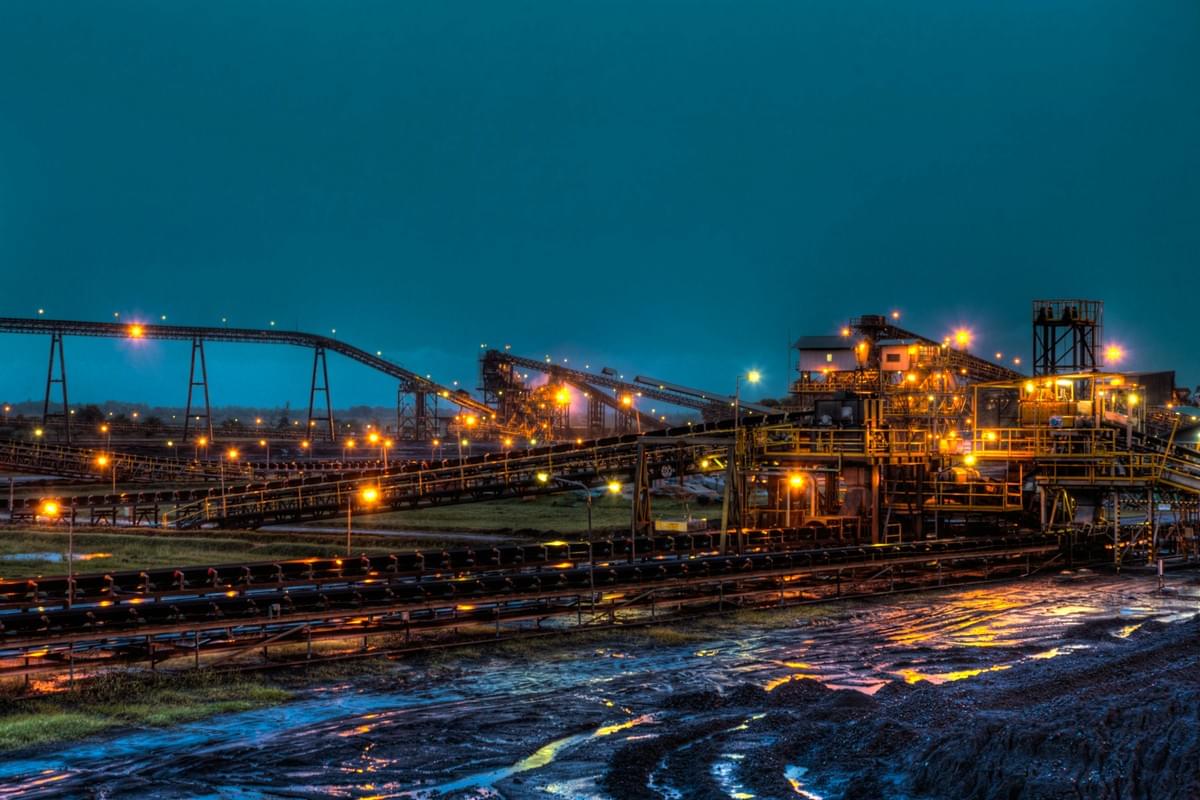
Identifying locations where an ATEX may form is crucial for any industry handling flammable materials. Understanding the common hazards triggering ATEX zones is the first step in ensuring workplace safety and compliance with ATEX regulations. By recognizing these hazards, businesses can better prepare and implement effective strategies to mitigate risks associated with explosive atmospheres.
Common Hazards Triggering ATEX Zones
Common hazards that trigger ATEX zones include flammable gases, vapors, and dust particles, which can ignite under certain conditions. Industries such as oil and gas, chemical manufacturing, and food processing are particularly susceptible to these hazardous conditions due to the nature of their operations. Additionally, equipment failures or improper handling of materials can lead to the formation of explosive atmospheres that necessitate a thorough understanding of ATEX zone classification.
When assessing potential hazards, it’s essential to consider both the frequency and duration of exposure to these dangerous substances. For instance, areas where volatile organic compounds (VOCs) are present may frequently fall under specific classifications within the ATEX framework. Identifying these common hazards allows safety experts to determine how to demarcate ATEX zones effectively while ensuring compliance with existing regulations.
Conducting a Risk Assessment for ATEX
Conducting a risk assessment for ATEX involves evaluating potential sources of ignition along with identifying locations where an ATEX may form due to the presence of hazardous materials. This assessment should include a detailed analysis of processes, equipment used in operations, and environmental factors that could contribute to explosive atmospheres. Safety experts must also engage employees in this process since they often have invaluable insights into daily operational risks.
Once potential hazards have been identified through risk assessments, businesses can prioritize actions based on severity and likelihood of occurrence related to different types of materials involved—be it gas or dust-based substances. The results from these assessments will inform decisions on necessary control measures such as ventilation systems or explosion-proof equipment tailored specifically for each classified area. Understanding how classification of areas influences risk management is fundamental in maintaining safety standards within industrial environments.
Case Studies: Identifying ATEX Locations
Case studies serve as excellent learning tools when identifying locations where an ATEX may form by illustrating real-world scenarios faced by various industries. For example, one case study involving a chemical plant revealed that improper storage practices led to significant dust accumulation in specific areas—prompting them to reevaluate their existing procedures based on proper classification of areas according to relevant regulations. This resulted in more stringent housekeeping measures and improved segregation between hazardous zones.
Another example comes from an oil refinery where regular inspections uncovered gas leaks that could potentially create explosive atmospheres if left unaddressed; this prompted immediate action toward implementing more robust monitoring systems alongside reclassifying certain operational zones based on updated risk assessments related specifically around gas emissions. These instances highlight not only the importance but also practical applications surrounding how businesses identify locations at risk for forming dangerous atmospheres while adhering strictly to established guidelines within the framework provided by ATEX regulations.
Key ATEX Regulations Every Safety Expert Should Know
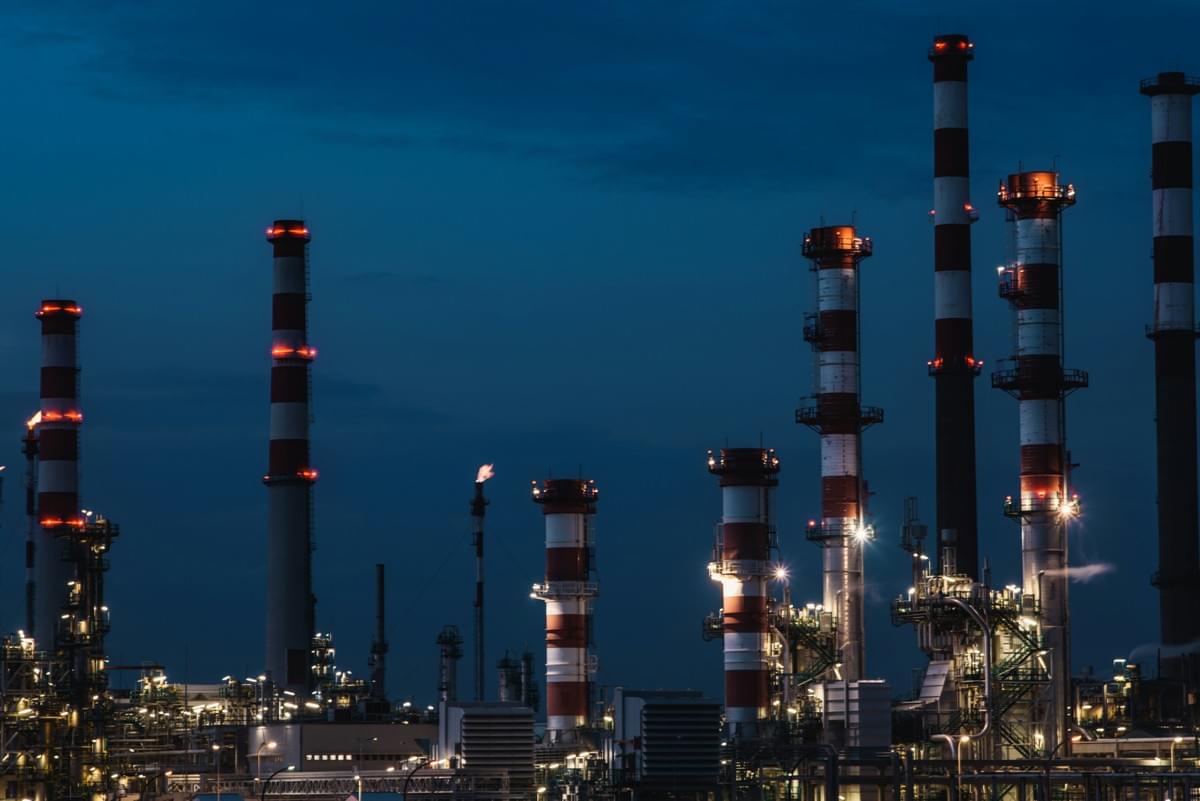
Navigating the world of ATEX regulations can feel like wandering through a maze without a map. However, understanding these directives is crucial for safety experts who aim to ensure compliance and protect workers in hazardous environments. In this section, we’ll explore the key ATEX regulations that every safety professional should have on their radar.
Overview of ATEX Directives
ATEX, an abbreviation for ATmosphères EXplosibles, refers to the European Union directives aimed at ensuring safety in environments where explosive atmospheres may occur. The two primary directives are ATEX 99/92/EC (which focuses on minimum requirements for improving the health and safety protection of workers) and ATEX 2014/34/EU (which deals with equipment intended for use in potentially explosive atmospheres). Understanding what an ATEX zone entails is essential, as these directives provide the framework for classifying areas, identifying locations where an ATEX may form, and ensuring that all necessary precautions are taken.
By grasping these directives, safety experts can effectively demarcate ATEX zones within their facilities. This process involves careful consideration of various factors such as potential sources of ignition and types of flammable materials present. Furthermore, compliance with these regulations is not just about ticking boxes; it’s about fostering a culture of safety that prioritizes employee well-being in potentially dangerous environments.
Essential Compliance Steps for Businesses
For businesses operating in industries susceptible to explosive atmospheres, compliance with ATEX regulations is non-negotiable. The first step involves conducting a thorough risk assessment to identify locations where an ATEX may form based on existing hazards and operational practices. Following this assessment, companies must classify their work areas according to the types of hazards present—whether gas or dust—to ensure appropriate measures are implemented.
Next comes the crucial task of how to demarcate ATEX zones effectively; this includes marking boundaries clearly and using appropriate signage to inform employees about potential risks associated with each zone classification. Regular training sessions should also be organized to keep staff updated on best practices relating to equipment use and emergency procedures within these classified areas. By following these essential compliance steps diligently, businesses can significantly mitigate risks associated with explosive atmospheres.
The Role of Jinrong in ATEX Industry Standards
Jinrong plays a pivotal role in shaping industry standards related to ATEX zone classification by providing innovative solutions tailored specifically for hazardous environments. As a leader in manufacturing explosion-proof equipment, Jinrong ensures its products meet stringent regulatory requirements outlined by both EU directives and international standards alike. Their expertise not only aids companies in achieving compliance but also enhances overall workplace safety through cutting-edge technology designed for hazardous areas.
Moreover, Jinrong actively participates in discussions surrounding best practices related to how to demarcate ATEX zones effectively across various industries—from oil refineries to food processing plants—ensuring that all stakeholders understand what constitutes an adequate response plan when dealing with potential hazards. By collaborating closely with regulatory bodies and industry leaders alike, Jinrong helps set benchmarks that elevate safety standards across sectors prone to explosive atmospheres.
In conclusion, understanding key ATEX regulations is paramount for any safety expert looking to navigate the complexities surrounding hazardous work environments successfully while ensuring compliance at every level.
Conclusion
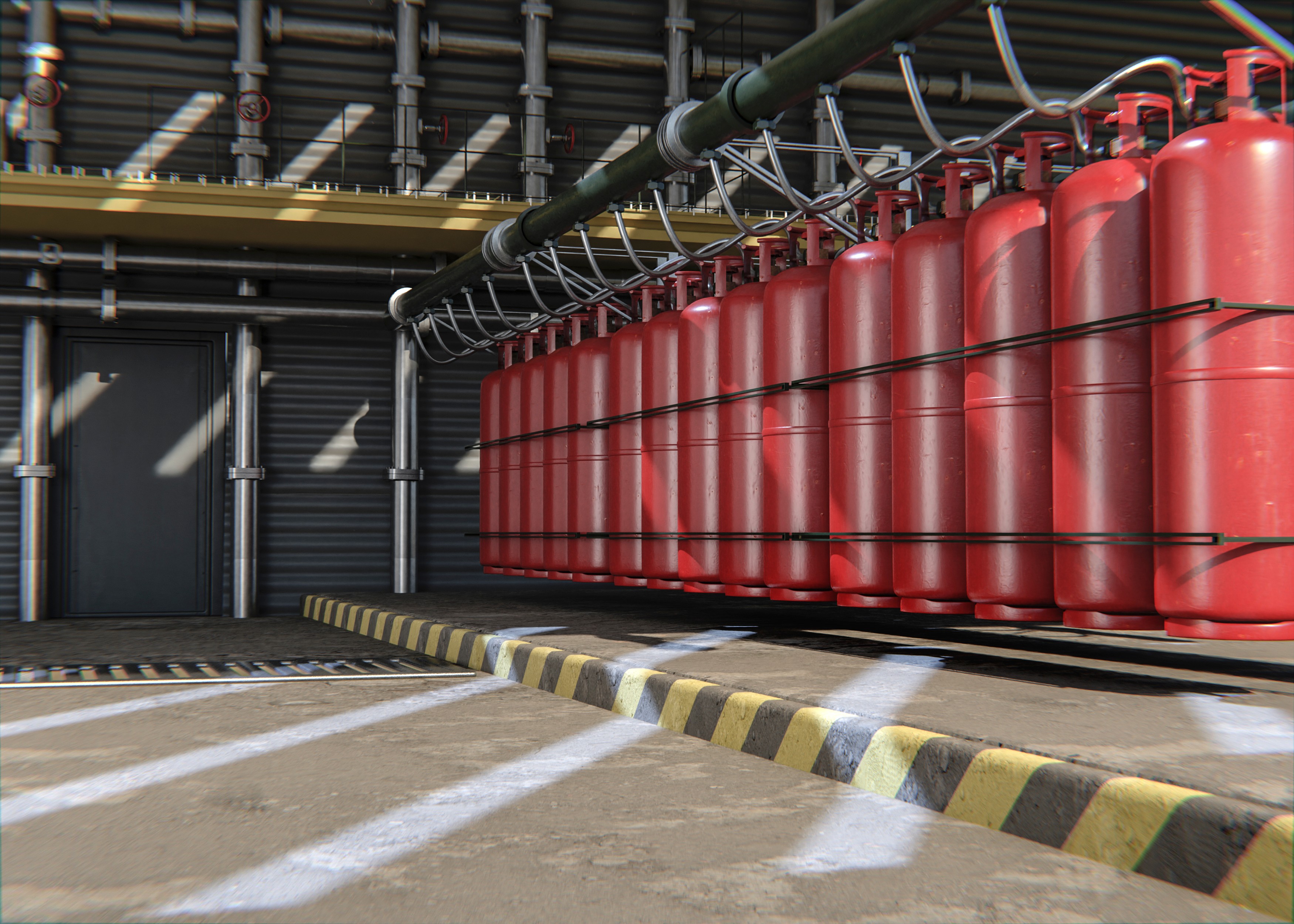
As we wrap up our exploration of ATEX zone classification, it’s clear that understanding what an ATEX zone is and how to demarcate ATEX zones is crucial for ensuring workplace safety in hazardous environments. The classification of areas plays a pivotal role in identifying locations where an ATEX may form, allowing businesses to implement necessary precautions effectively. With the right knowledge of ATEX regulations and guidelines, safety experts can significantly mitigate risks associated with explosive atmospheres.
Recap of ATEX Zone Classification Principles
ATEX zone classification involves categorizing areas where explosive gases or dust may occur, thus helping businesses maintain compliance with essential safety standards. By defining what an ATEX zone is, we can better understand the importance of this classification in protecting both personnel and property from potential hazards. The principles behind how to demarcate ATEX zones involve assessing various factors such as material properties and environmental conditions that contribute to the risk of explosion.
Ensuring Safety Through Effective ATEX Management
Effective management of ATEX zones not only ensures compliance with regulations but also fosters a culture of safety within organizations. By regularly reviewing the classification of areas and identifying locations where an ATEX may form, companies can proactively address potential risks before they escalate into dangerous situations. Implementing robust training programs around ATEX regulations further empowers employees to recognize hazards and take appropriate action when necessary.
Resources for Further ATEX Training and Knowledge
For those eager to deepen their understanding of ATEX zone classification, numerous resources are available for further training and knowledge enhancement. Online courses, industry workshops, and comprehensive guides on how to demarcate ATEX zones provide valuable insights into best practices for maintaining compliance with regulations. Engaging with professional organizations dedicated to safety standards can also offer networking opportunities and access to the latest developments in the field.